Czy kupując drukarkę 3D – bez względu na jej klasę – amatorską, czy desktopową, zastanawialiście się kiedykolwiek na jak długo Wam ona wystarczy? Z pewnością szukaliście informacji czy jest awaryjna – ale czy pytaliście kogokolwiek przed zakupem, do kiedy tak zasadniczo będzie ona działać? Jaka jest realna żywotność dzisiejszych drukarek 3D, co może się w nich takiego popsuć, co wymusi na nas zakup kolejnej oraz czy i kiedy producenci urządzeń tego typu wpadną na pomysł, aby świadomie skracać ich czas pracy?
W naszej krótkiej analizie skupimy się jedynie na niskobudżetowych drukarkach 3D klasy amatorskiej i desktopowej, pomijając całkowicie segment urządzeń przemysłowych. Rynek tych maszyn rządzi się innymi prawami, a i ich specyfika budowy czy warunków pracy jest zupełnie inna. Tym samym pochylimy się jedynie nad najpopularniejszymi urządzeniami na rynku, drukującymi z termoplastów w technologii FDM/FFF oraz z żywic światłoutwardzalnych w technologiach SLA/DLP.
Zacznijmy od tego, że od strony mechanicznej drukarki 3D typu FDM/FFF są bardzo proste w budowie. Nie bez przyczyny w dalszym ciągu są sprzedawane w formie zestawów do samodzielnego montażu, ze złożeniem których poradzi sobie większość osób mających jakiekolwiek zacięcie do majsterkowania. Jest to oczywiście naturalna konsekwencja faktu, że wszystkie urządzenia tego typu wywodzą się w prostej linii z projektu RepRap, gdzie ideą było samodzielne budowanie drukarek 3D z ogólnodostępnych materiałów i podzespołów oraz kompletu części drukowanych na innych drukarkach 3D.
Większość elementów konstrukcyjnych tego typu drukarek 3D jest wykonanych z metalu, a te wykonane z tworzyw sztucznych albo są drukowane w technologiach przyrostowych, albo da się je z powodzeniem takimi zastąpić w przypadku ich uszkodzenia. Jeśli chodzi o tak specyficzne i podatne na uszkodzenia elementy jak głowica drukująca czy sam hotend, na rynku funkcjonuje mnóstwo sklepów, gdzie bez problemu kupimy zamienniki w cenach nie przekraczających kilkudziesięciu (w porywach kilkuset) złotych.
Jedynym krytycznym komponentem, którego uszkodzenie może istotnie wpłynąć na sensowność zakupu nowego urządzenia, jest elektronika sterująca, z tym że to również dotyczy jedynie urządzeń opartych o własne, autorskie rozwiązania. W amatorskich drukarkach 3D wciąż przeważają standardowe elektroniki, których koszty są relatywnie niewielkie. Równocześnie spalenie lub uszkodzenie elektroniki to sytuacje skrajne, gdzie powodem jest zwykle albo jej wada fabryczna, albo mniej lub bardziej świadome uszkodzenie dokonane przez użytkownika.
Pozostałe kluczowe komponenty nie tyle się uszkadzają, ile zużywają, a ich wymiana nie stanowi zwykle większego problemu. Tym samym możemy założyć, że umiejętne obchodzenie się z drukarką 3D, czyszczenie jej oraz okresowa wymiana najbardziej podatnych na zużycie elementów jak np. dysza drukująca sprawią, że urządzenie będzie pracować przez długie lata. Na chwilę obecną wydaje się wręcz, że prędzej technologia FDM/FFF zostanie wyparta przez inne – lepsze i tańsze metody przyrostowe, niż nasza drukarka 3D przestanie być zdatna do użytku.
Oczywiście powyższe stwierdzenie to duża generalizacja i dotyczy jedynie naprawdę dobrych i solidnie wykonanych urządzeń. Jeżeli coś od początku działa źle, nie należy oczekiwać, że po latach użytkowania będzie działać lepiej. Fantastycznym przykładem potwierdzającym pierwsze założenie to drukarka 3D Monkeyfab PRIME, którą użytkujemy nieprzerwanie od jesieni 2014 roku. Urządzenie przeszło oczywiście od tamtego czasu kilka upgrade’ów, jednakże pod względem konstrukcyjnym to wciąż ten sam sprzęt.
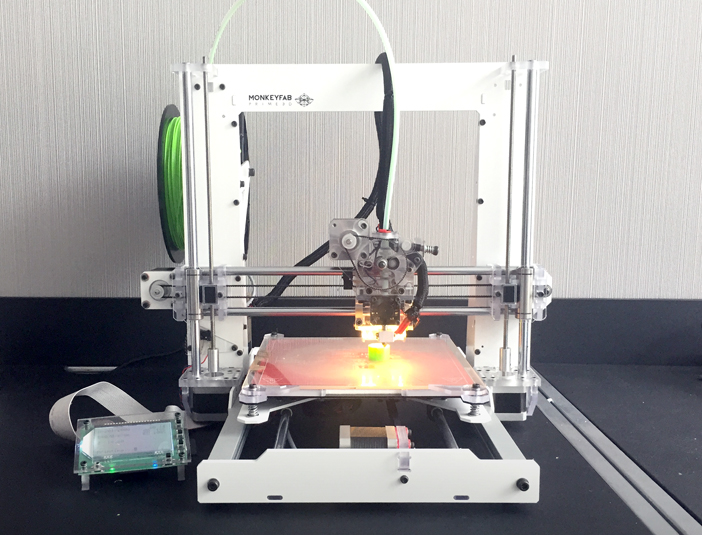
Z drugiej strony, dość podobna konstrukcyjnie drukarka 3D, oparta o ten sam projekt Josefa Prusy – Jelwek Prusa i3 XL to prawdziwe pasmo porażek… Mimo, że urządzenie przeszło całą masę przeróbek, w dalszym ciągu jego jedynym osiągnięciem jest to, że udaje mu się wydrukować „cokolwiek„.

Dość podobnie wygląda to w przypadku fotopolimerowych drukarek 3D, drukujących w technologii DLP. Urządzenia tego typu są jeszcze prostsze w budowie niż urządzenia drukujące z termoplastów, a jedynym elementem, który jest dość drogi i relatywnie szybko się zużywa to lampy projektora, który naświetla żywicę utwardzając jej kolejne warstwy. Ciekawą alternatywą w tym obszarze jest jednak drukarka 3D Liquid Crystal, gdzie projektor został zastąpiony ekranem LCD. W tym przypadku prawidłowo użytkowane urządzenie ma szansę być nieśmiertelne…
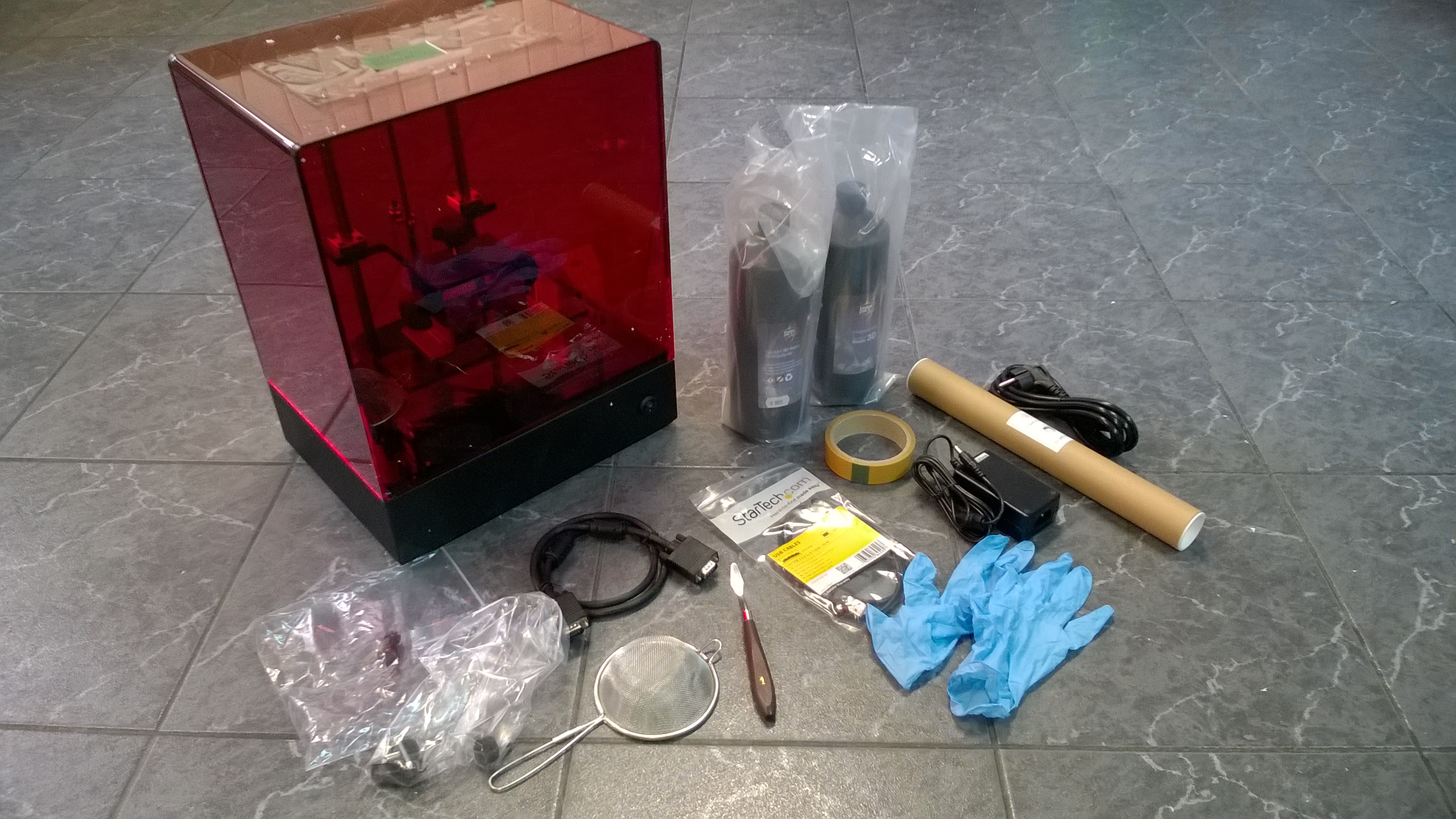
Bardziej skomplikowane pod względem mechanicznym są drukarki 3D typu SLA, jak The Form 2, gdzie kluczowym elementem jest galwo z lustrem, odpowiedzialne za sterowanie wiązką lasera utwardzającego żywicę. Jego uszkodzenie (choć w praktyce jest to dość trudne), może spowodować, że koszty wymiany lub naprawy będą bardzo wysokie.
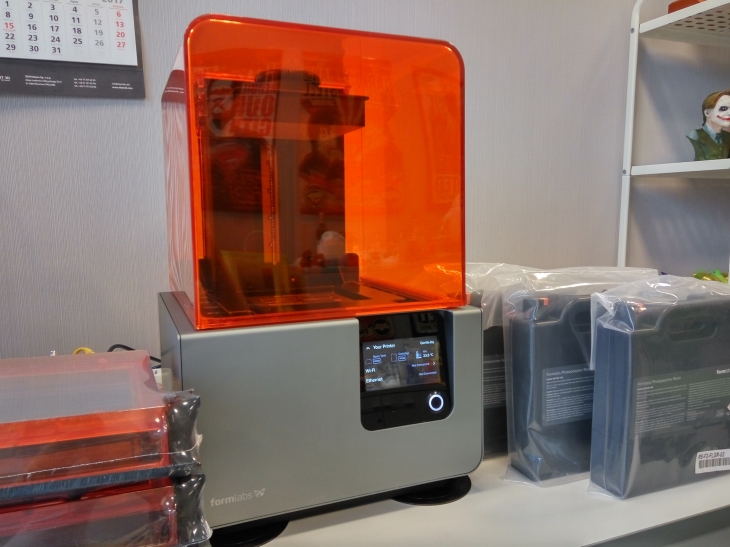
Skoro wiemy już, że drukarki 3D same z siebie się nie psują, po co kupować nowe? Pomijając tak oczywisty powód, jak potrzeba zwiększenia mocy produkcyjnych, jedynym sensownym uzasadnieniem jest zakup urządzenia posiadającego lepsze funkcjonalności, np. dwie głowice drukującej zamiast jednej, komunikacja bezprzewodowa, możliwość stosowania innych, lepszych materiałów eksploatacyjnych etc. Co jednak w sytuacji, gdy wszystko co potrzebujemy drukować to elementy o relatywnie prostej geometrii, wykonywane ze standardowych filamentów? A no nic – drukujemy je cały czas z tej samej, „starej” drukarki 3D.
Dlatego gdy spojrzymy na ostatni raport 3DHubs – 3D Printing Trends Q1-2018, na liście najpopularniejszych drukarek 3D wciąż spotkamy tych samych „starych znajomych„:
- Zortrax M200 (miejsce 3)
- Ultimaker 2 (miejsce 4 – nowsze modele Ultimaker 2+ i Ultimaker 3 zajęły odpowiednio 8 i 11 miejsce)
- MakerBot Replicator 2 i 2X (miejsca 9 i 12)
- The Form 1+ (miejsce 21).
To świetna wiadomość dla użytkowników – niestety dość ponura dla producentów… Jak na razie wszystko wygląda niby ok. – liczba sprzedanych drukarek 3D na świecie dynamicznie rośnie, coraz więcej firm i przedsiębiorstw przekonuje się do technologii przyrostowych, a ci którzy są do nich przekonani od dawna, powiększają istniejące parki maszynowe.
Pytanie brzmi – co w chwili, gdy rynek już do pewnego stopnia się nasyci, a drukarki 3D w dalszym ciągu nie będą się psuć? Czy wzrost innowacji w tak ograniczonej technologii wytwórczej jak FDM/FFF będzie na tyle znaczący, żeby przekonać nas do zmiany działających urządzeń na nowe – ale lepsze?
A może czeka nas to, co dzieje się w świecie urządzeń AGD, czy elektroniki użytkowej – czyli planowane postarzanie produktów? Zmiana wybranych komponentów na takie, które będą psuły się szybciej, a których wymiana będzie bądź na tyle problematyczna lub kosztowna, że bardziej opłacalnym będzie wymiana całego urządzenia? Czy coś co jest plagą w przypadku pralek, lodówek czy zmywarek, dotrze do świata amatorskich i desktopowych drukarek 3D? Co może być zwiastunem takich zmian?
W pierwszej kolejności zastąpienie elementów metalowych plastikowymi. Wyobraźmy sobie, że łożyska na których osadzone będą paski napędowe, będą montowane do plastikowych elementów konstrukcyjnych, połączonych w trwały sposób z obudową. Ich pęknięcie spowoduje konieczność wymiany całej obudowy – co będzie już istotnym kosztem. Taśmy łączące ekstruder z elektroniką będą słabe, a sposób ich montowania będzie powodować, że będą bardziej podatne na uszkodzenie lub przerwanie. Dysza drukująca będzie integralną częścią całego extrudera i jej zapchanie spowoduje konieczność wymiany całego układu… Przykłady można mnożyć…
Jak na razie powyższy scenariusz raczej nam nie grozi – rynek jest wciąż na tyle chłonny, że jego nasycenie to marzenie producentów drukarek 3D, a nie obawa. Niemniej jednak za kilka lat może okazać się, że starego Zortraxa, Ultimakera, czy MakerBota będziemy wspominać z równym szacunkiem i rozrzewnieniem co Mercedesa W123 – popularną „beczkę„, gdzie producent założył, że wał napędowy nie podlega wymianie, bo jest niezniszczalny…
Grafika przewodnia nawiązuje do niesławnego kartelu Phoebusa, założonego w 1923 r. przez Osram, Philips i General Electric, który oficjalnie kontrolował produkcję i sprzedaż żarówek, a w rzeczywistości zajmował się obniżaniem ich jakości, tak aby każda z nich pracowała maksymalnie 1000 godzin (zamiast ok. 2000).