Jedną z największych zalet technologii przyrostowych jest fakt, że w trakcie procesu produkcyjnego zużywa się relatywnie niewiele materiału na wykonanie danego detalu. W wybranych przypadkach (geometria detalu oraz użyta metoda druku 3D) ilość zużytego materiału = objętość części; nic nie jest tracone podczas jego wytwarzania.
Wiele osób rozważających zakup pierwszej drukarki 3D drukującej z tworzyw sztucznych w technologii FDM / FFF porusza często ten temat, odnosząc się np. do frezowania CNC, gdzie zużycie materiału bywa bardzo wysokie. Poniżej prezentuję kilka wariantów produkcji tego samego elementu wskazując na różnice zużycia materiału budulcowego (filamentu).
Parametry wydruku 3D, które mają bezpośredni wpływ na zużycie filamentu to:
- gęstość wypełnienia (od 0% do 100%)
- ilość struktur podporowych (często nie da się poprawnie wydrukować detalu bez supportów)
- ilość struktur poprawiających przyczepność wydruku 3D do stołu roboczego jak raft, czy brim (nie licząc wybranych modeli drukarek 3D można z tego zrezygnować)
- kształt wypełnienia (parametr o niewielkim wpływie na zużycie materiału – ma znaczenie tylko przy bardzo dużych detalach)
- wysokość drukowanej warstwy (jest to parametr o najmniejszym wpływie na zużycie materiału, jednakże występuje).
Naszym modelem testowym będzie ta część (element konstrukcyjny lokomotywy) o wymiarach 81 x 91,5 x 150 mm:
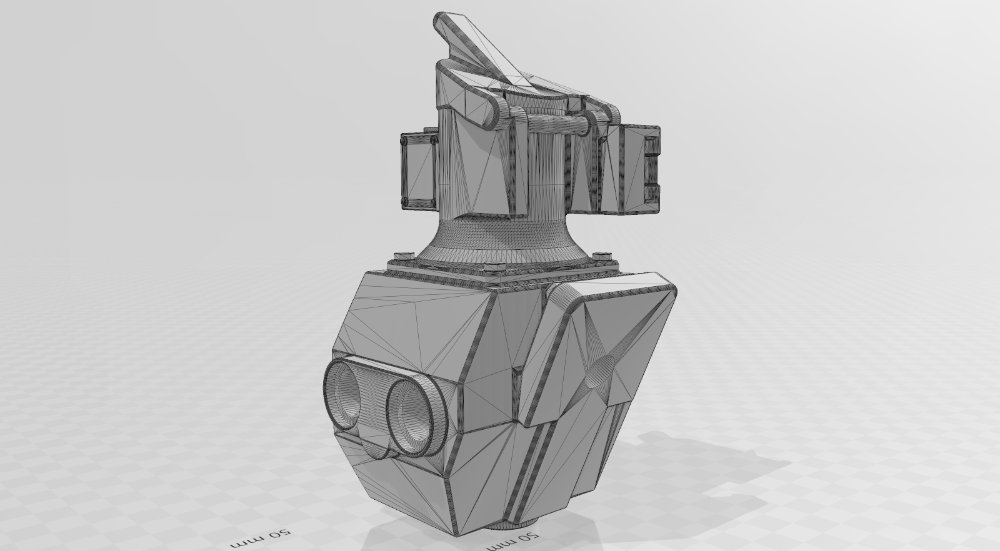
WARIANT 1 – druk 3D w pionie
Najpierw przeprowadzimy symulację dla domyślnego ustawienia detalu jak na printscreenie powyżej. Symulacje będą wykonywane na programie Z-SUITE firmy Zortrax. Drukarki 3D tego producenta muszą mieć wygenerowany raft z uwagi na perferowany stół roboczy, niemniej jednak przy gabarytach detalu, zużycie materiału na ten cel będzie znikome. Równocześnie dla ujednolicenia wyników przyjąłem następujące parametry druku 3D:
- materiał: Smart ABS firmy Spectrum Filaments w cenie 79,99 PLN brutto za 1 kg
- wysokość warstwy: 0,2 mm
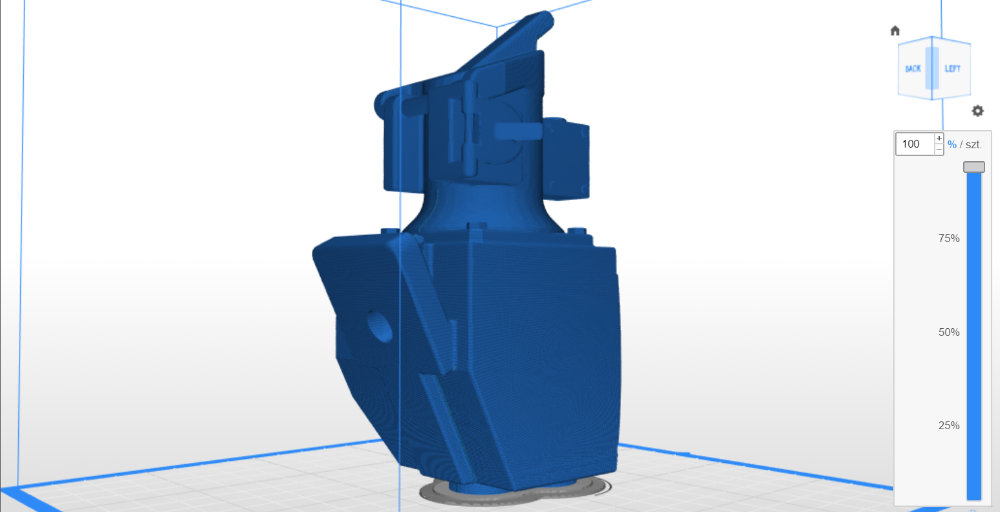
Wariant 1.1 – brak podpór (w rzeczywistości jest to wydruk niemożliwy, tzn. wyjdzie zdeformowany / uszkodzony)
- wypełnienie 0% = 75 gr = koszt materiału 6,00 PLN brutto
- wypełnienie 10% = 105 gr = koszt materiału 8,40 PLN brutto
- wypełnienie 20% = 128 gr = koszt materiału 10,24 PLN brutto
- wypełnienie 50% = 194 gr = koszt materiału 15,52 PLN brutto
- wypełnienie 90% = 290 gr = koszt materiału 23,20 PLN brutto
- wypełnienie 100% = 333 gr = koszt materiału 26,64 PLN brutto
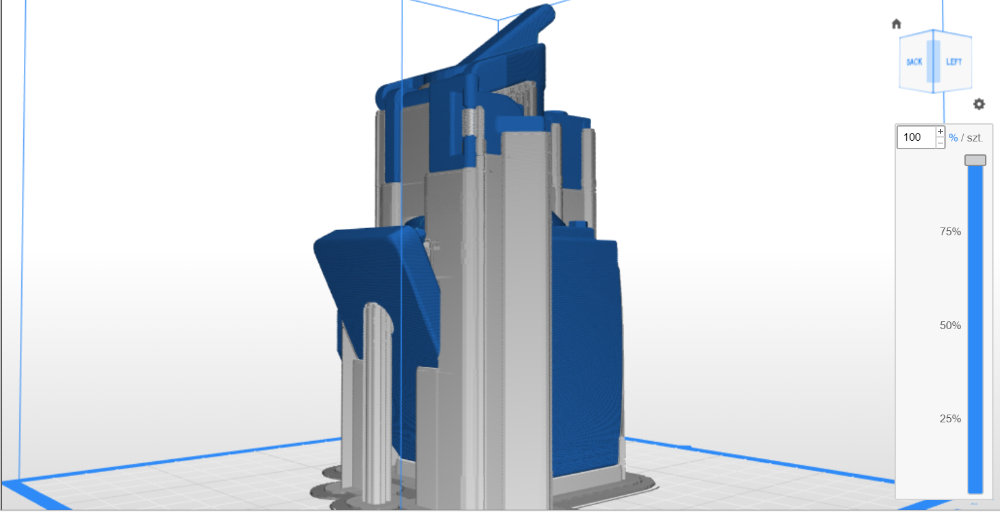
Wariant 1.2 – podpory
- wypełnienie 0% = 107 gr = koszt materiału 8,56 PLN brutto
- wypełnienie 10% = 138 gr = koszt materiału 11,04 PLN brutto
- wypełnienie 20% = 160 gr = koszt materiału 12,80 PLN brutto
- wypełnienie 50% = 226 gr = koszt materiału 18,08 PLN brutto
- wypełnienie 90% = 322 gr = koszt materiału 25,76 PLN brutto
- wypełnienie 100% = 360 gr = koszt materiału 28,20 PLN brutto
Jak zatem widać na tej symulacji, próba rezygnacji z podpór (co uczyni wydruk wadliwym) ma z punktu widzenia oszczędności na materiale znikome znaczenie i zamyka się w kwotach na poziomie kilku złotych.
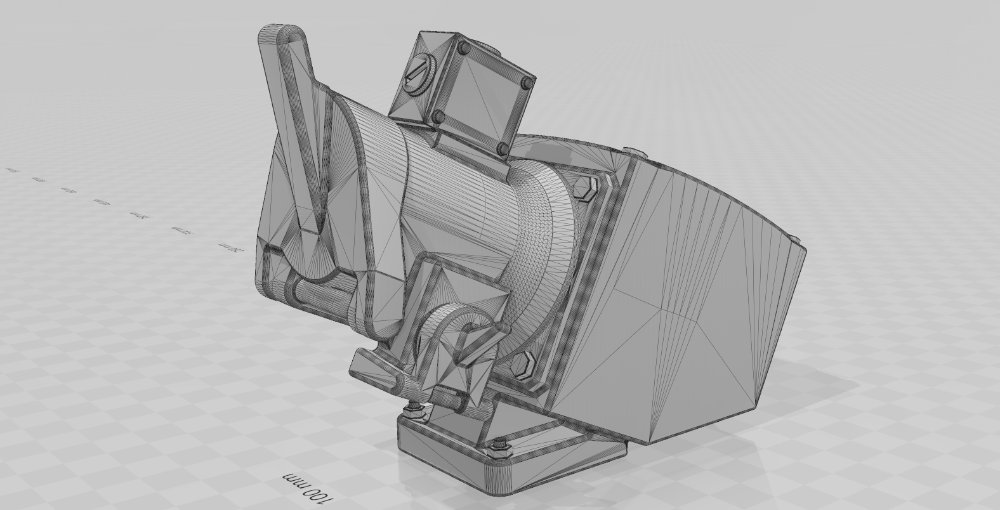
WARIANT 2 – druk 3D w poziomie
Drugi wariant to optymalizacja ułożenia wydruku 3D względem stołu roboczego, co zmieni sposób generowania się podpór i skróci czas pracy (ale to temat na oddzielny artykuł). Symulacje przeprowadzone wyłącznie z pdoporami.
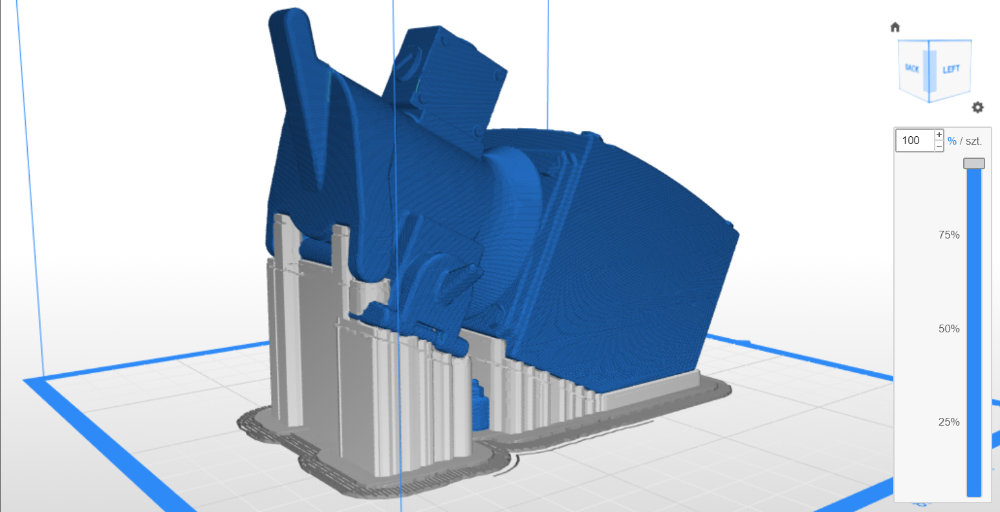
- wypełnienie 0% = 105 gr = koszt materiału 8,40 PLN brutto
- wypełnienie 10% = 135 gr = koszt materiału 10,80 PLN brutto
- wypełnienie 20% = 155 gr = koszt materiału 12,40 PLN brutto
- wypełnienie 50% = 218 gr = koszt materiału 17,44 PLN brutto
- wypełnienie 90% = 312 gr = koszt materiału 24,96 PLN brutto
- wypełnienie 100% = 350 gr = koszt materiału 28,00 PLN brutto
Różnice są iluzoryczne i z punktu widzenia zużycia materiału, ułożenie tego konkretnego detalu nie ma większego znaczenia.