Elementy metalowe produkowane w procesach addytywnych stają się pełnoprawnym zamiennikiem części wytwarzanych przy pomocy klasycznych, dużo kosztowniejszych technologii. W przypadku produkcji tego typu kluczowym kryterium jest jakość wykonania nieodbiegająca od wyznaczonych standardów – producenci nie mogą pozwolić sobie na żadne odstępstwo od normy. Metoda druku 3D z metali proponowana przez Desktop Metal przedstawiana jest charakterze przełomu w przemyśle, jednak czy stosunkowo niska cena urządzeń może przekładać się na optymalną jakość wytwarzanych detali? Jak się okazuje, firma prowadzi prace nad zapewnieniem jak najpełniejszej kontroli wykonywanych wydruków już na poziomie urządzenia a ich rezultatem jest patent dotyczący systemu nadzorowania jakości wydruków.
Wiadomości dotyczące włączenia wysokobudżetowego druku przestrzennego w proces produkcyjny przez najważniejszych producentów z różnych dziedzin przemysłu nie stanowią już zaskoczenia, są naturalną koleją rzeczy. Dla producentów z branży automotive czy lotniczym obietnica dość radykalnego cięcia kosztów produkcji sprawia, że urządzenia Desktop Metal mogą być rozwiązaniem wartym uwagi. Wyśrubowane standardy dotyczące m.in. parametrów warstwy wierzchniej nadawane podczas procesu produkcji warunkują jego późniejsze właściwości wytrzymałościowe i zachowanie w określonym środowisku.
Inżynierowie z Desktop Metal prowadzą badania nad zoptymalizowaniem systemu kontroli procesu tworzenia metalowego detalu opartego o zjawiska elektrohydrodynamiczne (czyli zachowaniu się elektrycznie naładowanych cząstek płynnego metalu). Charakteryzowanie powierzchni w czasie rzeczywistym za pomocą sygnału generowanego przez sieć sensorów, a następnie porównanie jej z wirtualnym modelem ma pozwolić na zachowanie jak najwyższej jakości wykonywanych wydruków. W razie wystąpienia nieprawidłowości powierzchni wydruku następuje natychmiastowe dostosowanie procesu i przesłanie powiadomienia do użytkownika o ewentualnych zmianach (np. w czasie trwania).
Wśród czujników jakie mogą zostać zastosowane w systemie sensorycznym warto wyróżnić te monitorujące wymiary kropli metalu oraz parametry sił działających na nią, prędkość poruszania się cząsteczek, topografię powierzchni wydruku w polu czy warunki panujące w komorze roboczej.
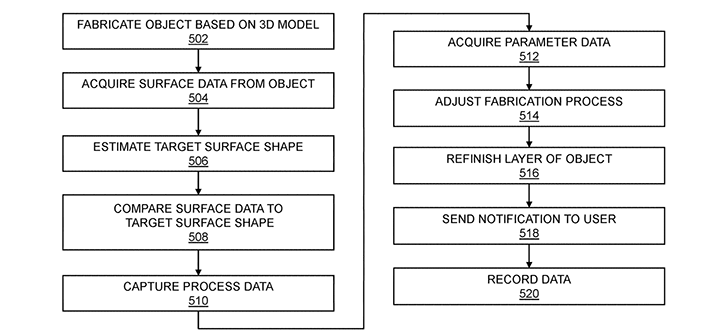
Bezzwłoczna reakcja w razie dostrzeżenia nieprawidłowości w geometrii wydruku już na poziomie wytwarzania wiąże się z zwiększeniem wydajności produkcji, minimalizując ilość drukowanych metali niespełniających konkretnych wymogów już w kolejnych etapach cyklu. Wszelkie rozbieżności pomiędzy projektem wirtualnym a fizycznym modelem są traktowane jako odchylenie od prawidłowej formy detalu.
Jeżeli Desktop Metal uda się wdrożyć tę funkcjonalność w swoich urządzeniach, gwarantując tym samym niezawodność i najwyższą jakość druku to może stać się poważnym konkurentem firm, które od lat zajmują się zagadnieniem technologi przyrostowych w kontekście tworzyw metalowych.
Źródło: fabbaloo.com, patents.google.com