Technologie przyrostowe od kilku dekad znacząco przyspieszają procesy powstawania nowych produktów, a często stanowią nawet impuls do tego, aby daną rzecz w ogóle wymyślić i prędko urzeczywistnić bez ponoszenia wysokich kosztów. Drukarki 3D znajdują zastosowanie praktycznie w każdej możliwej branży i sektorze produkcyjnym, pozwalając rozwijać innowacje w wielu niszowych i specjalistycznych dziedzinach. Przykładem łączącym wszystkie wymienione aspekty jest historia Dirka Dorenbosa z firmy Ropes Edge, który przy pomocy technologii HP Multi Jet Fusion stworzył rodzaj nowego zabezpieczenia chroniącego liny ochronne przed uszkodzeniem w obrębie ostrych krawędzi i z powodzeniem produkuje je i sprzedaje klientom końcowym.
Dirk Dorenbos od 18 lat pracuje jako technik-specjalista stosujący liny w terenie; zajmuje się również szkoleniami, jest kontrolerem i ekspertem ds. IRATA oraz realizuje szereg projektów specjalnych w obrębie komercyjnego transportu linowego. Szczególnie specjalizuje się w zakresie bezpieczeństwa techników wykorzystujących olinowanie w celu dostępu do najbardziej trudnych miejsc pracy. Z czasem Dorenbos zauważył obszar, który wymagał istotnego udoskonalenia – postanowił stworzyć osprzęt zabezpieczający liny przed uszkodzeniem przez ostre krawędzie, który finalnie został nazwany Vortex.
Początkowo, ze względu na brak umiejętności w obszarze projektowania parametrycznego i metod produkcji, Dorenbos skonsultował się z zewnętrznym projektantem, który pomógł przenieść jego szkice i koncepcje na ekran oprogramowania klasy CAD. Projektant współpracował z firmą GoProto Inc., oferującą usługi szybkiego prototypowania i produkcji gotowych części z tworzyw sztucznych i metalu. Założona w 2018 r. firma była jedną z pierwszych na świecie, które wykorzystywały w pracy drukarki 3D HP Jet Fusion. Dziś posiada łącznie dziewięć drukarek 3D HP – sześć w USA i trzy w Australii. Dorenbos wykonał w GoProto prototypy funkcjonalne swojego produktu, które poddał rygorystycznym testom niszczącym. Gdy materiał i produkt okazały się przekraczać początkowe oczekiwania, przyszedł czas na produkcję części o charakterze końcowym.
Materiał jaki został wykorzystany w produkcji to HP 3D High Reusability (HR) PA 12, charakteryzujący się wysoką wytrzymałością i udarnością. Równocześnie technologia HP MJF okazała się najlepszym rozwiązaniem dla małoseryjnej produkcji osprzętu, który z jednej strony posiadał złożoną i trudną do odwzorowania innymi metodami produkcyjnymi geometrię, a z drugiej wymagał skrajnie wysokiej trwałości.
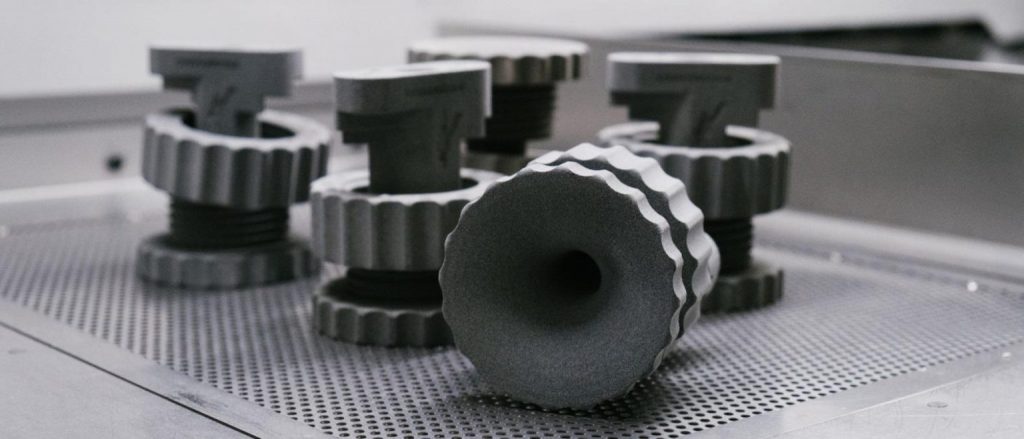
Dzięki pomocy GoProto, które należy do sieci HP Digital Manufacturing Network (DMN), firma Dirka Dorenbosa – Ropes Edge, wykorzystała technologię HP MJF do udoskonalenia swojego projektu i produkcji w sposób szybszy i tańszy, niż umożliwiają to tradycyjne metody produkcji. Wykorzystanie formowania wtryskowego do produkcji części zajęłoby 6-8 tygodni, plus kilka dodatkowych tygodni na regulacje, modyfikacje narzędzi i ponowne próby. Z kolei tańsza metoda produkcji addytywnej – FDM, nie gwarantowała takiej samej jakości wykończenia części i była mniej wydajna.
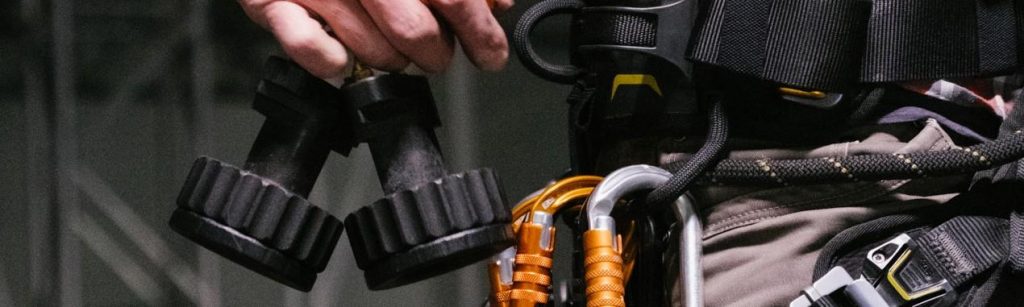
Dzięki technologii MJF Ropes Edge może wyprodukować zarówno kolejne prototypy jak i części końcowe w 3-5 dni od dnia złożenia zamówienia. Dzięki możliwościom szybszej iteracji, firma może szybciej wprowadzać innowacje i wdrażać zmiany. Dodatkowo, klienci mogą zamawiać części lokalnie, poprzez sieć produkcji HP DMN – zamiast produkować je w jednym miejscu i wysyłać kurierem, Ropes Edge może zlecić wydruk 3D części w drukarni 3D z miasta klienta, który odbierze je bezpośrednio.
Firmy zainteresowane przetestowaniem i/lub zakupem technologii druku 3D HP MJF proszone są o kontakt z firmą Integart.
Źródło: www.drukarki3dhp.pl