Technologia HP Multi Jet Fusion to relatywnie nowa metoda przyrostowa, stosowana w drukarkach 3D HP Jet Fusion 3D, wyróżniająca się na tle innych metod produkcyjnych w obszarze kosztów, prędkości i jakości. Technologia MJF umożliwia wytwarzanie skomplikowanych geometrii, niemożliwych do osiągnięcia innymi technikami, równocześnie produkując części o niższej wadze – w dużej mierze dzięki strukturze kratownicowej lub optymalizacji topologii geometrii. Same tworzywa sztuczne wykorzystywane w procesie druku 3D są lżejsze niż popularne stopy metali jak aluminium lub stal.
Dzięki HP Multi Jet Fusion można zmniejszyć wagę części przy jednoczesnym zachowaniu wymaganej wytrzymałości. Ponadto HP MJF pozwala produkować elementy posiadające niemalże takie same właściwości mechaniczne dla osi XY w porównaniu z osią Z, dlatego na etapie projektowania nie trzeba uwzględniać zachowania mechanicznego. Drukowanie 3D może skrócić czasy realizacji zleceń, ponieważ skomplikowane, wieloelementowe montaże można scalać do pojedynczych części. Zmniejsza to też ryzyko błędów i innych problemów w procesie montażu oraz koszty robocizny.
Druk 3D a CNC
CNC to substratywna technologia produkcji, doskonale nadająca się do wytwarzania małych serii z różnorodnych materiałów, w tym metali i tworzyw sztucznych. Jedną z jej największych zalet jest dokładność – elementy można wytwarzać z tolerancją do +/-0.025 mm, co nie jest możliwe np. w przypadku formowania wtryskowego. W technologii CNC uzyskanie pewnych geometrii, np. narożników wewnętrznych o małym promieniu, skomplikowanych wgłębień i podcięć oraz cienkich ścianek jest jednak niezwykle trudne, a często niemożliwe, z uwagi na ograniczenia samego procesu wytwórczego…
Równocześnie maszyny typu CNC wymagają zaangażowania wykwalifikowanych operatorów, gdyż ich konfiguracja i konserwacja może być skomplikowana, a sam plik produkcyjny z zapisanymi instrukcjami do wycinania (frezowania) elementów należy utworzyć wcześniej w odpowiednim programie CAM. Przed rozpoczęciem produkcji części z zastosowaniem obróbki CNC należy przeprowadzić czynności konfiguracyjne – najpierw przygotowywany jest plik z instrukcjami prowadzącymi narzędzie frezujące, a w samej frezarce lub obrabiarce trzeba zainstalować odpowiednie narzędzie skrawające oraz uchwyty podtrzymujące. Z tego względu elementy zazwyczaj wytwarza się po kolei – jeden po drugim.
Jeśli uwzględnić szacunki kosztowe, obróbka CNC jest odpowiednim procesem do produkcji części o prostej konstrukcji. Elementy o złożonej geometrii często wymagają dłuższego czasu produkcji CNC, co może zwiększyć ostateczny koszt części. W przypadku HP Multi Jet Fusion skomplikowana geometria nie wydłuża czasu ani nie zwiększa kosztu produkcji, gdyż technologia ta umożliwia wyższą wydajność produkcji niezależnie od złożoności elementów.
Równocześnie technologia HP Multi Jet Fusion umożliwia wytwarzanie części, które zostały przeprojektowane (puste w środku lub zoptymalizowane topograficznie) w celu redukcji ilości materiału wymaganego do ich wytworzenia, co dodatkowo zmniejsza ich koszt. W porównaniu z innymi technikami druku 3D, HP Multi Jet Fusion pozwala na produkcję części o wysokiej jakości przy niższym koszcie. Jest to możliwe dzięki materiałom HP 3D High Reusability, umożliwiającym ponowne wykorzystanie do 80% starego proszku.
Dodatkowo łatwość użytkowania i czyszczenia oraz przewidywalność technologii HP MJF skraca czas pracy operatora redukując jednocześnie poziom wymaganych umiejętności. Konieczność zaangażowania wykwalifikowanych pracowników do konfiguracji i konserwacji skomplikowanych i kosztownych urządzeń CNC również może wpłynąć na koszty ogólne. Można je zredukować dzięki HP Multi Jet Fusion, gdyż po wykonaniu projektu części 3D, plik jest przesyłany do drukarki drogą elektroniczną, a element można wytworzyć przy niewielkim udziale człowieka.
Czas ma krytyczne znaczenie, jeśli potrzebny jest przyrząd produkcyjny lub prototyp. Zazwyczaj do stworzenia idealnego projektu dla danego zastosowania niezbędnych jest większa liczba iteracji. Skrawanie skomplikowanych geometrii w przypadku metalu wymaga szerokiego zakresu projektowania oraz wysoce wykwalifikowanych projektantów CAD i operatorów maszyn. HP Multi Jet Fusion nie wymaga CAM, umożliwia skrócenie czasu realizacji, gdyż kilka iteracji projektu można wykonać jednocześnie, to pozwala na produkcję kilku części o różnej konstrukcji w ramach jednej partii produkcyjnej.
HP Multi Jet Fusion umożliwia produkcję części do 10 razy szybciej niż inne technologie druku 3D. Dzięki tym poziomom produktywności i szybkości, można znacznie skrócić czasy realizacji: z kilku dni do zaledwie jednego.
Druk 3D umożliwia wytwarzanie na żądanie, co z kolei może zredukować, a nawet wyeliminować konieczność posiadania zapasów wyprodukowanych części. Pozwala też zredukować zapasy materiałów. Aby pracować wydajnie, warsztaty CNC muszą dysponować blokami materiałów w różnych rozmiarach, natomiast proszek do drukowania 3D jest pobierany bezpośrednio z kartridżów, niezależnie od geometrii lub rozmiaru wytwarzanych części.
Obróbka CNC, jako technika substratywna, usuwa materiał z pierwotnego bloku surowca, działa więc na zasadzie wytwarzania odpadów, których recykling – szczególnie w przypadku tworzyw sztucznych – jest trudny, kosztowny i czasochłonny. HP Multi Jet Fusion minimalizuje ilość materiału (proszku) odpadowego w procesie drukowania w przypadku stosowania standardowych gęstości, a wskaźnik ponownego wykorzystania proszku wynosi do 80%.
Jakie części można wytwarzać za pomocą technologii HP Multi Jet Fusion?
HP Multi Jet Fusion to technologia produkcji 3D, która może stanowić uzupełnienie obróbki CNC. Poniższa tabela określa, do jakich zastosowań i wymagań najlepiej nadają się obie technologie:
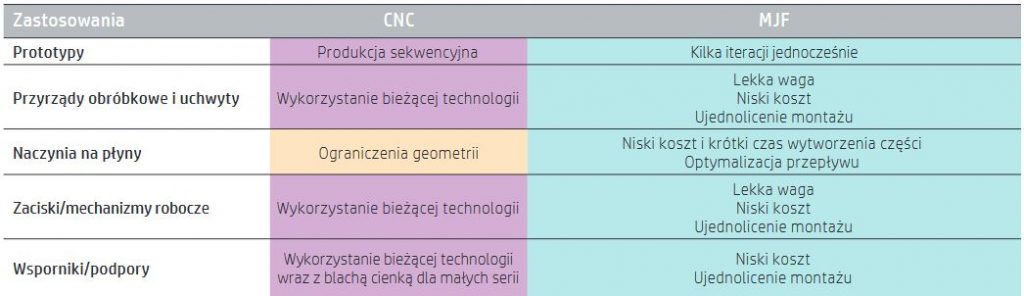
Tradycyjnie techniki drukowania 3D stosuje się do walidacji projektów i ich ponownej iteracji na wczesnym etapie opracowania produktu. Wolumen części na tym etapie zazwyczaj jest niski w porównaniu z obecnymi wymaganiami dla części końcowych lub zamiennych.
Dzięki HP Multi Jet Fusion można szybko wytwarzać funkcjonalne części przy niskim koszcie, które można wykorzystać nie tylko jako prototypy, ale też jako części końcowe, na różnych etapach cyklu życia produktu (PLC). Wprowadzenie części HP Jet Fusion w produkcji może zredukować koszty w porównaniu z tradycyjnymi technologiami, w zależności o części i wolumenu produkcji, oraz dodać wartość do samego procesu projektowania. Jednym z przykładów wartości dodanej jest umożliwienie uzyskania nowych geometrii, które wcześniej nie były możliwe.
Otwiera to też ciekawe możliwości dla części zamiennych, gdyż wykorzystanie części drukowanych trójwymiarowo może zoptymalizować łańcuchy dostaw i logistykę na końcowych etapach PLC.
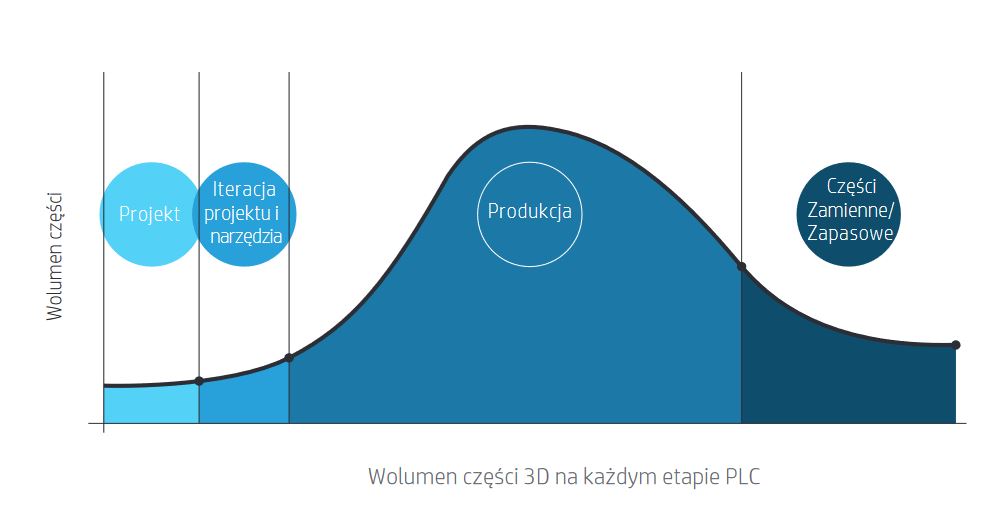
Główne zastosowania, w przypadku których HP Multi Jet Fusion może zwiększyć wartość w porównaniu z obróbką CNC to m.in.:
1. Prototypy (czytaj więcej…)
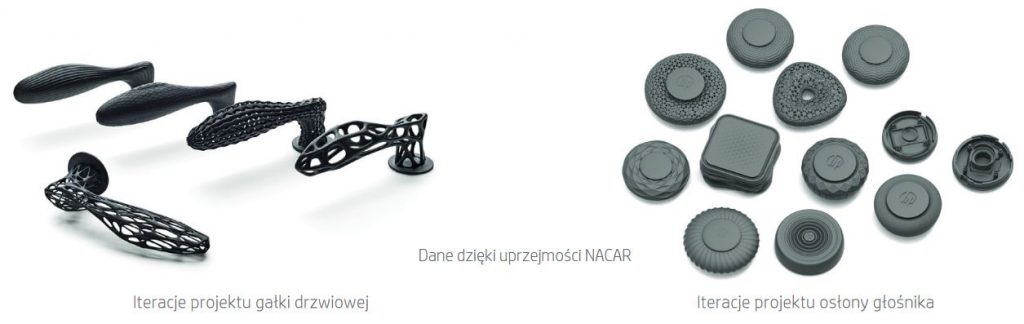
Prototyp to wstępny projekt części lub produktu, wykorzystywany w cyklu rozwojowym w ramach iteracji i walidacji koncepcji do chwili osiągnięcia etapu ostatecznego projektu. Prototypowanie funkcjonalnie umożliwia przetestowanie koncepcji na wczesnym etapie projektowania wyrobu, przed przejściem do produkcji.
Zalety HP Multi Jet Fusion w przypadku prototypów:
- Niski koszt
- Jednocześnie można wydrukować kilka części o różnych iteracjach
- Krótki czas wytworzenia części
2. Części wewnętrzne
W przypadku niektórych małoseryjnych produktów lub maszyn, produkcja formy nie ma uzasadnienia ekonomicznego – dlatego niektóre części są wytwarzane z użyciem obróbki lub blachy, zamiast formowania wtryskowego. W takich sytuacjach istnieją różne rodzaje części plastikowych – takich jak wsporniki lub podpory (np. wsporniki czujników) mogących utrzymać małe obciążenia, które można wytworzyć za pomocą HP Multi Jet Fusion zamiast innych tradycyjnych technik produkcji
Zalety HP Multi Jet Fusion dla części wewnętrznych:
- Niski koszt
- Komponenty można zoptymalizować i przeprojektować w celu ujednolicenia
- Krótki czas wytworzenia części
3. Chwytaki/mechanizmy obsługowe
Mechanizm obsługowy lub chwytak to urządzenie znajdujące się na końcu ramienia robota, zaprojektowane do interakcji z otoczeniem. W zależności od rocznego wolumenu, geometrii i wymagań mechanicznych, chwytaki mogą być wykonane z metalu (obróbka CNC lub blacha) lub tworzywa sztucznego (obróbka lub formowanie wtryskowe).
Zalety HP Multi Jet Fusion w przypadku chwytaków/mechanizmów obsługowych:
- Można wytwarzać części o niższej wadze, co zwiększa precyzję i szybkość ruchów z uwagi na mniejszą
bezwładność i środek ciężkości zlokalizowany bliżej ramienia, szczególnie gdy ramię robota ma być ruchome. - Niski koszt
- Zespoły można zoptymalizować i przeprojektować w celu ujednolicenia
Kilka przykładów chwytaków, jakie można wytworzyć za pomocą HP MJF:
Chwytak dla branży samochodowej:
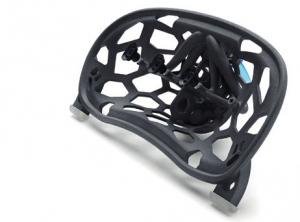
chwytak posiada 4 przyssawki pneumatyczne; większa rama została przeprojektowana w taki sposób, aby zwiększyć ogólną stabilność chwytaka. 4 przyssawki są połączone bezpośrednio z niezależnym zbiornikiem płynu, zaprojektowanym i wydrukowanym w technice 3D, następnie wbudowanym w całą część, co zwiększa wszechstronność kształtu oraz optymalizację całej konstrukcji i części.
Chwytak pneumatyczny
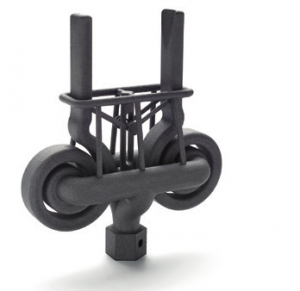
Chwytak pneumatyczny został prototypowany i opracowany specjalnie pod kątem wymagań klienta. Jednym z tych wymagań było zapewnienie, że żywotność chwytaka podczas testów przekroczy milion cykli. Jego konstrukcja została ulepszona poprzez wzmocnienie niektórych typowych obszarów usterek oraz dodanie małych i precyzyjnych mechanizmów zapewniających osiągnięcie lepszej symetrii ruchów i stabilności chwytu.
Spiralny kształt układu pneumatycznego został zaprojektowany z wykorzystaniem nie tylko typowych wypustów, ale też matematycznych funkcji przyrostowych, tak aby stworzyć idealną spiralę. Po napełnieniu spirali sprężonym powietrzem, chwytak zaciska się. Po uwolnieniu powietrza chwytak ponownie się otwiera, co umożliwia stosunkowo szybkie otwieranie i zamykanie chwytaka poprzez regulację częstotliwości wlotu i wylotu powietrza. Projekt druku 3D umożliwił wyprodukowanie tego chwytaka w formie pojedynczego elementu. W przypadku tradycyjnych metod produkcji konieczne byłoby wytworzenie kilku części oraz ich montaż.
4. Przewody płynów
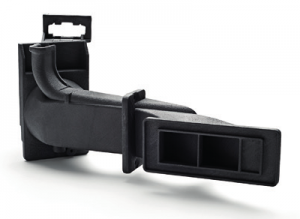
Przewody płynów to części – rurki lub kanały – służące do transportowania płynu wewnątrz układu. Zazwyczaj wytwarza się je metodą ekstruzji, ale mniejsze powstają metodą obróbki CNC. Materiał stosowany do wyrobu przewodów musi być chemicznie kompatybilny z danym płynem. Porowatość materiału może wpłynąć na szczelność.
Zalety HP Multi Jet Fusion dotyczące przewodów transportujących płyny:
- Szczelność można osiągnąć bez obróbki końcowej
- Ujednolicenie różnych przewodów lub części polepsza właściwości użytkowe (redukując wycieki)
- Poprawa wydajności przepływu
- Materiał HP 3D High Reusability PA 12 cechuje się dużą kompatybilnością chemiczną z różnymi płynami, w tym z wodą, płynem hamulcowym i alkoholami
5. Przyrządy produkcyjne
Przyrządy produkcyjne to wszelkiego rodzaju narzędzia stosowane w procesie produkcji do kontroli jakości lub pomagające w produkcji. Zapewniają powtarzalność, dokładność, produktywność i wymienność w ramach procesu.
Druk 3D i obróbka CNC są już stosowane do wytwarzania przyrządów produkcyjnych na liniach produkcyjnych, ale dostępne do tej pory rozwiązania były bardzo kosztowne.
Multi Jet Fusion oferuje przełomową produktywność w porównaniu z innymi technikami drukowania 3D i może znacząco skrócić czas wytwarzania przyrządów produkcyjnych. Zwiększa to elastyczność w procesie produkcji, umożliwiając szybszą reakcję na potrzebę zmian (np. zmiana projektu części).
Zalety HP Multi Jet Fusion dla przyrządów produkcyjnych:
- Niski koszt
- Redukcja wagi poprzez struktury kratownicowe lub optymalizację topologii
- Swoboda projektowania i większa elastyczność
- Możliwość unifikacji osobnych zespołów.
Przypadki zastosowania HP Multi Jet Fusion
SIGMADESIGN łącznik aplikatora próżniowego
SIGMADESIGN to firma świadcząca usługi rozwoju produktów, oferująca rozwiązania pomagające klientom w poprowadzeniu procesu wytwarzania produktów od koncepcji do produkcji i jeszcze dalej. Usługi SIGMADESIGN obejmują m.in. projektowanie przemysłowe, zapewnianie jakości i badania oraz wsparcie technologiczne, jak również wyrób produktów końcowych.
Jeden z klientów SIGMADESIGN wytwarza maszyny do etykietowania owoców. Są to małoseryjne urządzenia o wysokiej jakości, które nakładają kilka tysięcy etykiet na godzinę, a przy tym wymagają precyzji, aby nie uszkadzać owoców.
SIGMADESIGN miała za zadanie uzyskanie redukcji kosztów oraz poprawę konstrukcji pewnych elementów tej maszyny. Firma zidentyfikowała kilka części, które można było udoskonalić za pomocą technologii HP Multi Jet Fusion, w tym:
Łącznik aplikatora próżniowego to element chwytaka ramienia, który umieszcza etykiety na jabłkach:
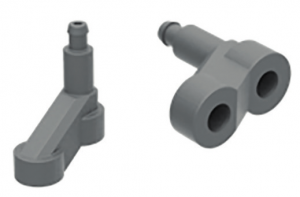
Pierwotnie zespół ten był wytwarzany z aluminium. Pracuje przy podciśnieniu od -2 do -3 psi. Jego szacowana trwałość użytkowa jest taka sama, jak dla całej maszyny, co oznacza dziesiątki milionów cykli eksploatacji.
Komponent musi być wystarczająco precyzyjny, aby umożliwić nitowanie gwintowanych wkładek w otworach górnych. Ważne było wytworzenie tych otworów z konkretną tolerancją, aby zachować maksymalną wytrzymałość pomiędzy gwintowanym uchwytem a częścią po procesie nitowania.
SIGMADESIGN rozwiązała to wyzwanie projektując część do druku 3D za pomocą HP Multi Jet Fusion:
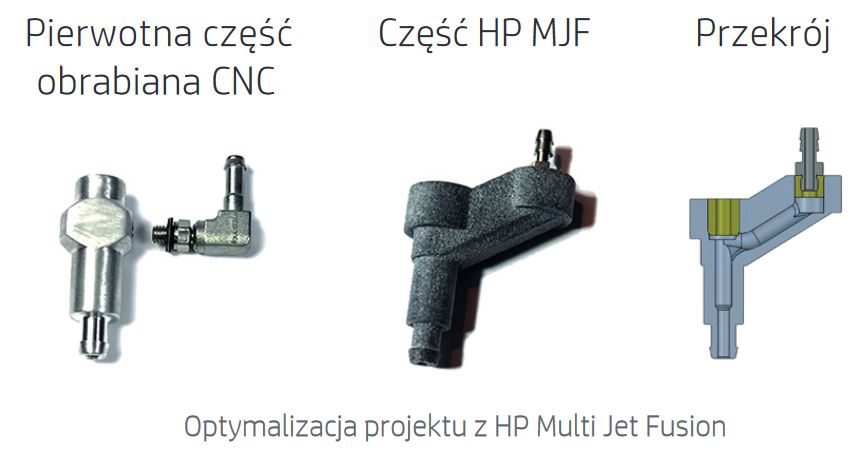
HP Multi Jet Fusion umożliwia SIGMADESIGN:
- Drukowanie ciągłych kanałów przepływu powietrza, która to możliwość nie była dostępna w przypadku obróbki CNC, co redukuje wycieki powietrza i poprawia wydajność części
- Optymalizację geometrii części, wcześniej ograniczoną przez produkcję CNC, do pracy w określonej przestrzeni,co zapobiega kolizjom z innymi ruchomymi elementami
- Redukcję kosztu części o 68% w porównaniu z pierwotną konstrukcją
HP Inc. Suwak ekstrakcyjny wiertła
HP Inc. to firma wytwarzająca elektronikę konsumencką, w tym drukarki 2D i 3D, komputery PC i urządzenia peryferyjne.
HP jest pionierem w stosowaniu technologii HP Multi Jet Fusion do usprawniania procesów w swoim łańcuchu dostaw i zidentyfikowała do tej pory wiele możliwości zastąpienia tradycyjnych metod produkcji technologią HP Multi Jet Fusion.
Jednym z przykładów jest narzędzie na linii produkcji głowic drukujących HP – suwak ekstrakcyjny wiertła.
Dysze głowic drukujących HP wytwarzane są w procesie cięcia laserowego. W procesie tym wykorzystuje się wodę do chłodzenia lasera i silikonowe płytki. Podczas cięcia suwak ekstrakcyjny wiertła stosowany jest do usuwania stale obecnego odpadu silikonowego i wody, co zwiększa wydajność procesu cięcia laserowego.
Prawidłowy proces produkcyjny wymaga odpowiedniego ciśnienia ekstrakcji (~3 do 4.5 kPa) oraz czystego suwaka ekstrakcyjnego. Narzędzie musi wytrzymać pewną ilość ciepła wytwarzaną przez impulsy lasera podczas procesu wiercenia.
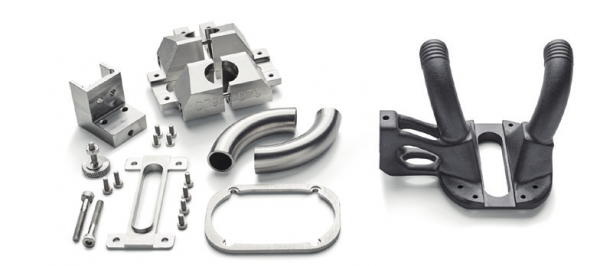
Jak widać na ilustracji po prawej stronie, początkowe narzędzie obrabiane CNC. Narzędzie widoczne po lewej stronie wykonane jest z 7 elementów, z których większość obrobiono z zastosowaniem bloku aluminium, a dwie wytłoczono z aluminium. Przeprojektowana część HP MJF znajduje się po prawej stronie i stanowi jeden komponent niewymagający składania.
Technologia HP Multi Jet Fusion zapewnia w tym przypadku:
- Wodoszczelność niezbędną dla przyrządów produkcyjnych zawierających płyny pod ciśnieniem, bez konieczności obróbki końcowej lub powlekania części
- Optymalizację konstrukcji w celu zredukowania turbulencji wewnątrz elementu za pomocą analizy elementów
skończonych Modyfikację kształtu rurki w celu optymalizacji przepływu przez element - Redukcję kosztu o 95% w porównaniu z pierwotną częścią.
- Zmniejszenie wagi o 90% w porównaniu z pierwotną częścią, dzięki optymalizacji topologii i mniejszej ilości materiału
- Skrócenie czasu wykonania z 3-5 dni przy obróbce CNC do zaledwie 24 godzin w przypadku MJF
- Redukcję montażu poprzez połączenie siedmiu części składowych w jeden element