Ultimaker słynie z angażowania się w liczne projekty edukacyjne oraz naukowo-badawcze na całym świecie. W kwietniu br. informowaliśmy, że firma przekazała swoje urządzenie studentom Politechniki Śląskiej, którzy zwyciężyli w konkursie „Ultimaker education challange”. Dziś podczas konferencji prasowej w Łodzi, Holenderski producent ogłosił nawiązanie oficjalnej współpracy z łódzkim Bionanoparkiem, któremu przekazał na testy swój flagowy model drukarki 3D – Ultimakera 3.
Ultimaker to jeden z dwóch największych producentów niskobudżetowych drukarek 3D na świecie. Firma jest znana z tego, że cały czas podąża za trendami i udoskonala swoje produkty. Jest to możliwe dzięki współpracy z ośrodkami, które wykorzystują druk 3D w swojej codziennej pracy. Jak to wygląda w praktyce? Ultimaker wybiera firmę, która wyróżnia się na tle konkretnej branży i oferuje jej testowanie swoich najnowszych urządzeń w zamian za fachową recenzję sprzętu i wykonanych wydruków.
W wyniku współpracy CD3D oraz get3D – autoryzowanego dystrybutora produktów Ultimaker na Polskę, Ukrainę i Mołdawię, jako ośrodek testowy wybrano łódzką Pracownię Indywidualnych Implantów Medycznych z Bionanoparku.
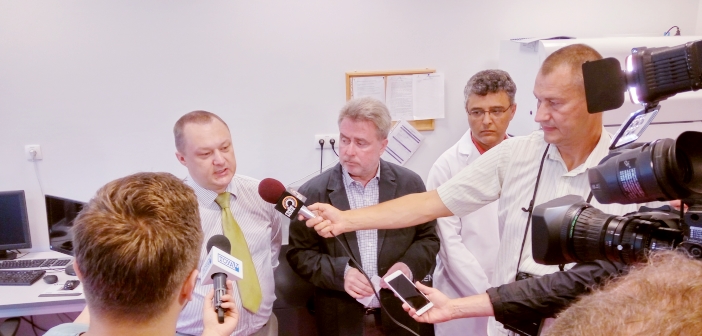
Pracownia zajmuje się projektowaniem i wytwarzaniem implantów medycznych, które dopasowane są do struktur anatomicznych konkretnego pacjenta oraz drukowaniem w technologii 3D fizycznych modeli anatomicznych, które służą do zaplanowania zabiegu operacyjnego lub do formowania implantów z odpowiedniego materiału. W kontekście branży medycznej jest to więc idealny partner dla Ultimakera.
Pracownia na co dzień korzysta już ze starszego modelu drukarki 3D producenta – Ultimakera 2. „Trójka” otwiera przed Pracownią dużo większe możliwości za sprawą systemu dwóch głowic drukujących, gdzie jedna jest odpowiedzialna za nakładanie materiału budulcowego (ABS, nylon, PLA), a druga materiału podporowego, którym jest rozpuszczalne w wodzie PVA. W ten sposób oszczędza się czas, konieczny dotychczas do mechanicznego usuwania tego materiału. Co ważniejsze, to rozwiązanie umożliwia także budowanie bardziej skomplikowanych obiektów, między innymi struktur charakterystycznych dla tkanki kostnej.
W ciągu ostatnich miesięcy mieliśmy okazję przeprowadzić szereg wydruków testowych dla Pracowni z użyciem Ultimakera 3, gdzie sprawdzaliśmy możliwości drukarki 3D w zakresie drukowania skomplikowanych modeli anatomicznych, pochodzących z tomografii komputerowej. Efekty części naszych testów opisywaliśmy na łamach 3D w praktyce.
Pracownia Indywidualnych Implantów Medycznych korzysta z technologii oferowanej przez firmę Ultimaker w pierwszych etapach projektowania zindywidualizowanych implantów, dla których wymagana jest stała konsultacja z chirurgami. Podczas tego procesu tworzy się prototypy implantów oraz odpowiednie modele anatomiczne, które są oceniane przez zespół chirurgiczny i na podstawie ich spostrzeżeń dokonuje się wielu zmian i usprawnień. Ostateczne implanty tworzone są z wykorzystaniem druku 3D lub wielosiowych obrabiarek CNC.
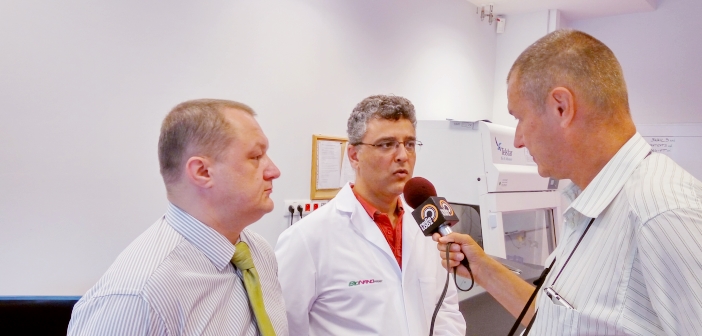