W Centrum Druku 3D lubimy pisać o praktycznych zastosowaniach technologii addytywnych tam, gdzie rzeczywiście ma to sens. Dzisiaj dzięki kolegom z 3D Phoenix na przykładzie technologii od Markforged przybliżamy jak branża przemysłowej produkcji spożywczej korzysta lub może korzystać z druku 3D w kontekście ciągłego dostosowywania się do zmieniających potrzeb rynku i oczekiwań konsumentów
Druk 3D umożliwia tworzenie niestandardowych części i narzędzi, które idealnie odpowiadają specyficznym wymaganiom danej linii produkcyjnej. Jest to szczególnie ważne w przypadku produkcji żywności, gdzie każdy produkt może wymagać innej formy opakowania lub sposobu manipulacji.
Narzędzia typu EOAT – Elementy oprzyrządowania krańcowego robotów
Posiadanie odpowiednich narzędzi do obsługi szybko rosnącej liczby jednostek SKU oraz regularnie zmienianych opakowań, co jest obecnie powszechne w branży produkcji żywności, może być frustrującym wyzwaniem dla zespołów produkcyjnych. Jak zwiększyć wydajność i elastyczność na linii, gdy sprzęt używany w zeszłym miesiącu nie jest dostosowany do nowego opakowania wprowadzanego na rynek w miesiącu następnym? Jak szybko wprowadzać zmiany, aby dostosować się do wymogów transportu różnych opakowań i zmiennego popytu w obrębie łańcucha dostaw?
Druk 3D części EOAT (elementów oprzyrządowania krańcowego robotów) umożliwia dostosowanie narzędzi niezbędnych w codziennej pracy. Dzięki możliwości drukowania na żądanie firmy mogą znacznie skrócić czas potrzebny na wprowadzenie zmian w linii produkcyjnej, co jest kluczowe w branży, gdzie czas reakcji na zmiany może decydować o sukcesie rynkowym.

Druk 3D popychaczy na liniach pakujących
Zespoły produkcyjne projektują i instalują różnorodne rodzaje popychaczy na liniach pakujących, które służą do rozdzielania, sortowania, odrzucania, wkładania, podawania oraz przełączania pasów. Współczesne fabryki muszą być coraz bardziej elastyczne w zakresie tego, co i kiedy produkują. Drukowanie addytywne poszerza możliwości zespołów produkcyjnych, umożliwiając wytwarzanie niestandardowych komponentów popychaczy na miejscu, co pomaga rozwiązać trudne problemy z rozmieszczeniem, unikalnymi powierzchniami i kątami kontaktu produktów oraz innymi wyzwaniami.
Proces tworzenia niestandardowych elementów popychaczy z Markforged przebiega następująco:
- Określenie, jakie elementy mogą rozwiązać bieżący problem.
- Modyfikacja istniejących projektów lub tworzenie nowej geometrii w CAD.
- Produkcja mocnych, niezawodnych niestandardowych popychaczy na żądanie przy użyciu kompozytu Onyx® klasy przemysłowej.
- Zastosowanie wzmocnienia włóknami ciągłymi (CFR) w celu zwiększenia wytrzymałości lub włókna aramidowego (Kevlar®) w celu poprawy odporności na uderzenia.
- Iterowanie i optymalizacja wydajności części za pomocą funkcji Simulation w Digital Forge™.
Dzięki tym niestandardowym częściom zespoły mogą elastycznie poprawiać wydajność linii produkcyjnej w ciągu godzin, a nie dni, bez dodatkowych opóźnień związanych z oczekiwaniem na wysyłkę i testowaniem specjalistycznych komponentów czy tradycyjnymi cyklami opracowywania nietypowych części. Zatwierdzone i zweryfikowane projekty są dodawane z powrotem do cyfrowego magazynu, gotowe do ponownego wyprodukowania za pomocą jednego kliknięcia. Cały proces odbywa się bez znacznego zwiększania wymagań dotyczących fizycznych zapasów.

Przykład z Australian Meat Processor Corporation (AMPC)
Australian Meat Processor Corporation (AMPC) to korporacja badawczo-rozwojowa dla przemysłu przetwórstwa mięsa w Australii. W dużych zakładach produkcyjnych części takie jak śruby i rolki często ulegają zużyciu lub uszkodzeniu. Jak w każdej innej branży, czas to pieniądz, a awaria części skutkuje utratą produktywności i kosztownymi przestojami.
AMPC i Markforged przeprowadziły pierwsze na świecie próby modelu usług druku 3D. Celem tych prób było umożliwienie australijskim producentom mięsa drukowanie w 3D części do maszyn produkcyjnych, co mogłoby drastycznie usprawnić konserwację sprzętu i zapewnić ciągłą dostawę produktów mięsnych.
Jednym z obiektów, które skorzystały z druku 3D, była spółdzielnia Casino Food Co-op. Od 1933 roku jest to największa w Australii spółdzielnia rolnicza zajmująca się przetwórstwem mięsa na międzynarodowym poziomie. Firma przetwarza 1200 sztuk bydła dziennie i zatrudnia ponad 1000 osób z okolicznych obszarów.
W Casino Food Co-op zidentyfikowano trzy obszary, które udało się poprawić dzięki zastosowaniu druku 3D z Markforged:
- Dzięki możliwości drukowania nowych zawiasów do drukarek etykiet w razie potrzeby, Casino Food Co-op może zapobiegać przestojom maszyn i zapewnić ciągłość drukowania etykiet. Ponadto wydłużono żywotność tych drukarek, oszczędzając tysiące dolarów na kosztach wymiany.
- Drukowanie 3D przekładni garbarskiej pozwoliło na wydrukowanie tymczasowego zamiennika, który mógł być używany do utrzymania maszyny w ruchu do czasu wyprodukowania nowej przekładni. Dzięki temu przetwarzanie mogło być kontynuowane bez przestojów, co pozwoliło uniknąć znacznych strat.
- Możliwość szybkiego wydrukowania łopatki wentylatora do parowników chłodni przyniosła również znaczne oszczędności kosztów i ograniczenie ryzyka dla firmy. Wcześniej spółdzielnia musiałaby zlecić producentowi stali wykonanie zastępczej łopatki, której koszt wynosiłby do 10 000 USD za sztukę. Teraz wydruk 3D zamiennego elementu zajmuje zaledwie kilka dni i kosztuje ułamek ceny nowej stalowej łopatki, zapewniając znaczące korzyści dla firmy.
Druk 3D nie jest odpowiedzią na wszystkie problemy w branżach przemysłowych, ale identyfikacja tych obszarów, gdzie jego zastosowanie ma rzeczywisty sens i wdrożenie odpowiedniej technologii addytywnej potrafi dać efekty naprawdę spektakularne. Utrzymanie ruchu w zakładach produkcyjnych nie tylko w branży spożywczej, ale w wielu innych jest właśnie takim obszarem.
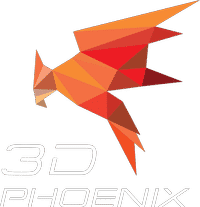
3D Phoenix jest wyłącznym Dystrybutorem Markforged w Polsce.
Zapytaj co może usprawnić w Twoim biznesie: kontakt@3dphoenix.pl.