Firma Deep Blue Aerospace skróciła czas potrzebny na wyprodukowanie komory spalania silnika rakietowego o około 70% dzięki technologii druku 3D z metalu Farsoon Technologies. Firmy współpracują ze sobą od 2022 r., kiedy działające w branży lotniczej Deep Blue zainwestowało w drukarkę 3D Farsoon FS621M, aby wykorzystać ją w produkcji silników rakietowych.
Farsoon i Deep Blue Aerospace wspólnie pracowały nad zapewnieniem wyższej wydajności przy obniżonych kosztach w produkcji części o dużych rozmiarach przekraczających 600 mm. Drukarka 3D FS621M ma wymiary robocze 620 x 620 x 1100 mm, dlatego uznano, że jest potencjalnym czynnikiem umożliwiającym realizację tych celów. Po miesiącach testów i weryfikacji Farsoon poinformował, że osiągnięto „dużą liczbę udanych wdrożeń optymalizacji maszyn i procesów ukierunkowanych na produktywność i wyższą jakość”.
Wśród nich znajduje się druk 3D komory spalania o średnicy 600 mm i wysokości 780 mm. Po szczegółowej analizie i optymalizacji układu optycznego, parametrów procesu, strategii skanowania i ponownym powlekaniu proszkowym maszyny FS621M partnerom udało się wyprodukować komorę spalania w 96,5 godziny, zamiast 327 godzin.
Poczyniwszy te postępy, Farsoon przedstawił szczegółowe informacje na temat ulepszeń wprowadzonych do procesu stapiania proszków metali, które ułatwiły skrócenie czasu produkcji. Jak twierdzi firma, kluczem do osiągnięcia tego sukcesu było opracowanie zaawansowanych strategii skanowania wielolaserowego i szybko działającego algorytmu w nakładających się obszarach, co pomogło stawić czoła wyzwaniom związanym z kontrolą mocy lasera, kalibracją systemu galvo, spójnością nakładania się i obsługą wielu laserów. koordynacja zadań. Zaawansowane strategie skanowania poprawiły kontrolę nad skanerem i galvo dzięki zoptymalizowanym parametrom, poprawiając wydajność komunikacji o 39%, zapewniając jednocześnie wewnętrzną jakość metalurgiczną.
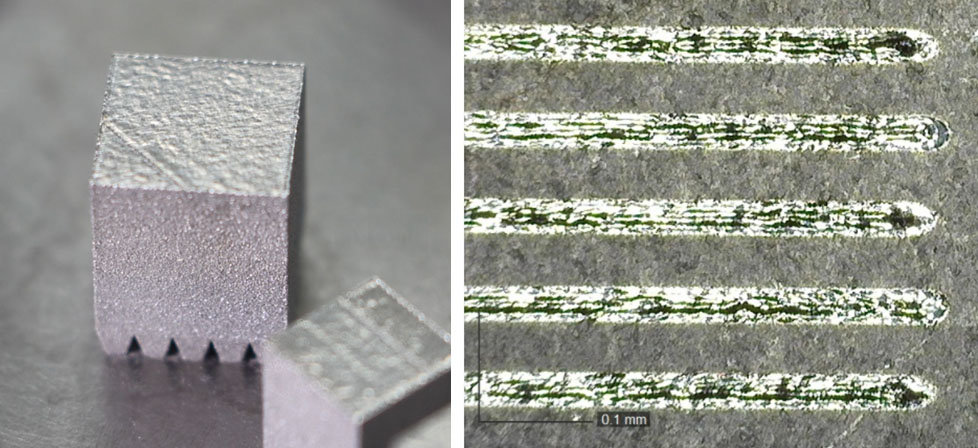
W międzyczasie Farsoon pracował także nad udoskonaleniem projektu przepływu gazu, aby umożliwić terminowe usuwanie dymu i płynniejszą pracę wielu laserów, a także zoptymalizowano system sterowania, aby skrócić czas oczekiwania między laserami i zminimalizować czas przestoju. Następnie firma dokonała „skrupulatnych dostosowań” parametrów przetwarzania, aby pomóc w uzyskaniu powierzchni o wysokiej jakości.
Źródło: www.farsoon-gl.com