Mimo że technologia druku 3D z metalu liczy sobie już blisko 30 lat, wciąż jest postrzegana przez wiele osób jako coś nowatorskiego. W gruncie rzeczy nie powinno to dziwić – koncepcja tworzenia detali ze sproszkowanych stopów metali może być dla osób nie mających na co dzień styczności z metodami addytywnymi faktycznie czym niezwykłym i niecodziennym. Jak zawsze w tego typu przypadkach, rzeczywistość jest dużo bardziej prozaiczna i nie tak spektakularna jak mogłoby się to na pierwszy rzut oka wydawać… W niniejszym artykule przybliżymy na czym polega proces druku 3D z metalu oraz czym różnią się od siebie poszczególne warianty tej technologii o dziwnie brzmiących nazwach DMLS, SLM czy EBM…?
Zacznijmy od wyjaśnienia różnic w nazewnictwie. Na dobrą sprawę DMLS, SLM czy LS to zastrzeżone nazwy handlowe tej samej technologii selektywnego przetapiania sproszkowanych metali przy pomocy lasera, nanoszonych warstwa po warstwie, aż do uzyskania gotowej, w pełni wytrzymałej części. Początkowo nazwa SLM (Selective Laser Melting) była używana równolegle przez MCP Hek oraz EOS, jednakże pierwsza z firm zastrzegła ją, a niemiecki EOS był zmuszony do wymyślenia własnej nazwy – DMLS (Direct Metal Laser Sintering). Z kolei Concept Laser (należący do koncernu GE) określa tę technologię mianem Laser Cusing.
Drukarki 3D drukujące w technologii DMLS nie używają filamentów – modele powstają z bardzo drobno sproszkowanego stopu metalu (np. stal nierdzewna, aluminium, nikiel lub tytan). Proszek ten jest następnie formowany w wyjątkowo cienkie warstwy, dlatego niezmiernie ważny jest jego nienaganny kształt i równomierna ziarnistość, by można go było łatwo wyrównać. Każda warstwa powinna mieć tę samą wysokość (i mówimy tutaj o dokładności mierzonej w mikronach), dlatego opracowanie precyzyjnego proszku ma kluczowe znaczenie w tej technologii.
ZOBACZ RÓWNIEŻ: Do czego wykorzystywać technologię druku 3D z metalu, a kiedy należy jej unikać?
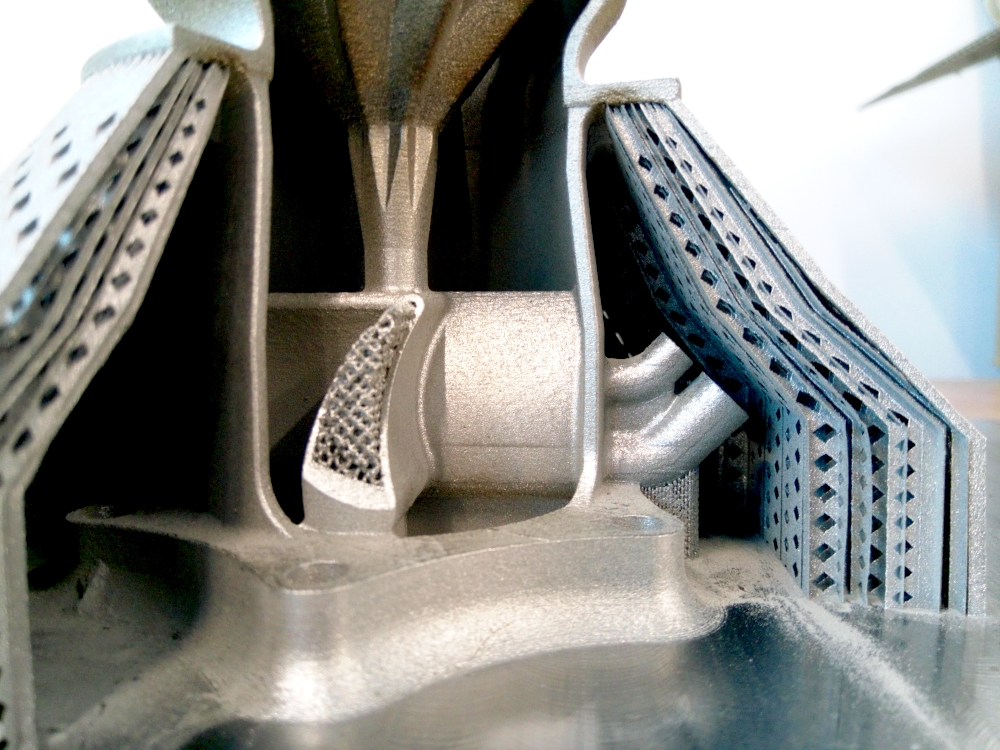
Jak to działa? Komora robocza maszyny jest podgrzewana do zadanej temperatury w celu zapewnienia właściwej stabilności termicznej. Na platformie roboczej rozprowadzana jest super cienka warstwa metalu. Laser, w który wyposażona jest drukarka 3D, wysyła wiązkę światła, która stapia proszek – proszek nie stopi się aż do momentu, gdy osiągnie odpowiednią temperaturę. Wiązka lasera „dotyka” punktów na warstwach modelu, temperatura tych obszarów wzrasta aż do osiągnięcia momentu, w którym materiał się spieka i voilà! – mamy spieczoną warstwę. Drukarka 3D będzie rozprowadzała kolejne warstwy proszku, które będą topione wiązką lasera, aż do osiągnięcia całego modelu.
Po zakończeniu procesu nie można od razu wyjąć wydruku 3D z komory roboczej – zarówno jej wnętrze, jak i materiał muszą wystygnąć w kontrolowany sposób. Następnie należy odciąć detal od płyty, a jeśli model wymagał wygenerowania supportów, należy je również mechanicznie usunąć. Podobnie jak np. w metodach FDM czy SLA, technologia DMLS/SLM wymaga generowania trwałych struktur podporowych. Są one konieczne ze względu na znacznie szybszy skurcz metali, spowodowany dużą różnicą temperatur między atmosferą komory roboczej oraz ciekłym metalem. Podpory są generowane, aby utrzymać detal w miejscu na platformie startowej i zapobiec opadaniu oraz nadmiernemu przetopowi „wiszących” warstw.
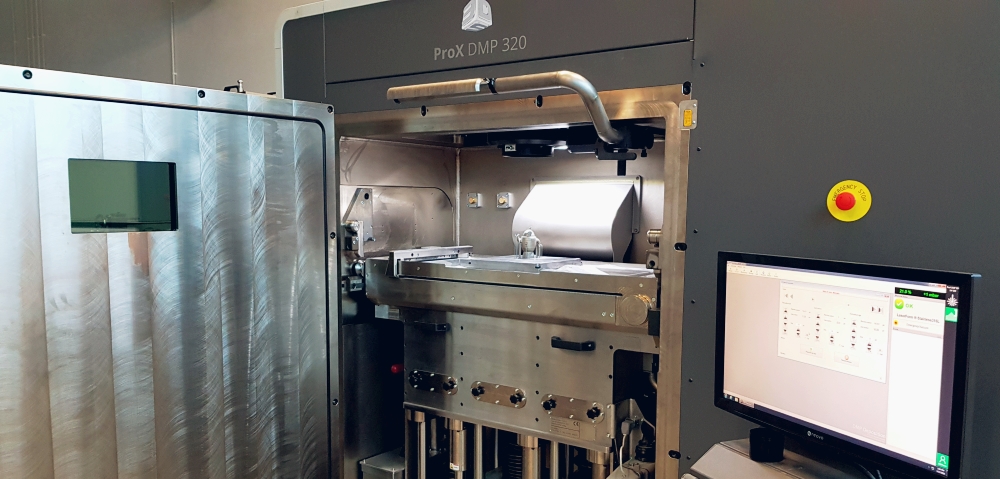
Technologia ta służy do budowania skomplikowanych drobnych i precyzyjnych struktur przestrzennych, których nie można uzyskać za pomocą metod odlewniczych i ubytkowych. Jest wykorzystywana m.in. w produkcji wysoko temperaturowych części do silników lotniczych ze stopów niklu, profesjonalnych implantów medycznych i stomatologicznych, narzędzi do form wtryskowych, biżuterii z metali szlachetnych oraz prototypowania metalowych części.
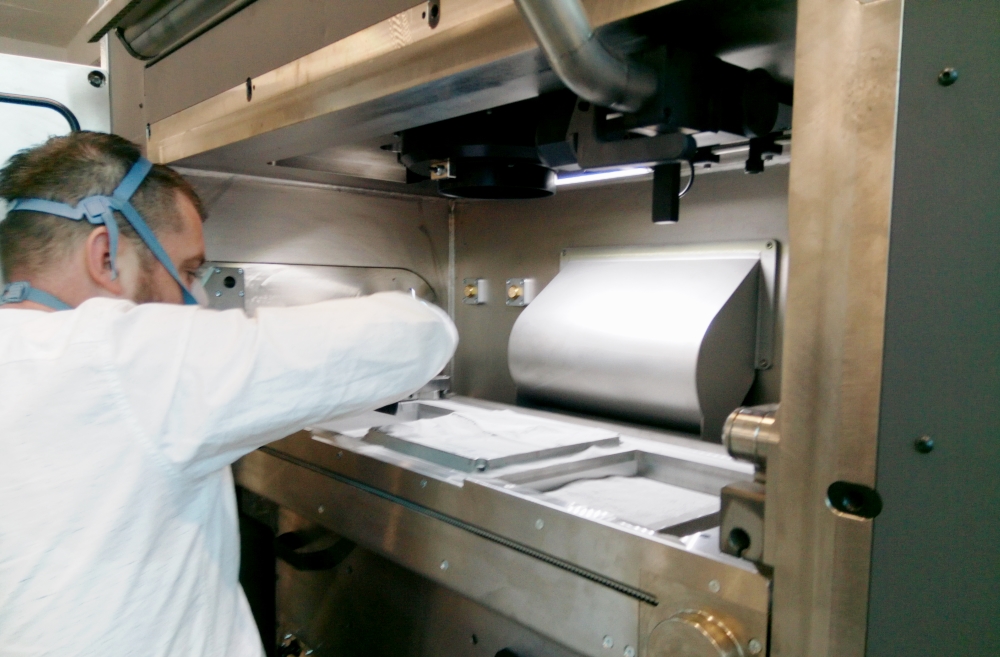
DMLS/SLM pozwala na zaoszczędzenie czasu – jest szybsza od procesu odlewniczego, dzięki możliwości budowania bezpośrednio z danych CAD. Ścianki modeli są niezmiernie wytrzymałe i w zależności od ułożenia mogą mieć grubość sięgającą nawet 0,1 mm. Jej plusem jest ponadto wysoka dokładność wymiarowa oraz powtarzalność budowanych elementów na poziomie od 0,02 do 0,1 mm. Co więcej, duży wybór materiałów zwiększa potencjał produkcji krótkoseryjnej, a niespieczony metal może być wykorzystany nawet w 95-99%.
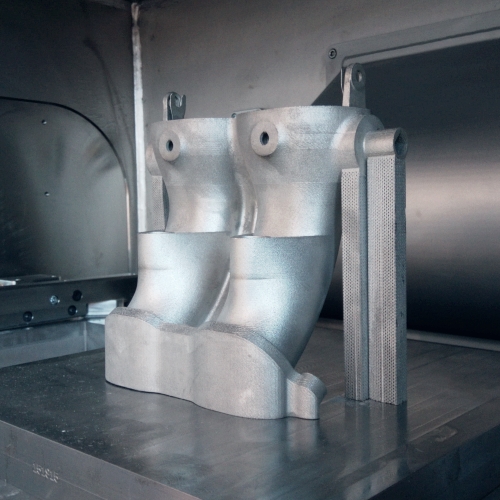
Nie jest to jednak rozwiązanie pozbawione wad. Wymaga ono stosowania struktur podporowych, co znacznie ogranicza geometrię modelu. Wiele trudności przysparza również budowanie dużych powierzchni płaskich ze względu na gradienty temperaturowe podczas spiekania części. Maszyny do druku 3D z metalu są bardzo drogie. Wpływają na to bezpośrednio koszty poszczególnych komponentów przemysłowych drukarek 3D takich jak skaner galwanometryczny czy laser iterbowy. Niemniej jednak ceny te są współmierne do tego, co można osiągnąć dzięki urządzeniom tego typu.
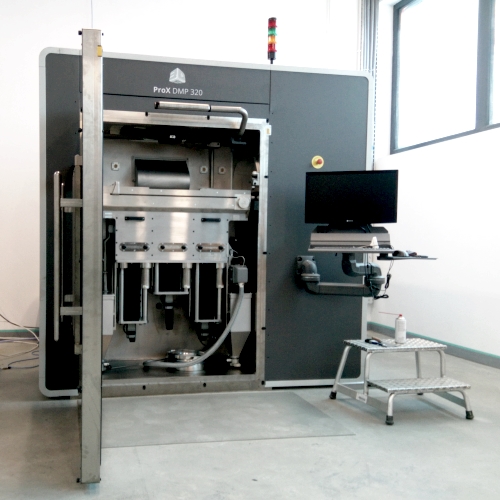
Przejdźmy teraz do nieco mniej powszechnej technologii druku 3D z metalu – EBM (Electron Beam Melting) czyli spiekanie za pomocą wiązki elektronów. Różnica pomiędzy wcześniejszymi technologiami a tą jest taka, że każda warstwa modelu jest spiekana przy pomocy zogniskowanego strumienia elektronów tak, by obecna warstwa została całkowicie spieczona i trwale połączona z poprzednią. Proces zachodzi w komorze próżniowej by zapobiec rozpraszaniu promienia elektronowego przez atomy gazu.
Firma, która przyczyniła się do rozwoju EBM, to Arcam AB należąca do koncernu GE. W 1993 r. złożono wniosek patentowy dotyczący urządzenia do budowy elementów metalowych poprzez spajanie warstw sproszkowanego materiału, przy pomocy wysokoenergetycznego promienia cząstek obdarzonych ładunkiem dodatnim lub ujemnym, o znamionach przetapiania wiązką elektronową w szwedzkim urzędzie patentowym. Cztery lata później patent ten stał się własnością firmy. Następnie wraz z Uniwersytetem Technologicznym Chalmers w Goeteborgu zaczęła rozwijać tę metodę aż do jej pełnej komercjalizacji. W 2002 r. na rynku pojawiły się pierwsze maszyny dedykowane dla branży implantologicznej – EBM S12, która doczekała się kilku ulepszeń.
Technologia EBM znajduje szerokie zastosowanie w produkcji implantów medycznych ze względu na wysoką gęstość i czystość struktury metalicznej. Oprócz tego stosuje się ją w produkcji części dla przemysłu kosmicznego i lotniczego oraz do prototypowania części metalowych. Jest zdecydowanie szybsza od DMLS i SLM, jednak należy pamiętać o tym, że oferuje dużo mniejszą dokładność budowanych elementów i gorszą jakość powierzchni, przez co większość części inżynieryjnych, wymaga dodatkowej obróbki skrawaniem. Z drugiej strony, nie wymagają one obróbki, głównie ze względu na tempo całego procesu.
Bardziej skomplikowanie wygląda również wytwarzanie sproszkowanych metali dla tej technologii. By uzyskać niektóre znormalizowane stopy przy użyciu EBM, należy stosować stopy o nieco zmienionym składzie procentowym w stosunku do składu stopu docelowego. Przetapianie stosowanego w lotnictwie TiAl6V4 tą metodą wiąże się z zastosowaniem stopu o podwyższonej zawartości aluminium, gdyż znaczna część tego niskotopliwego pierwiastka na skutek wysokiej energii promieniowania elektronowego wyparowuje w trakcie procesu. Gdyby nie jego zbilansowany skład, otrzymalibyśmy materiał o dużo niższej zawartości aluminium niż żądana.
EBM to technologia o wysokim potencjale rozwoju. Charakteryzują ją wysokie tempo budowania skomplikowanych elementów metalowych oraz niskie ceny materiałów eksploatacyjnych, a w dodatku nie wymaga ona obróbki termicznej i tak licznych struktur podporowych jak w przypadku DMLS/SLM. Z drugiej strony, powstająca w niej powierzchnia ma niższą jakość, podobnie wygląda to także w przypadku dokładności wymiarowej. Stosowanie tej technologii wiąże się również z częstą wymianą włókna działa elektronowego (100-200h) oraz wysokim pobieraniem energii elektrycznej.