Z roku na rok zwiększa się świadomość przedsiębiorstw produkcyjnych na temat metod polepszania wydajności produkcji poprzez wdrażanie innowacyjnych rozwiązań. W dobie Przemysłu 4.0. firmy starając się dotrzymać kroku konkurencji stawiają na nowe, wcześniej niewykorzystywane przez nich technologie — wśród nich druk 3D. Integracja dotychczasowego systemu produkcji z rozwiązaniami z zakresu technologii przyrostowych przekłada się na zwiększenie wydajności, czego naturalną konsekwencją jest redukcja kosztów.
Jedną z firm, której historia stanowi success-story wdrożenia druku 3D do produkcji jest NGNY, hiszpański producent zautomatyzowanych maszyn stanowiących wyposażenie laboratoriów klinicznych. Urządzenia projektowane są do wykonywania powtarzalnych sekwencji ruchów w celu zarządzania próbkami – ich kwalifikacji, przenoszenia pomiędzy kolejnymi stacjami (m.in. wirowania czy etykietowania) czy końcowej identyfikacji. Przepustowość procesów identyfikacji próbek jest wysoka. Dla całodobowych laboratoriów może być to nawet 24,000 zidentyfikowanych próbek.
Produkcja tego typu urządzeń ma charakter niemal jednostkowy. Jak tłumaczy Joan Viladomat, CEO NGNY, w przypadku ich produkcja elementów urządzeń metodą formowania wtryskowego jest nieopłacalna, ponieważ każda maszyna służy innym celom i dostosowana jest do indywidualnych potrzeb użytkownika. Rozwiązaniem okazały się technologie przyrostowe, które znacząco poprawiły wydajność procesu tworzenia i testowania nowych, spersonalizowanych elementów urządzeń.
https://www.youtube.com/watch?time_continue=96&v=7VihTR6AHSc&feature=emb_title
Optymalizując proces projektowania firma korzysta z własnych drukarek 3D firmy BCN3D. Urządzenia przyspieszają rozwój elementu, pozwalając jednocześnie zaoszczędzić dziesiątki tysięcy euro, eliminując konieczność wysyłania każdej iteracji projektu do zewnętrznego dostawcy. Koszt stworzenia pojedynczego elementu, korzystając z usług firmy zewnętrznej oscylował na poziomie 30 EUR.
Producent, uwzględniając ilość wytwarzanych elementów oraz średnia ilość iteracji każdej części, oszacował, że wdrożenie technologii przyrostowych każdego roku generuje oszczędności rzędu 40 000 EUR (diagram poniżej).
Jak tłumaczy Tomeu Ventayola, Project Manager w NGNY, technologia druku 3D stanowi dla nich rewolucję w sposobie tworzenia i produkcji elementów. Udało im się z powodzeniem wdrożyć i dopasować technologię wytwarzania przyrostowego do swoich potrzeb, a także sprawić, aby produkcja niskoseryjna elementów stała się dla nich opłacalna. Idąc za ciosem, specjaliści z NGNY zdecydowali się również na produkcję addytywną części końcowych, wykorzystując urządzenia BCN3D Sigma.
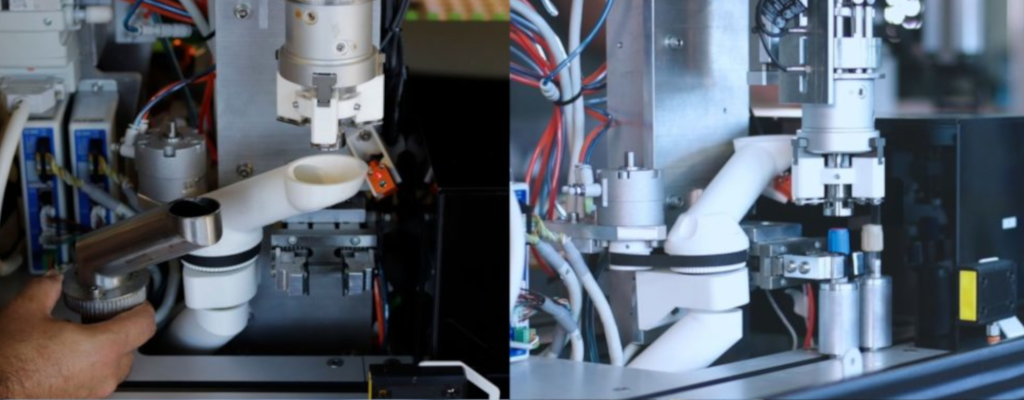
Producent w zależności od zastosowania elementu korzystają z dwóch rodzajów materiałów – PLA (dla prototypów) oraz Nylonu (dla części funkcjonalnych). Każdy z elementów przechodzi fazę testowania podczas której tworzone są kolejne iteracje części do czasu, aż opracowany zostanie element spełniający wszelkie założenia projektowe.
Następnie, inżynierowie NGNY, przekonani, że element charakteryzują wszystkie wymagane parametry, wytwarza finalne części na drukarkach 3D. Jak dodaje Tomeu Ventayola, technologia od BCN3D zapewnia powtarzalną, wysoką jakość wykonania części.

Oficjalnym dystrybutorem drukarek 3D BCN3D Technologies w Polsce jest firma Global 3D.
Źródło: bcn3d.com