GE Additive wraz z upływem kolejnego roku obecności w branży addytywnej ma coraz większy wpływ na obecny kształt przemysłu – wdrażanie rozwiązań opartych o technologie przyrostowe w kolejnych firmach prowadzi do optymalizacji procesów produkcji i wytwarzania. Trwający proces wprowadzania technologii addytywnych do zakładów produkcyjnych możliwy jest m.in. dzięki Concept Laser, firmie od lat związanej z branżą przemysłowego druku 3D, należącej do GE Additive.
Zarząd oddziału firmy Bosch w Bamberg (Niemcy) zdecydował się na wprowadzenie w swoim cyklu produkcji elementów, które zostaną wyprodukowane z zastosowaniem technologii addytywnych. Mowa o głowicach smarujących, które pomimo niewielkich rozmiarów maja kluczowe znaczenie dla płynnego przepływu pracy.
W filii firmy w Bamberg produkowane są między innymi systemy wykorzystywane do wtrysku paliwa w silnikach. Nieodzownym elementem ich produkcji są głowice olejowe – małe elementy wykorzystujące olej do nawilżania gwintów dla optymalnego dopasowania między dwoma komponentami. Jest to szczególnie ważne w przypadku nowej generacji wtryskiwaczy, gdzie materiały cechują różne właściwości powierzchni, przez co bez odpowiedniego środka smarującego wykazują dużą tendencję do wzajemnego tarcia.
Wnikliwa analiza sposobu nanoszenia smarowidła na powierzchnie komponentów wykazała, że części wtryskiwaczy jest pokrywana olejem jedynie z jednej strony, przez co tworzą się tzw. martwe punkty. Miejsca niekompletnie pokryte smarem generują niepożądane opory tarcia, które przyczyniają się do powstawania potencjalnych uszkodzeń elementów, generujących kosztów dla firmy (które wynikają m.in. z konieczności nawet krótkotrwałego zatrzymania produkcji).
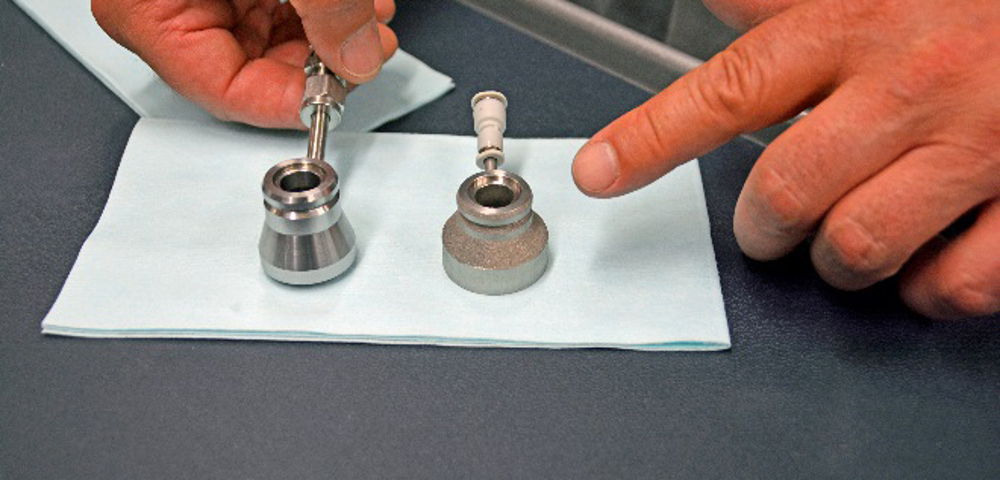
Przeprowadzone badania wykazały, że część musi zostać poddana optymalizacji – zmieniony został jej kształt, a technologia przyrostowa pozwoliła na wykonanie elementu nie w czterech częściach (tak jak wytwarzany był wcześniej), ale jednej. Detal został przeprojektowany – zmniejszyła się jego wielkość, a także został wyposażony w sieć kanałów smarujących, pozwalając na wydajniejsze smarowanie elementów przy jednocześnie lepszym pokryciu olejem również trudno dostępnych miejsc.
Jeśli chodzi o materiał to wybór padł na stop CoCr – niekorodujący, mocny materiał, który zachowa swoje właściwości mechaniczne na długi czas, bez jakichkolwiek uszkodzeń. Optymalne parametry druku przestrzennego w systemie Mlab Cusing od Concept Laser, umożliwiały wykonanie kilku niewielkich głowic z zachowaniem pełnej precyzji, odpowiedniej dla produkcji niewielkich elementów.
Według Wolfganga Schliebitza, odpowiedzialnego za planowanie i nadzór prac w firmie, wytworzenie elementów tym sposobem dla Bosch był jednoznaczny z obniżeniem kosztów, wykluczając nakłady finansowe na montaż oraz skróceniem czasu projektowania.
Części wykonane w technologii addytywnej poprawiły wydajność procesów produkcyjnych – pozytywny feedback spowodował, że drukowane 3D głowice smarujące zostały również wprowadzone w czterech innych zakładach firmy we Francji, Niemczech, Korei Południowej i Turcji.
Źródło: Materiały prasowe