Istniejąca od 30 lat, amerykańska firma Biotech Dental jest wiodącą firmą w branży stomatologicznej, specjalizującą się w produkcji wysokiej jakości implantów stomatologicznych. Równocześnie od pewnego czasu, firma inwestuje 10% obrotów w technologię druku 3D, zdobywając pozycję jednego z liderów w tym segmencie, na amerykańskim rynku. Jest równocześnie jedyną firmą na świecie, która produkuje 100% swoich protez dentystycznych przy użyciu cyfrowych przepływów pracy i druku 3D w połączeniu z innymi sposobami wytwarzania procesów takich jak frezowanie. Duży udział ma w tym technologia MultiJet Fusion firmy HP.
„Druk 3D jest filozofią Biotechu. Z wyjątkiem implantów stomatologicznych i śrub, wszystkie spersonalizowane produkty, zabiegi ortodontyczne i protezy są w całości lub częściowo budowane dzięki drukarkom HP 3D Multi Jet Fusion” – mówi Robin Maisonneuve, Dyrektor Zarządzający Biotech Dental. Misją firmy jest tworzenie cyfrowej przyszłości stomatologii przy jednoczesnym dostarczaniu łatwych w użyciu rozwiązań oraz wysokiej klasy produktów w atrakcyjnych cenach dla swoich klientów. Firma polega na innowacjach technologicznych i digitalizacji, aby odróżnić się od swoich konkurentów.
Projektowanie ruchomej protezy wiąże się z problemami dotyczącymi materiałów (np. żywice, metale, kompozyty), które nie mogą być drukowane w tej samej maszynie i które mogą wpłynąć na pogorszenie jakości końcowej. Dlatego Biotech Dental opracowała i opatentowała nowy proces usprawniający digitalizację protez dentystycznych. „Kiedy laboratorium projektuje ruchomą protezę, problem wynika z faktu, że ta proteza zawiera różne materiały, które nie mogą być drukowane”. – mówi Maisonneuve. „Niektóre nie mogą być w ogóle drukowane, jeśli chcemy uzyskać dobrą jakość. Biotech Dental korzysta z technologii druku 3D od ponad 10 lat, ale zaczęliśmy używać HP Multi Jet Fusion, ponieważ maszyna była znacznie bardziej wydajna w porównaniu z tradycyjnymi metodami produkcji”.
Firma chciała automatycznie zaprojektować i wydrukować dwuczęściową formę do umieszczenia w niej metalowego szkieletu i protezy. W obliczu ciągłej ewolucji maszyn produkcyjnych i tradycyjnych technologii, Biotech Dental był zmuszony do częstych zmian, aby być bardziej produktywnym. Wcześniej firma stosowała frezowanie, toczenie oraz metody przyrostowe – SLS, DLP, czy Binder Jetting. Przed wprowadzeniem technologii HP Multi Jet Fusion, wytwarzanie i projektowanie częściowych protez ruchomych, takich jak zęby i dziąsła, stanowiło spore wyzwanie.
Przed wprowadzeniem technologii HP MJF, wytwarzanie i projektowanie częściowych protez ruchomych, takich jak zęby i dziąsła, stanowiło wyzwanie. Laboratoria potrzebowały trzech godzin, a dentyści czterech wizyt, aby wyobrazić sobie rodzaje potrzebnych części, w tym standardowe kształty zębów kompozytowy wydrukowany zestaw zębów.
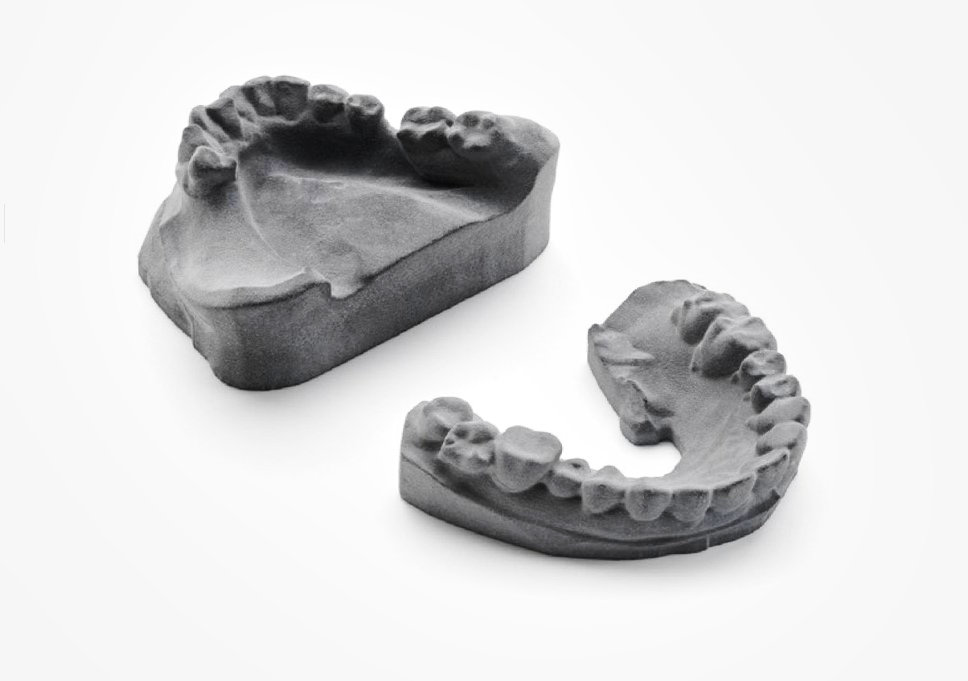
Firma chciała automatycznie zaprojektować i wydrukować dwuczęściową formę do umieszczenia metalowej ramy kompozytowy zestaw zębów z nadrukiem. Dwuczęściowa forma jest zamykana, a żywica jest wstrzykiwana i wypalana. Po zakończeniu, część wyciągnięta z formy jest polerowana i proteza jest gotowa. W przypadku laboratoriów proces ten wymaga pięciu do 10 minut projektowania i dwóch wizyt u stomatologa.
Drukarka 3D HP Multi Jet Fusion zwiększyła tempo produkcji o prawie czterokrotność pierwotnego tempa i zredukowała koszty o 78%, w porównaniu z procesem SLS, z którego korzystali wcześniej. Poprzednia technologia produkowała 42 formy dziennie przy koszcie sprzedanych towarów (COGS) na poziomie 18€. Teraz HP MJF pozwala na produkcję 180 form dziennie przy COGS na poziomie 4€. W 2019 roku Biotech Dental planuje przyspieszyć produkcję drukując 250 form dziennie. Firma ma nadzieję stać się jedynym partnerem produkcyjnym form dentystycznych na rynku (60 milionów form rocznie).
Przedsiębiorstwa zainteresowane przetestowaniem lub zakupem technologii druku 3D HP Multi Jet Fusion zachęcamy do kontaktu z firmą Integart Sp. z o.o.
Źródło: materiały prasowe Integart