Druk 3D zrewolucjonizował wiele branż, oferując wiele zróżnicowanych metod przyrostowe, takich jak FDM (Fused Deposition Modeling), SLA (Stereolithography) czy Binder Jetting. Wśród nich, selektywne spiekanie laserowe (SLS) z wysokowydajnych polimerów (w szczególności poliamidu PA12), wyróżnia się unikalnymi cechami i zaletami. Największą firmą świadczącą usługi z użyciem metody SLS w Polsce jest Technology Applied, które oferuje produkcję wysokowydajnych części z wykorzystaniem większości metod przyrostowych wymienionych powyżej.
Selektywne Spiekanie Laserowe (SLS) polega na użyciu wiązki lasera do selektywnego spiekania warstwa po warstwie sproszkowanego materiału polimerowego, aż do wytworzenia trójwymiarowego obiektu. Części wykonane z PA12 techniką SLS są znane z wysokiej wytrzymałości, elastyczności i precyzji detali, dzięki czemu metoda ta jest idealna do zastosowań inżynieryjnych i szybkiego prototypowania.
Fused Deposition Modeling (FDM) – najpopularniejsza metoda druku 3D na świecie, wykorzystuje termoplastyczne filamenty, które są topione i nakładane warstwowo. Chociaż FDM jest bardziej przystępne cenowo i proste w użyciu, części wyprodukowane tą metodą często są mniej wytrzymałe i dużo mniej precyzyjne w porównaniu do SLS. Dodatkowo w przypadku bardziej złożonych geometrii niezbędne jest stosowanie struktur podporowych, wykonanych albo z tego samego materiału, albo z materiału podporowego, rozpuszczalnego w wodzie lub chemikaliach. W obydwu przypadkach konieczne jest usunięcie podpór (ręcznie lub chemicznie), co wydłuża czas produkcji części i ma negatywny wpływ na ich końcową estetykę (fragmenty budowane na podporach są zawsze gorsze wizualnie od tych budowanych na stole roboczym drukarki 3D).
Stereolitografia (SLA) używa światła UV do utwardzania żywicy warstwa po warstwie. SLA zapewnia wysoką dokładność i gładkie wykończenie powierzchni, ale produkty są zazwyczaj mniej wytrzymałe niż te wytworzone metodą SLS – domyślnie mają niższą odporność temperaturową i mechaniczną. Ponadto, materiały żywiczne używane w technice SLA mogą być mniej odpornie na działanie czynników środowiskowych w porównaniu z PA12. Jednakże największą różnicą jest post-processing – elementy wykonane z żywic należy najpierw wykąpać w alkoholu izopropylowym (IPA) aby oczyścić je z resztek żywicy, następnie doświetlić UV w dedykowanym urządzeniu, a na koniec usunąć struktury podporowe, które tutaj również występują. W przypadku SLS wystarczy tylko oczyścić je z niespieczonego proszku.
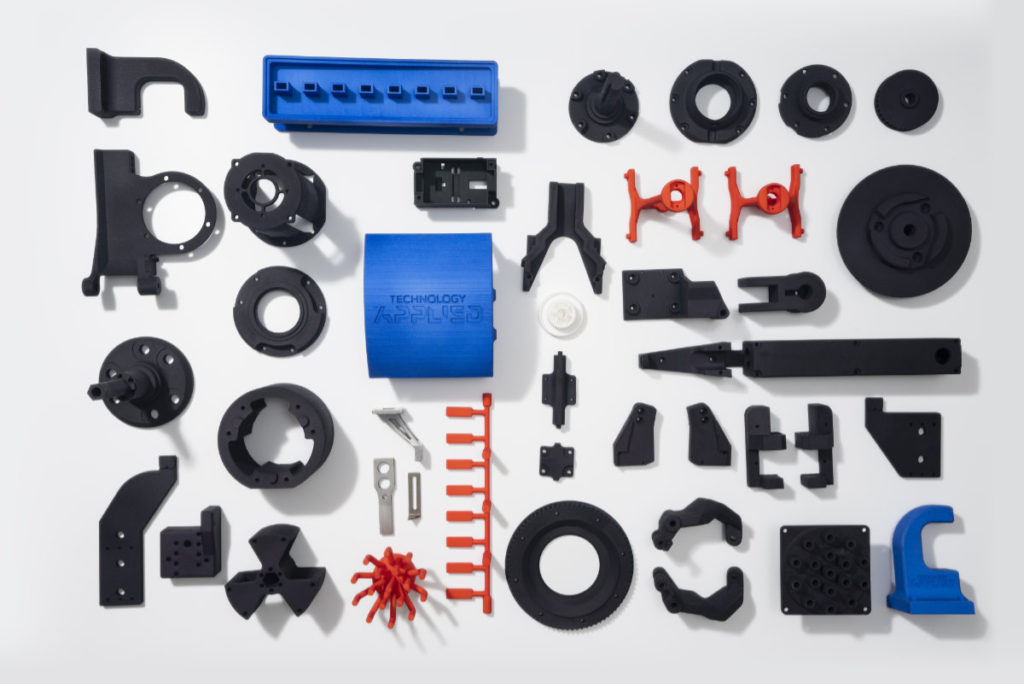
Kolejna popularna metoda przyrostowa – Binder Jetting, polega na nakładaniu wiążącego środka na warstwę proszku (lepiszcza), co pozwala na drukowanie złożonych geometrii. Niestety wytrzymałość mechaniczna i trwałość elementów wytworzonych tą metodą są zazwyczaj niższe niż w przypadku SLS. W przypadku proszków metali, konieczne jest wypiekanie gotowych części aby nadać im niezbędnej trwałości i wytrzymałości. Niestety w trakcie tego procesu części się kurczą (średnio o ok. 20%) w stosunku do wydruku 3D.
Podsumowując, SLS wyróżnia się w druku 3D swoją zdolnością do tworzenia wytrzymałych, funkcjonalnych części z złożonymi geometriami i wysoką dokładnością, bez konieczności użycia struktur podporowych. Jest również bardzo wydajną metodą jeśli chodzi o czas produkcji, gdyż elementy można piętrować w komorze drukarki 3D, całkowicie wykorzystując jej obszar roboczy (w metodach FDM i SLA użytkownik jest zawsze ograniczony powierzchnią stołu w osiach XY). Ta kombinacja cech sprawia, że SLS jest preferowaną metodą w aplikacjach, gdzie wymagana jest wysoka jakość i trwałość, przewyższając inne techniki, takie jak FDM, SLA, czy Binder Jetting, szczególnie w wymagających zastosowaniach przemysłowych.
Technology Applied jako największy dostawca usług druku 3D w Polsce oferuje wszystkie wyżej wymienione techniki addytywne (z wyjątkiem Binder Jetting). Skontaktuj się z firmą, aby poznać kluczowe różnice i wybrać najlepszą dla siebie metodę przyrostową.
Źródło: www.3dprintingcenter.net