Druk 3D to bardzo pojemna definicja dla szeregu technologii różniących się od siebie procesami wytwórczymi, materiałami jakie są w nich wykorzystywane oraz rodzajem obiektów, jakie można z nich wykonać. Na chwilę obecną możemy wyróżnić kilkadziesiąt metod produkcyjnych, które można określić mianem przyrostowych – niektóre z nich różnią się między sobą drobnymi niuansami technicznymi, inne stanowią całkowicie odrębne procesy wytwórcze nie posiadając poza nazwą „druk 3D” praktycznie żadnych cech wspólnych.
W niniejszym opracowaniu prezentujemy najważniejsze technologie addytywne w kontekście ich zalet, wad i różnic co jak mamy nadzieję, pomoże Państwu zrozumieć czym jest druk 3D, czy znajdzie zastosowanie w kontekście Państwa aplikacji – a jeśli tak, to z którego konkretnego rozwiązania powinniście skorzystać?
Zacznijmy od podstawowej rzeczy, czyli definicji druku 3D:
DRUK 3D – metoda wytwórcza polegająca na nakładaniu materiału budulcowego warstwa po warstwie i jego selektywnym spajaniu.
Alternatywnymi i równorzędnymi nazwami dla druku 3D są:
- technologia przyrostowa
- technologia addytywna.
Szczegółowe informacje na temat druku 3D znajdziecie Państwo w poniższych artykułach:
Jakie technologie druku 3D wyróżniamy?
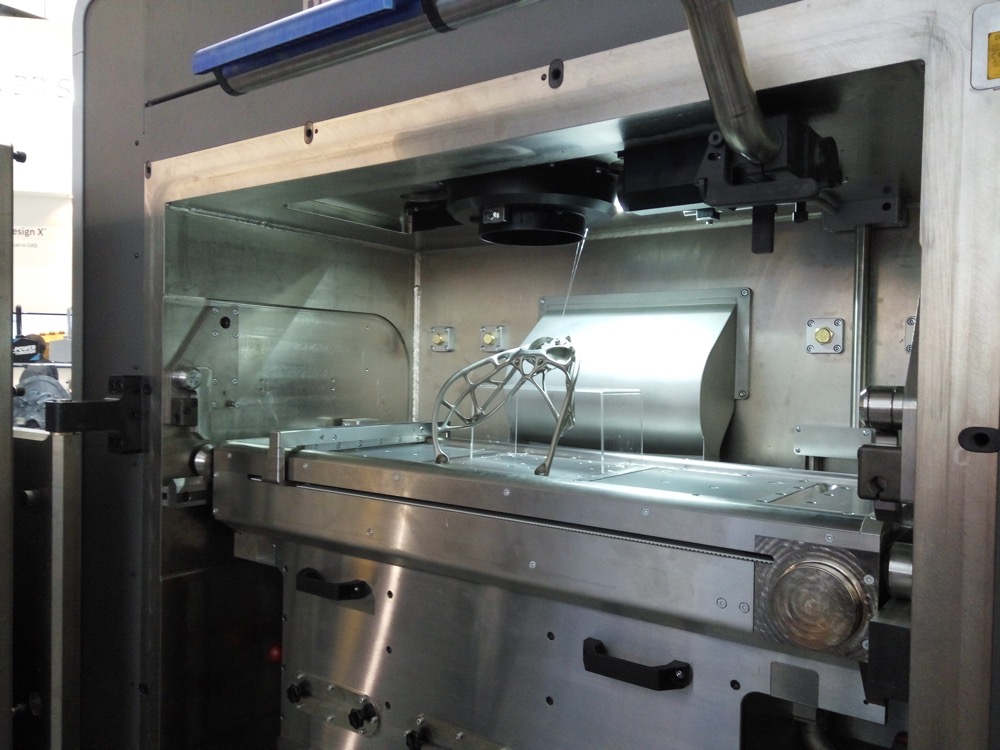
Tak jak wspomniano powyżej, w ramach druku 3D możemy zdefiniować co najmniej kilkadziesiąt różnych technik wytwórczych. Wielu producentów drukarek 3D rozwijając daną metodę addytywną często patentuje jej unikalną część, tworząc z formalnego punktu widzenia odrębną technologię, mimo że co do zasady wywodzi się ona w prostej linii z czegoś, co funkcjonuje na rynku od kilkunastu-kilkudziesięciu lat. Dla uproszczenia możemy spróbować je podzielić na cztery główne grupy ze względu na postać w jakiej do drukarki 3D danego typu dostarczany jest materiał budulcowy:
- materiał w postaci żyłki (drutu)
- materiał w postaci płynu (żywicy światłoutwardzalnej)
- materiał w postaci proszku
- pozostałe (hydrożele i inne materiały półpłynne, masy budowlane lub spożywcze oraz techniki które wyszły już z powszechnego użycia, jak np. druk 3D z folii lub papieru).
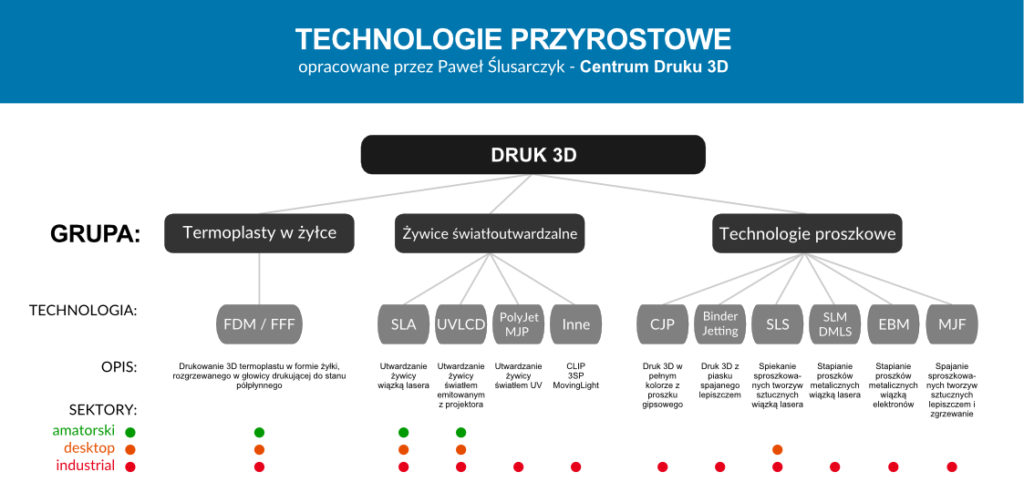
TERMOPLASTY W FORMIE ŻYŁKI / DRUTU:
- FDM – druk 3D z termoplastów w żyłce
- segment przemysłowy (>100.000 PLN)
- segment prosumer (20.000 – 100.000 PLN)
- segment desktopowy:
- urządzenia do użytku komercyjnego (3000 – 20.000 PLN)
- urządzenia amatorskie, w tym zestawy do samodzielnego montażu (500 – 3000 PLN)
ŻYWICE ŚWIATŁOUTWARDZALNE:
- SLA – druk 3D z żywic utwardzanych wiązką lasera
- segment przemysłowy
- segment desktopowy
- DLP – druk 3D z żywic utwardzanych światłem projektora
- segment przemysłowy
- segment desktopowy
- PolyJet / MJP – druk 3D z żywic utwardzanych światłem UV
- pozostałe technologie fotopolimerowe:
- 3SP
- MovingLight
- CLIP
- inne
TECHNOLOGIE PROSZKOWE:
- CJP (dawne 3DP) – druk 3D z proszków gipsowych w pełnym kolorze
- Binder Jetting – druk 3D z piasku lub sproszkowanego metalu
- SLS – druk 3D ze sproszkowanych tworzyw sztucznych spiekanych laserem
- MJF – druk 3D ze sproszkowanych tworzyw sztucznych klejonych selektywnie i zgrzewanych
- SLM / DMP / DMLS – druk 3D ze sproszkowanych metali topionych laserem
- EBM – druk 3D ze sproszkowanych metali topionych wiązką elektronów
- inne…
Do kategorii “inne” możemy zaliczyć całą masę metod wytwórczych, których twórcy w dość naciągany sposób próbują wpleść drukowanie przestrzenne. Są to np.:
- biodrukowanie 3D, wywodzące się z bioplotowania, czyli zautomatyzowanego sposobu nakładania / zakraplania materiału biologicznego (lub hydrożelowego)
- drukowanie 3D z betonu (drukowanie 3D domów), czyli nakładanie mas budowlanych techniką zbliżoną do FDM, będącą de facto zrobotyzowaną techniką nakładania betonu z pompy
- druk 3D żywności, gdzie możemy nakładać masy żywieniowe na podobnej zasadzie jak hydrożele w biodrukowaniu 3D, czy masy budowlane budując w ten sposób obiekty przestrzenne (niestety do tej pory nikt nie znalazł jakiegokolwiek przydatnego zastosowania tej metody w życiu codziennym).
W niniejszym opracowaniu skoncentrujemy się na najpopularniejszych, najpowszechniejszych i najczęściej wykorzystywanych technologiach druku 3D porównując je do siebie i próbując wykazać, która jest najlepsza z punktu widzenia danej aplikacji.
Kiedy wybrać technologię druku 3D?
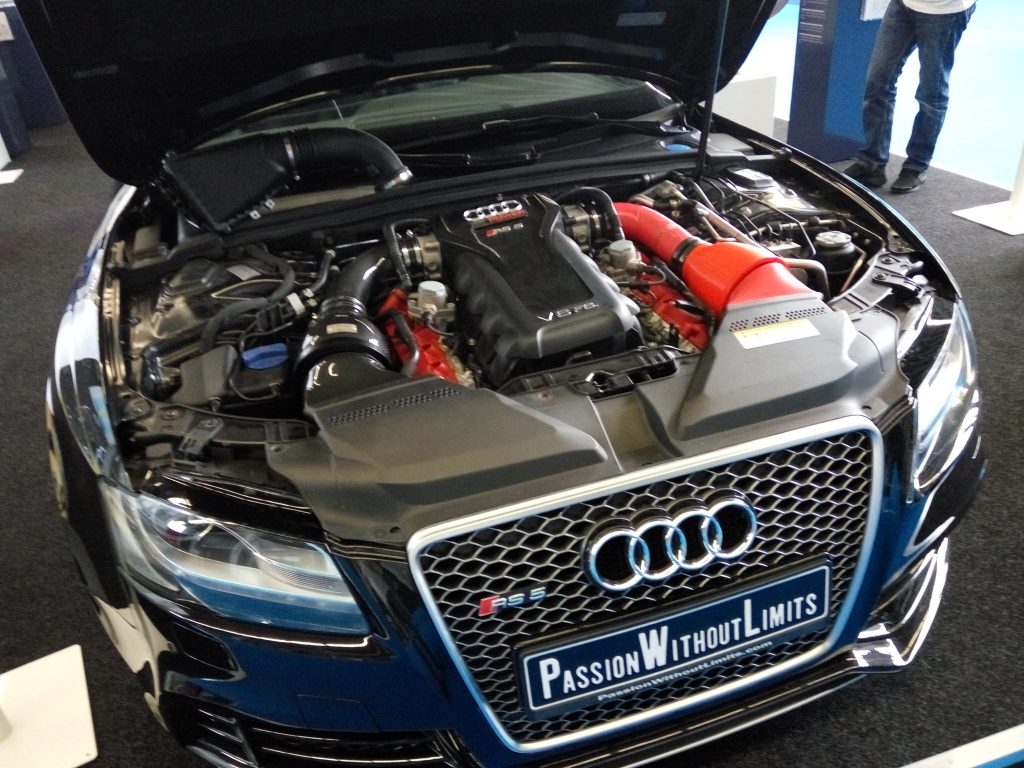
Druk 3D to taka sama technologia wytwórcza jak każda inna – jej celem jest produkowanie rzeczy w określony sposób, z określonych materiałów. Pewne aplikacje da się wykonać na drukarkach 3D lepiej niż na maszynach innego typu, pewne wyjdą gorzej – znajdziemy też takie, których wydrukować się nie da, lub których drukowanie 3D jest ekonomicznie nieuzasadnione. Historycznie, technologie przyrostowe zostały powołane do życia jako alternatywny sposób wykonywania prototypów. Przewagą tej metody nad innymi były i są przede wszystkim:
- szybki czas wykonania modelu
- niski koszt wykonania modelu
- możliwość szybkiego nanoszenia zmian
- wysoka opłacalność tworzenia pojedynczych egzemplarzy i/lub niskich serii
- możliwość personalizacji.
Kolejną zaletą jest możliwość drukowania bardzo skomplikowanych geometrii, niemożliwych do wykonania za pomocą innych metod wytwórczych (dotyczy w szczególności technik wykorzystujących proszki).
ZALETY DRUKU 3D:
- jest najszybszy
- jest najtańszy
- ma możliwość tworzenia najbardziej skomplikowanych geometrii
WADY DRUKU 3D:
- jest słaby pod względem jakości powierzchni
- jest nieefektywny przy produkcji wysoko seryjnej (setki tysięcy – miliony sztuk detali)
Technologię druku 3D wybieramy wtedy, gdy potrzebujemy wyprodukować coś relatywnie szybko, tanio i w ilościach nie przekraczających kilkuset – kilku tysięcy sztuk, a równocześnie nie zależy nam na jakości powierzchni takiej jak w technologii formowania wtryskowego lub odlewniczej.
TECHNOLOGIE DRUKU 3D
FDM / FFF: druk 3D z termoplastów w formie żyłki

Jedna z najpopularniejszych i najbardziej rozpowszechnionych technologii druku 3D. Występuje w trzech wymiarach: amatorskim, desktopowym i przemysłowym. Chociaż zasada działania w każdym przypadku jest dokładnie taka sama, drukarki 3D z sektora amatorskiego nie są w stanie dobrze i dokładnie drukować z materiałów klasy profesjonalnej, które z kolei nie stanowią większego wyzwania dla maszyn klasy przemysłowej (mowa m.in. o poliamidach, materiałach wzmacnianych włóknem węglowym lub szklanym etc.).
Technologia polega na tworzeniu detali poprzez dostarczania tworzywa sztucznego w formie żyłki do głowicy drukującej i rozgrzewania go do stanu półpłynnego. Głowica drukująca nakłada materiał na stole roboczym w osiach XY „rysując” kształt pojedynczej warstwy. Gdy skończy, głowica albo podnosi się do góry, albo stół roboczy opuszcza się w dół o zadaną wysokość warstwy i nakładana jest kolejna warstwa. Półpłynne tworzywo sztuczne spaja się pod wpływem wysokiej temperatury i szybko zastyga tworząc jednolitą strukturę. Różnica w nazewnictwie (FDM / FFF) wynika z faktu, że FDM jest nazwą handlową zastrzeżoną przez twórcę tej technologii – firmę Stratasys.
Zalety:
- możliwość drukowania z szerokiego spektrum tworzyw sztucznych, w tym z tych samych materiałów, jakie są wykorzystywane w technologii formowania wtryskowego; możliwość drukowania 3D z materiałów kompoztowych domieszkowanych np. włóknem węglowym lub szklanym
- tanie materiały eksploatacyjne i eksploatacja drukarek 3D; łatwe i szybkie serwisowanie co ma znaczenie przy produkcji niskoseryjnej
- szybkość pracy – niewielkie detale o prostej geometrii drukuje się w czasie nawet kilkunastu minut; detale średnich rozmiarów, nie przewyższających kilkunastu centymetrów w osiach XYZ drukuje się w czasie kilkunastu godzin, a więc często podczas jednego dnia roboczego
- post-processing – nie licząc skomplikowanych geometrii, gdzie musi zostać wygenerowanych dużo struktur podporowych, post-processing jest prosty, a czasem wręcz na drukarkach 3D da się od razu wyprodukować gotowy do użycia detal.
Wady:
- niezbyt duża dokładność w porównaniu z innymi metodami wytwórczymi – wysokość drukowanej warstwy w technologii FDM / FFF to standardowo 0,1 – 0,3 mm (oczywiście można próbować drukować na niższej lub dużo wyższej warstwie w zależności od potrzeb); standardowa średnica głowicy drukującej to 0,4 mm (czyli otworu, z którego wytłaczany jest półpłynny plastik);
- problemy ze skurczem materiału
- post-processing skomplikowanych geometrii – niektóre geometrie będą wymagać wygenerowania tak skomplikowanych, wewnętrznych struktur podporowych, że ich usunięcie po wydruku będzie albo bardzo skomplikowane, albo niemożliwe.
SLA / UV LCD: druk 3D z żywic światłoutwardzalnych

SLA (stereolitografia) to technika tworzenia detali z żywic światłoutwardzalnych, utwardzanych poprzez naświetlanie ich wiązką lasera. Do pojemnika wlewana jest żywica, w której zanurza się stół roboczy. Jest on opuszczany na wysokość zadanej warstwy (np. 0,05 mm od dna pojemnika), po czym wiązka lasera „rysuje” kształt obiektu w płaszczyźnie XY, utwardzając żywicę. Żywica przywiera do powierzchni stołu roboczego, po czym jest on podnoszony na wysokość kolejnej warstwy i proces się powtarza – tym razem nowa warstwa przywiera do wcześniej utwardzonej.
UV LCD to proces produkcyjny zbliżony do SLA, z tym że żywicę nie utwardza się wiązką lasera, a światłem emitowanym przez ekran LCD z podświetleniem UV zamontowany pod pojemnikiem z żywicą. Zaletą tej metody jest to, że cała warstwa jest naświetlana (utwardzana) równocześnie. Wadą jest to, że przy utwardzaniu dużych powierzchni (o długości / szerokości wyższej niż kilkanaście centymetrów) następuje duży skurcz utwardzanej w tym samym czasie żywicy. Alternatywą dla tej metody jest DLP, gdzie żywica jest utwardzana światłem emitowanym przez projektor.
ZALETY:
- wysoka precyzja drukowanych modeli – możliwość tworzenia detali o warstwie na poziomie 0,025 mm; gwarantuje to gładkość powierzchni najbardziej zbliżoną do formowania wtryskowego lub odlewnictwa
- łatwość usuwania struktur podporowych – nie licząc bardzo skomplikowanych geometrii, z wydruków wykonanych z żywicy bardzo łatwo usuwa się podpory, które są tworzone w zupełnie inny sposób niż np. w FDM / FFF
- świetnie sprawdza się w produkcji niskoseryjnej niewielkich i bardzo precyzyjnych detali
- możliwość stosowania żywic biokompatybilnych – wydruki wykonane z takich żywic mogą być po sterylizacji używane w protetyce, a nawet podczas operacji chirurgicznych i mieć kontakt z tkanką pacjenta.
WADY:
- z uwagi na to, że drukuje się bardziej precyzyjne modele, czas ich wykonania jest dłuższy niż w przypadku FDM / FFF
- o ile świetnie sprawdza się w produkcji małych obiektów, duże detale są problematyczne, a ich poprawne wydrukowanie dużo droższe niż w przypadku FDM / FFF
- wysoka cena materiałów eksploatacyjnych – zwykłe żywice budulcowe są ok. 2-3 razy droższe od termoplastów stosowanych w FDM / FFF i mają słabszą odporność fizyczną i temperaturową; stosowanie bardziej wytrzymałych żywic jest dużo droższe
- konieczność stosowania chemicznego post-processingu – proces druku 3D z żywic jest „brudny” – wydruki są zaraz po zdjęciu ze stołu roboczego pokryte warstwą nie utwardzonej żywicy, którą należy opłukać; wydłuża to czas produkcji i zwiększa koszty.
MJF: druk 3D ze sproszkowanych poliamidów

Technologia opracowana w XXI wieku przez koncern HP. Polega na rozsypywaniu na stole roboczym warstwy sproszkowanego poliamidu PA12 (lub elastycznego TPU) i selektywnym natryskiwaniu lepiszcza, które spaja poszczególne warstwy detalu. Równocześnie materiał jest zgrzewany ciepłem emitowanym przez lampy, tworząc doskonale wytrzymałą strukturę o dowolnej geometrii. Po zakończonej pracy detal należy wydobyć z niezespojonego proszku i oczyścić – odbywa się to w dedykowanej, zautomatyzowanej stacji do post-processingu.
W technologii MJF (podobnie jak w SLS) nie ma konieczności stosowania struktur podporowych, gdyż ich formę spełnia niezespojony proszek. Umożliwia to drukowanie detali o geometriach niemozliwych do osiągnięcia przy uzyciu innych, tradycyjnych technik wytwórczych. Kolejna zaleta systemu MJF to wysoka wydajność produkcyjna – drukarki 3D HP są dostosowane do produkcji niskich serii produkcyjnych i są pod tym względem bez porównania bardziej wydajne niż drukarki 3D pracujące w technologii FDM / FFF oraz SLA i UV LCD.
Kolejna istotna cecha technologii MJF to możliwość druku 3D detali w pełnym kolorze z wykorzystaniem tworzywa sztucznego PA12.
ZALETY:
- możliwość drukowania obiektów z bardzo wytrzymałych i sprężystych bądź elastycznych materiałów
- możliwość drukowania obiektów o skomplikowanych geometriach – z uwagi na to, że jest to technologia proszkowa, proszek, który nie jest spieczony tworzy naturalną strukturę podporową, która po zakończonym wydruku z łatwością się usuwa (chociaż są sytuacje, gdy podpory są mimo wszystko wskazane)
- dużo wyższa precyzja i dokładność niż w technologii FDM / FFF
- technologia dedykowana do produkcji seryjnej (możliwość piętrowania wydruków)
- możliwość drukowania detali o charakterze finalnym
- możliwość stosowania pełnego koloru.
WADY:
- do czasu produkcji należy doliczyć drugie tyle na post-processing (np. 1 dzień druku 3D = 1 dzień na obróbkę detali)
- wydruki w pełnym kolorze są bardzo drogie; domyślny kolor detali to grafitowy
- specyfika procesu technologicznego czyni technologię opłacalną przede wszystkim przy niższych seriach produkcyjnych, lub dużych obiektach o skomplikowanej geometrii; małe i proste rzeczy bardziej opłaca się drukować w innych technikach addytywnych.
DMP: druk 3D z metalu
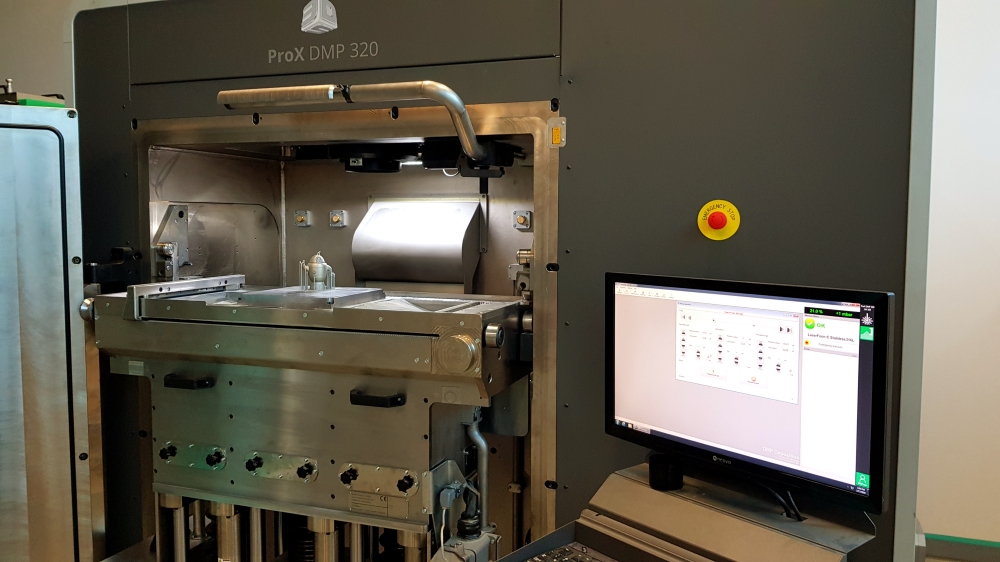
Druk 3D z metalu to jedna z najbardziej pożądanych, a zarazem najtrudniejszych w obsłudze technologii addytywnych. Polega na równomiernym rozkładaniu kolejnych warstw sproszkowanych stopów metali i selektywnym ich topieniu za pomocą wiązki lasera. Drukarki 3D do metalu są maszynami klasy przemysłowej, wykorzystującymi m.in. gazowe atmosfery ochronne. W pracy można wykorzystywać wiele popularnych stopów metali na czele ze stalą nierdzewną, tytanem czy aluminium.
Technologia DMP (direct metal printing) jest autorską metodą przyrostową firmy 3D Systems. Równocześnie na rynku funkcjonuje wiele jej odmian, które co do zasady działają i polegają na tym samym, ale różnią się niuansami technologicznymi – i co za tym idzie nazwą. Techniki o nazwach SLM (selective laser melting), DMLS (direct metal laser sintering) i inne opisują ten sam proces wytwórczy.
Zalety:
- możliwość drukowania detali ze stopów metali
- możliwość drukowania obiektów o skomplikowanych geometriach
- możliwość drukowania bardzo precyzyjnych detali o ściankach o grubości 0,2 mm (lub niższej – zależy od modelu)
- technologia dedykowana do produkcji seryjnej
- możliwość drukowania finalnych detali dla lotnictwa, motoryzacji etc.
- możliwość drukowania implantów medycznych (z tytanu).
Wady:
- wysokie koszty (drogie maszyny + drogie materiały + droga eksploatacja)
- skomplikowany i co za tym idzie długi post-processing
- bardzo skomplikowane przygotowywanie modeli do druku 3D.
Którą technologię wybrać?
Każda z powyższych metod przyrostowych ma szereg zalet i wad. Aby wybrać właściwą musimy poznać specyfikę i oczekiwania wobec tworzonej aplikacji. Czynniki jakie bierzemy pod uwagę w porównaniu to:
- rozmiar
- dokładność odwzorowania szczegółów i wymiarów
- stopień złożoności geometrii
- wytrzymałość:
- wytrzymałość na czynniki mechaniczne (uderzenia, ścierność, ściskanie i rozciąganie)
- odporność temperaturowa
- odporność chemiczna
- liczba wyprodukowanych detali vs. czas produkcji
- koszt produkcji.
FDM | SLA | UV LCD | MJF | DMP | |
---|---|---|---|---|---|
Gabaryt | ***** | ** | * | **** | *** |
Dokładność | * | ***** | **** | ** | *** |
Geometria | * | **** | *** | ***** | ** |
Trwałość | *** | ** | * | **** | ***** |
Liczba szt. | **** | * | ** | ***** | *** |
Cena | ***** | ** | *** | **** | * |
Technologia FDM / FFF znajdzie zastosowanie tam, gdzie w grę wchodzą duże wydruki 3D i ważna jest niska cena. Dobrze sprawdzi się w produkcji niskoseryjnej. W zależności od zastosowanego materiału, wydruki mogą być albo bardzo wytrzymałe (PC, PCABS, PA6) albo tanie (PLA). Nie jest to najlepsza metoda gdy w grę wchodzi wysoka jakość powierzchni detali lub geometria wydruku będzie wyjątkowo skomplikowana.
Technologia SLA jest doskonała w aplikacjach, gdzie ważna jest jakość powierzchni i precyzja realizowanych wydruków 3D. Niestety jest mało efektywna w produkcji niskoseryjnej i jest zdecydowanie dedykowana do produkcji pojedynczych detali.
Technologia UV LCD w niewielkim stopniu ustępuje SLA w kwestii dokładności i różnice w tym obszarze są naprawdę niewielkie. Lepiej sprawdzi się w produkcji niskoseryjnej małych elementów, gdyż jest pod tym względem dużo szybsza od SLA. Wydruki będą też nieco tańsze. Co do zasady jednak, UV LCD i SLA to bardzo podobne metody wytwórcze, różniące się niewielkimi niuansami.
Technologia MJF jest doskonała praktycznie dla każdego typu aplikacji, a jej jedyną wadą może być cena przy produkcji jednostkowych elementów o prostej geometrii, gdzie przewaga FDM / FFF będzi znacząca. To idealna metoda wytwórcza do szybkiej realizacji serii produkcyjnych liczących po kilkadziesiąt / kilkaset / a nawet kilka tysięcy sztuk detali. Niska ocena jakości jest tu dość krzywdząca, ponieważ w rzeczywistości jakość wydruków jest wielokrotnie wyższa od tej, jaką oferuje FDM / FFF.
Technologia DMP posiada jedną, kluczową przewagę nad wszystkimi innymi, a jest to możliwość drukowania detali z metalu. Ten typ materiału determinuje wszystkie pozostałe czynniki porównawcze. Jedno z czym należy się liczyć to cena – druk 3D z metali jest drogi.