Od ponad 100 lat firma Wilson Sporting Goods jest znana na całym świecie jako lider w obszarze produkcji sprzętu sportowego, artykułów miękkich i innych akcesoriów sportowych. Zespół badawczo-rozwojowy Wilsona posiada niezbędne oprogramowanie, sprzęt i materiały, aby objąć cały proces projektowania produktu, od koncepcji i projektu, przez prototypowanie, aż po produkcję na pełną skalę. Ostatnio zespół firmy Wilson mocno zaangażował się w obszarze wytwarzania przyrostowego, współpracując z wieloma firmami z branży, wciąż ulepszając swoje produkty i wprowadzając innowacje w sferze ich szybszego i bardziej wydajnego wytwarzania. Kluczowymi partnerami Wilson są Nexa3D – producent superszybkich, fotopolimerowych drukarek 3D oraz Addifab – firma dostarczająca części formowane wtryskowo przy pomocy narzędzi drukowanych w 3D.
Glen Mason – kierownik ds. zaawansowanych innowacji/industrializacji w DeMarini (oddział firmy Wilson Sporting Goods) stwierdza, że firma wciąż dopiero stawia pierwsze kroki w druku 3D – „dopiero dotykamy powierzchni wytwarzania przyrostowego. Chcemy nie tylko przyspieszyć cykle iteracji oprzyrządowania i projektowania, ale także zastanawiamy się, jak uzyskać gotowe do produkcji formy bez konieczności testowania komponentów badawczo-rozwojowych. W pracy korzystamy z drukarki 3D firmy Nexa3D i platformy FIM (Freeform Injection Molding) firmy Addifab”.
Mason dołączył do zespołu badawczo-rozwojowego DeMarini Sports/Wilson wiele lat temu i posiada duże doświadczenie w branży formowania wtryskowego tworzyw sztucznych. „System Nexa3D x Addifab ma tak wiele zalet, że mój zespół jest w stanie wyeliminować kilka etapów podczas projektowania nowych narzędzi, pozwalając skupić się na innych projektach i znacznie zmniejszając ilość odpadów i czasu potrzebnego na przetestowanie naszych projektów” — mówi Mason.
Zespół badawczo-rozwojowy firmy Wilson poszukiwał skuteczniejszego sposobu produkcji prototypowych narzędzi do formowania wtryskowego dla linii młodzieżowych rękojeści kijów bejsbolowych. Aby wdrożyć zmiany projektowe w istniejącej rękojeści kija, zespół ds. rozwoju produktu poszukiwał alternatywnego procesu prototypowania, aby skrócić czas potrzebny do wyprodukowania tych części na hali produkcyjnej. Odchodząc od tradycyjnych metod obróbki metalu, zespół najpierw zajął się przeprojektowaniem komponentu wykorzystując druk 3D jako jedyny sposób na wyprodukowanie tej formy.
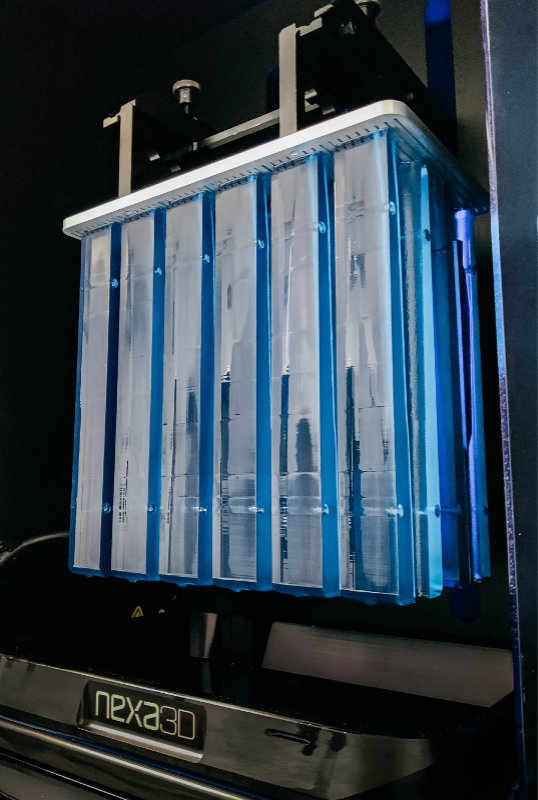
Przed przejściem na technologię Nexa3D i Addifab, zespół projektowy Wilson używał tradycyjnych metod produkcji ubytkowej do wytwarzania narzędzi do prototypów plastikowych form wtryskowych. Chociaż oprzyrządowanie metalowe jest zazwyczaj znacznie sztywniejsze i solidniejsze niż oprzyrządowanie polimerowe, istnieje kilka ograniczeń projektowych, które należy wziąć pod uwagę, zanim przejdzie się w fazę koncepcji projektu. Ponadto, prowadząc globalną działalność produkcyjną, Wilson szukał również sposobów na skrócenie cyklu życia projektu produktu i przyspieszenie czasu wprowadzania produktu na rynek.
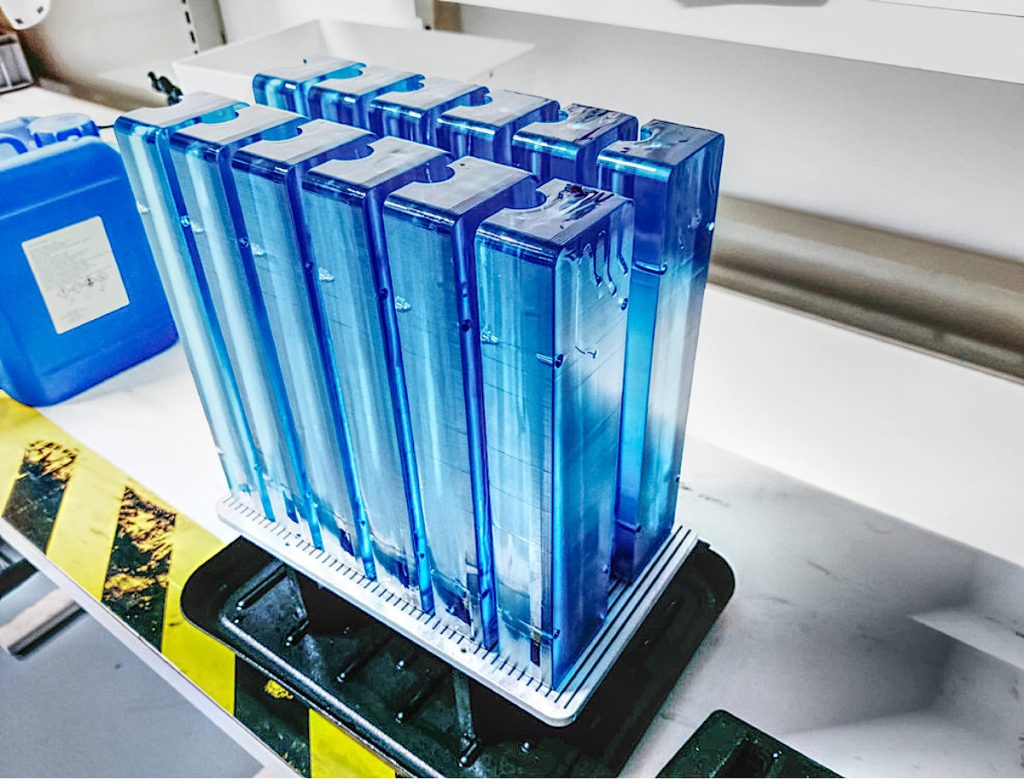
„W ciągu ostatnich dwóch lat uważnie przyglądaliśmy się naszym łańcuchom dostaw, a także próbowaliśmy zrozumieć, w jaki sposób możemy wytwarzać bardziej przyjazne dla środowiska i zrównoważone produkty. Sprowadza się to do wytwarzania produktów bliżej miejsca, w którym są używane oraz do projektowania i wytwarzania produktów, które zużywają mniej odpadów, wykorzystując materiały nadające się do recyklingu i mają bardziej oszczędne procesy projektowania” — wyjaśnia Mason.
Partnerstwo z Nexa3D i Addifab przyniosło inżynierom Wilson kilka natychmiastowych korzyści. Dzięki dużemu obszarowi roboczemu w drukarkach 3D Nexa3D i ultraszybkiemu procesowi LSPc, grupa badawczo-rozwojowa Wilsona może teraz szybko produkować wiele części jednocześnie, co pozwala na wiele iteracji projektu w jednej partii wydruku 3D. Ponadto to, co wcześniej składało się z kilku komponentów, można teraz wydrukować w postaci pojedynczej części, skracając czas montażu i zwiększając jej trwałość.
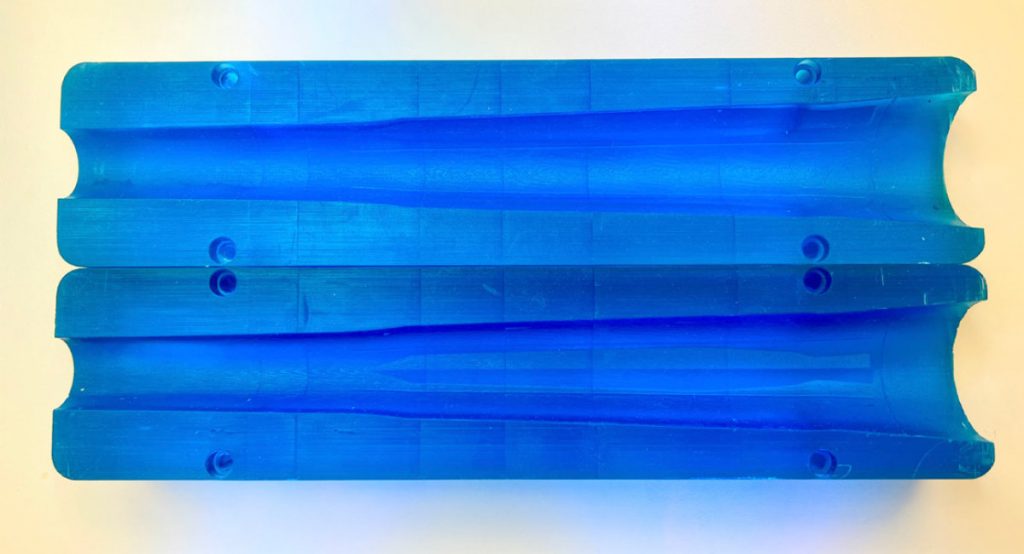
Dzięki Addifab projektanci zajmujący się badaniami i rozwojem mają znacznie większą elastyczność projektowania i dostęp do szerszej gamy materiałów w porównaniu z tradycyjnymi metalowymi narzędziami do formowania wtryskowego tworzyw sztucznych. „Nasi projektanci mogą teraz pozwolić sobie na tolerancję dla tych narzędzi, podczas gdy w przypadku narzędzi metalowych nawet kilka mikronów może zmienić pierwotny projekt. Dodatkowo, dzięki autorskiemu materiałowi żywicznemu Addifab, nie ma obaw o adhezję lub wiązanie tworzyw sztucznych podczas procesu formowania wtryskowego” – powiedział Mason.
Wyjaśnił, że w tym przedsięwzięciu przyjęto kilka celów, z których dwa najważniejsze to „w jaki sposób możemy skrócić czas potrzebny na wprowadzenie nowych projektów na rynek” oraz „jakie nowe technologie możemy wykorzystać, aby skrócić cykl rozwoju produktu, zmniejszyć zużycie materiału dzięki mniejszej iteracji prototypów i poprawić ogólny projekt komponentów dla tych nowych projektów”?
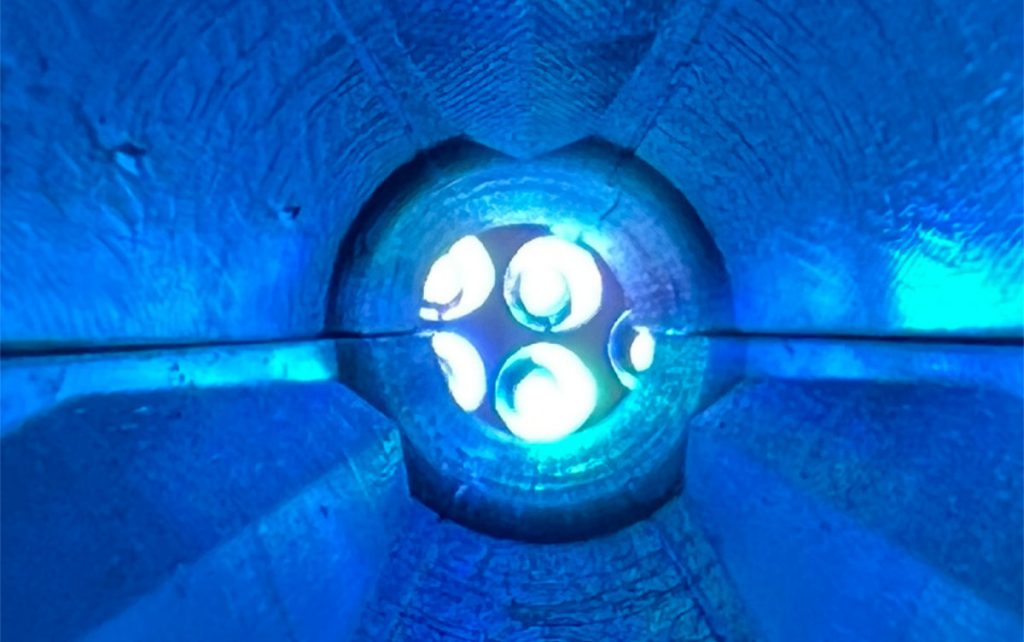
Po opracowaniu wstępnej koncepcji zespół badawczo-rozwojowy może zazwyczaj opracować prototyp w ciągu jednego dnia roboczego – proces, którego stworzenie wcześniej zajęłoby miesiące. Istnieje prosty, trzyetapowy proces, gdy inżynierowie z firmy Wilson podejmą decyzję o stworzeniu prototypu:
- Wydrukuj formę – dzięki szybkiemu procesowi drukowania LSPc Nexa3D i dużej objętości roboczej, inżynierowie Wilson R&D mogą zazwyczaj wydrukować w 3D wiele prototypowych narzędzi na jednym wydruku. W niedawnym teście zespół produkcyjny był w stanie wydrukować łącznie 6 różnych form (12 sztuk) w ciągu około 9 godzin. Wcześniej alternatywą było albo wytwarzanie narzędzi do metalu przez kilka tygodni/miesięcy – i to w takim przypadku tylko dla jednej opcji projektowej, albo po prostu w ogóle nie rozpoczynać podróży projektowej.
- Plastikowe formowanie wtryskowe części – ponieważ nowy proces przypomina formowanie izolatora termicznego zamiast przewodnika, gorący materiał polimerowy wpływa znacznie łatwiej do formy. Zmniejsza to ryzyko błędów procesu i znacznie obniża ciśnienie wymagane do uformowania części, co przekłada się na niższe ciśnienie w zagłębieniu i mniejsze odkształcenie drukowanej formy.
- Obróbka końcowa – użycie systemu utwardzania Addifab i rozpuszczalnej żywicy, zanurzenie części w zbiorniku i pozostawienie płynu do rozpuszczenia się z podłoża to jedyne prace związane z obróbką końcową potrzebne do uzyskania gotowej części. Ten alkaliczny roztwór usuwa wnękę polimeru, pozostawiając gotowy element nienaruszony, gotowy do przetestowania.
„To, co niegdyś zajmowało naszemu warsztatowi mechanicznemu miesiące, teraz zajmuje zaledwie kilka dni, aby odwrócić iteracje projektowe” — mówi Mason – „wyeliminowaliśmy również dwa dodatkowe kroki w naszym procesie opracowywania produktu i pozwalamy na minimalną interakcję niezbędną do przejścia do pierwszego testu”.
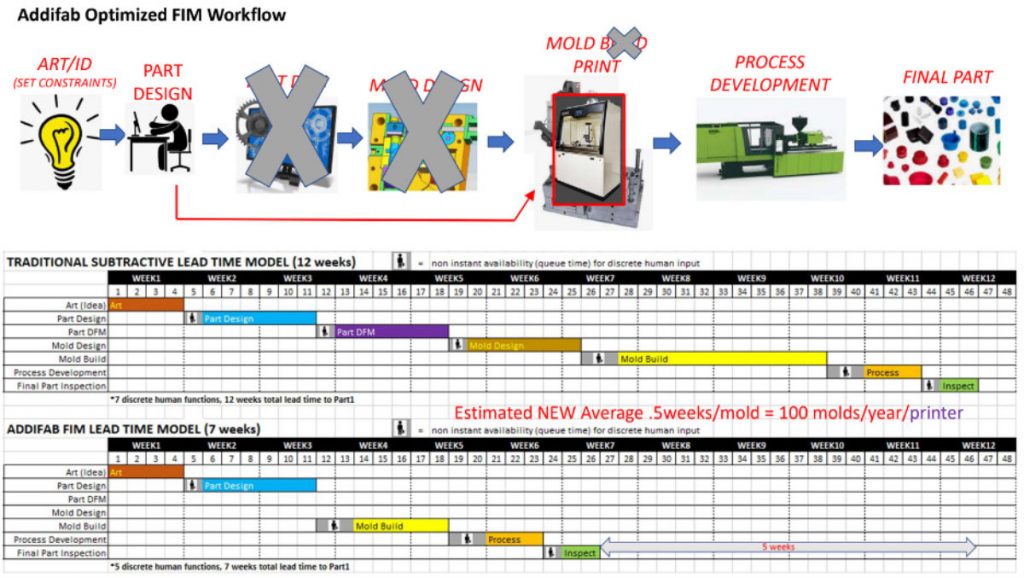
„Ponieważ możemy o wiele szybciej wykonywać iteracje, drukować narzędzia szybciej niż obrabiać maszynowo i eliminować kilka etapów procesu. Pomaga nam to znacznie skrócić czas wprowadzania produktów na rynek, umożliwiając szybkie i sprawne podejmowanie decyzji projektowych. Nie musimy też już martwić się tradycyjnymi ograniczeniami DfM, takimi jak: gdzie umieścić bramę, jak materiał będzie przepływał przez część, wypaczenie/odchylenie części, a nawet ścisłe tolerancje, w porównaniu z naszą poprzednią produkcją narzędzi”.
Chociaż Wilson Sporting Goods jest klientem Addifab od kilku lat, naturalna ekspansja relacji nastąpiła, gdy Addifab ogłosił partnerstwo z Nexa3D, umożliwiające znaczne zwiększenie możliwości technologii FIM. „Ukończyliśmy około 15 różnych projektów w okresie dziewięciu miesięcy, podczas gdy wcześniej byliśmy w stanie zrealizować tylko kilka projektów w tym samym czasie” — wyjaśnia Mason – „nasze długoterminowe plany obejmują włączenie tej technologii i nowego procesu projektowania do kolejnych linii produktowych Wilsona jak golf, tenis i inne”.
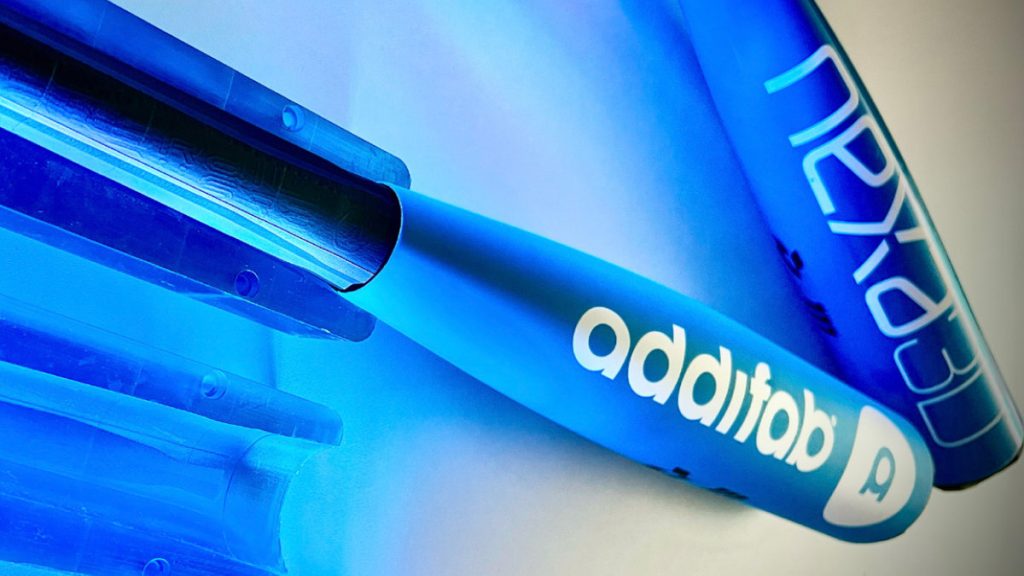
Wilson w dalszym ciągu zamierza wykorzystywać rozwiązania Nexa3D i Addifab w tworzeniu nowych innowacji i ulepszeń w istniejących liniach produktów. Zespół już używa tego samego przepływu pracy do koordynowania prac projektowych dla sąsiednich linii produktów i będzie to nadal robić. Chociaż dość trudno jest zastąpić trwałość i możliwości oprzyrządowania do produkcji metalu, zespół ds. rozwoju produktów firmy Wilson nieustannie przesuwa granice możliwości, wykorzystując wytwarzanie przyrostowe jako swoje podstawowe narzędzie.
Wyłącznym dystrybutorem Nexa3D Polsce jest 3D Phoenix. Zapytaj co może zmienić w Twoim biznesie: info@3dphoenix.pl.
Źródło: materiały prasowe 3DPhoenix