W ostatnie dniach chyba nie było medium, które nie napisałoby czegoś o najnowszym samochodzie ze stajni Bugatti, czyli Tourbillon. Nie będziemy się zatem wyróżniać w tej kwestii. Ten limitowany do 250 sztuk, kosztujący €3,8 mln samochód, to nie tylko dzieło sztuki na kołach, ale też ogromne osiągnięcie technologiczne z 1800 końmi pod maską. Jest to pierwsza hybryda w historii marki i choć zasięg na silniku elektrycznym to zaledwie 60km, to pozostałe parametry to już wyżyny osiągnięć motoryzacji. Tourbillon rozpędza się do 100km/h w zaledwie 2 sekundy. Prędkość maksymalna po odblokowaniu tak zwanym Speed Key to 445km/h. Ale zostawmy te informacje dla portali branżowych. Nas interesuje, co takiego sprawiło, że najnowszy samochód od Bugatti osiąga takie parametry? Z pewnością zastosowanie silnika elektrycznego oraz spalinowego V16 ma spory wpływ, ale my wierzymy, że użycie technologii addytywnych w konstrukcji podwozia i zawieszenia dorzuciło swoją cegiełkę w postaci obniżonej wagi, zoptymalizowanej geometrii i zwiększonej wytrzymałości komponentów.
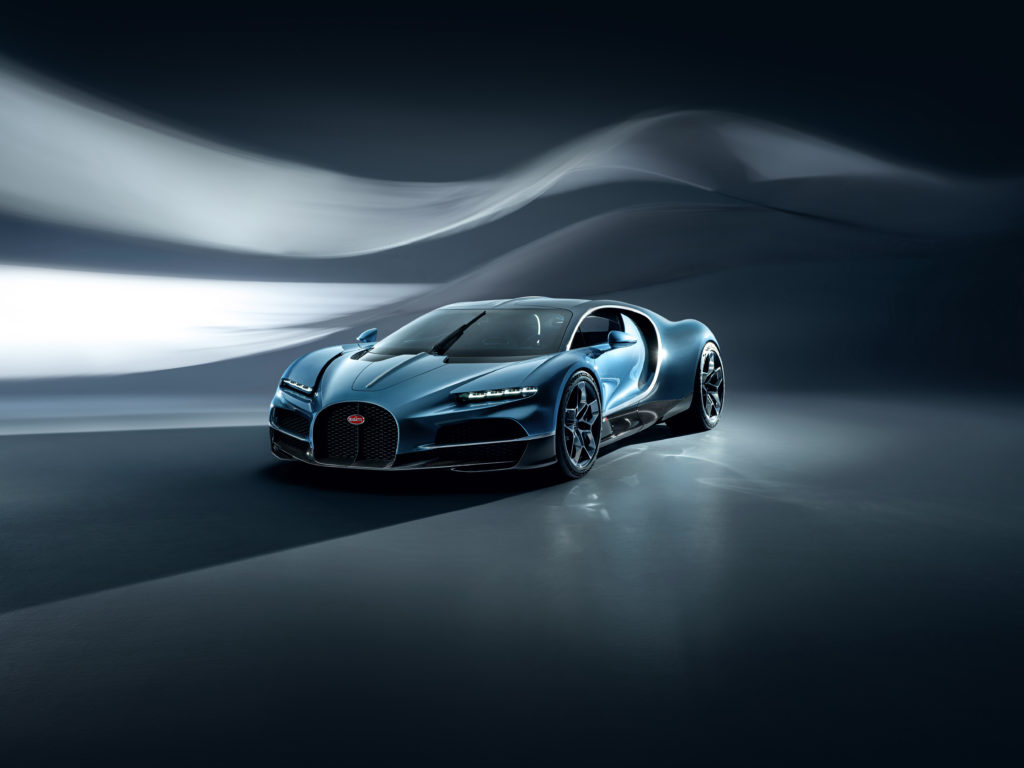
Bugatti nawiązało współpracę z amerykańską firmą Divergent Technologies celem wdrożenia przy produkcji Tourbillona ich systemu DAPS, Divergent Adaptive Production System. Poniżej pozwolimy sobie zacytować ze strony Divergent, czym dokładnie jest DAPS:
„…to kompletne rozwiązanie software’owe i hardware’owe zaprojektowane w celu zastąpienia tradycyjnej produkcji pojazdów. Aby uprościć cały proces, jest to kompletna modułowa cyfrowa fabryka skomplikowanych konstrukcji. Biorąc pod uwagę zestaw wymagań cyfrowych jako dane wejściowe, maszyna automatycznie projektuje, wytwarza przyrostowo i montuje dowolną złożoną konstrukcję. System może płynnie przełączać się między produkcją różnych modeli pojazdów.„
Jesteśmy bardzo ciekawi jak to wygląda od kuchni, ale na nasze można to tłumaczyć jako kompletny ekosystem służący do produkcji addytywnej podparty projektowaniem pod technologie addytywne na potrzeby branży automotive.
Jakkolwiek enigmatycznie to nie brzmi, efekty są bardzo namacalne.
Źródło: 3dprinting.com