Maciej Patrzałek, mimo wciąż młodego wieku (jest dwa lata młodszy ode mnie!) jest prawdziwym weteranem branży druku 3D w Polsce, działającym w niej praktycznie od jej samego początku, czyli połowy lat dwutysięcznych. Jest współwłaścicielem Solveere, firmy będącej czołową pracownią konstrukcyjną z branży automotive w kraju, specjalizującej się w rapid prototyping, jak również dystrybutorem wielu znanych marek drukarek 3D, w postaci enVisiontec, TierTime, M-Cor oraz Up! W wywiadzie, którego mi udzielił opowiada o początkach druku 3D w Polsce, licznych niuansach związanych z szybkim prototypowaniem oraz bardzo ciekawych spostrzeżeniach na temat branży.
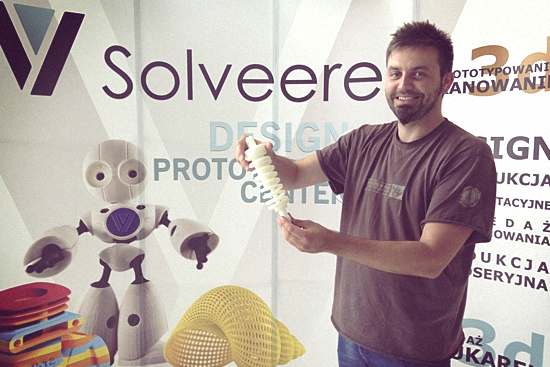
Solveere
We wstępie do wywiadu z Wulfnorem pisałem, że Wulfnora zna każdy. Z Maćkiem Patrzałkiem jest inaczej – to on zna każdego. Będąc w branży od samego jej początku, widział, wdrażał i realizował wszystko. Gdy jakiś czas temu miałem okazję odwiedzić Concordię Design i oglądać ich park maszynowy, okazało się, że był on instalowany przez Solveere, a architektem całego projektu był właśnie Maciek. Nawet modele, które oglądałem na miejscu były jego autorstwa. Równocześnie jego firma projektuje rzeczy dla najznamienitszych marek samochodowych i firm z branży przemysłowej w Polsce i na świecie. Z uwagi na specyfikę tych branż, poproszono mnie abym nie wymieniał żadnych nazw, jednakże mogę zapewnić, iż pisząc „najznamienitsze” miałem to dokładnie na myśli…
Wiedza Maćka na temat druku 3D jak i samej branży jest powalająca. To prawdziwy specjalista w tej dziedzinie i gdy wypowiada się na temat różnych aspektów technicznych czy produkcyjnych, trudno przejść obok tego obojętnie. Warto zapoznać się z jego opiniami, ponieważ pochodzą od człowieka, który działał w branży na kilka lat zanim Przemek Jaworski wystawił pierwsze zestawy do RepRapów na Allegro…
W trakcie rozmowy dołączył do nas na chwilę również Michał Kosiński, pracujący w Solveere od wielu lat, będący równie wielkim ekspertem w dziedzinie druku 3D. W prezentowanym wywiadzie dowiecie się zatem o początkach branży w Polsce, niuansach związanych z profesjonalnym drukiem 3D, czy dość ciekawej opinii na temat Formlabs…
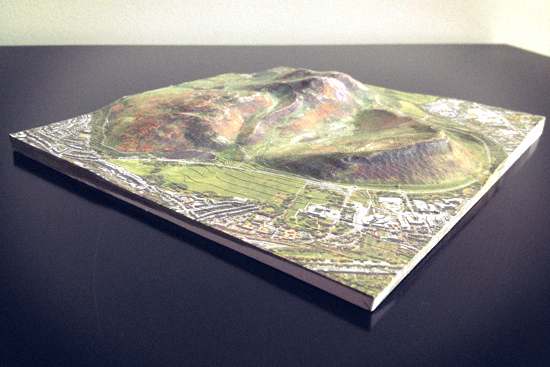
Paweł Ślusarczyk: Kto jako pierwszy sprowadził maszynę do druku 3D do Polski?
Maciej Patrzałek: To pytanie można podzielić na dwa: kto komercyjnie zaczął pracować na drukarkach 3D i realizować usługi sprzedając przy okazji urządzenia do druku 3D, oraz kto sprowadził je jako pierwszy? Z tego co pamiętam ,pierwsze drukarki 3D pojawiły się – jak podejrzewam, na uczelniach. Na Politechnice Rzeszowskiej mają sprzęt z 1997 roku, a na Politechnice Wrocławskiej posiadają ZCorpa i SLA. Politechnika Wrocławska miała ZCorpa 402 jeszcze zanim ZCorp zaczął sprzedawać urządzenia w Polsce. Jeśli chodzi o drukarki 3D działające komercyjnie, to według mojej wiedzy takie maszyny pojawiły się w latach 2005/2006 i to był przede wszystkim ZCorp. W Polsce było wtedy dwóch dealerów ZCorpa, miałem przyjemność pracować jako handlowiec w jednym z nich.
PŚ: A ty jak długo zajmujesz się drukiem 3D?
MP: Zacząłem działać w tej branży na przełomie lat 2005/2006.
PŚ: Jak to się zaczęło?
MP: Pracowałem w nieistniejącej już firmie Car Technology, która zajmowała się komercyjnym wykorzystaniem druku 3D i była równocześnie dealerem ZCorpa. Dzięki pracy tam oraz zdobytego doświadczenia w branży samochodowej i sprzedaży urządzeń do Rapid Prototyping wynikowym działaniem było powstanie firmy Solveere w 2008 roku.
PŚ: Czym zajmuje się Solveere?
MP: Sprzedażą i serwisem drukarek 3D, oraz usługami prototypowymi. Konstruujemy elementy do samochodów, mamy własne biuro konstrukcyjne.
PŚ: Jakie drukarki 3D macie w ofercie
MP: enVisiontec, TierTime, którego jesteśmy przedstawicielami na Europę Wschodnią, M-Cor, czyli drukarek 3D drukujących obiekty z papieru oraz drukarki desktopowe Up!

PŚ: Dlaczego akurat Up!?
MP: Ponieważ jest bardzo dobrą maszyną. Moim zdaniem ze wszystkich urządzeń dostępnych na ten moment na rynku, jest jedynym urządzeniem, które działa na zasadzie Plug&Print. Jest to jedyne moim zdaniem urządzenie tego typu, które posiada system automatycznej kalibracji. Nie trzeba nic kręcić, przestawiać śrubeczek, sprawdzać naciągów pasków nie ma czegoś takiego w serwisie urządzenia. Jesteśmy w stanie przejść do pozycji drukuj w przeciągu 10 minut. Do tego jest bardzo przyzwoity soft i świetne parametry jeśli chodzi o algorytmy, którymi operuje głowica, jeśli chodzi o rastrowanie.
PŚ: Czyli zasadniczą zaletą jest prędkość rozpoczęcia pracy?
MP: Prędkość i jakość wydruku. Poza tym te urządzenia mają możliwość drukowania z podporą, która jest edytowana przez materiał budulcowy. Nie ma problemów ze zwisami, sami definiujemy kąt podparcia, sposób rastrowania elementów w środku. Jesteśmy w stanie z bardzo prostego menu skalibrować tą maszynę – jest to kwestia kliknięcia w dwie ikony i podłączenia czujników do kalibracji lub podpięcia kabla. Kolejna rzecz, która jest moim zdaniem trafiona i wbrew pozorom jest bardzo istotna to stół roboczy. Jest optymalny – 14 x 14 x 14 cm z otwartą komorą. Drukujemy z ABS a nie na kiepskim PLA. Jeżeli chcesz wydrukować detal, który ma grubość przykładowo 2 cm wypełniony w pełni po całym obrysie stołu i jest w swej geometrii skomplikowany na tyle, że zmuszamy ABS do wygięcia się, to jeżeli nasz stół roboczy ma 20 x 20 x 20 cm, to przy założeniu ABS detal powygina się – jest to naturalna sprawa – przy sprzęcie z otwartą komorą. Albo wybieramy optymalne stoły, albo bajerujemy ludzi, że na dużym stole przy otwartej konstrukcji drukarki jesteśmy w stanie wydrukować wszystko.
PŚ: A jak to się ma np. do drukarki 3D Omni3D – Architect, która ma obszar zadruku 31 x 31 x 31 cm?
MP: Duży stół nie jest oczywistym rozwiązaniem wynikającym z niezawodności maszyny. Moim zdaniem jest to tylko fajny chwyt marketingowy, skuteczny dopóki użytkownicy nie zrozumieją, że w tych maszynach liczy się nie tylko wielkość stołu, ale też sposób rastrowania, nakładania podpór i to z czego się tak naprawdę drukuje? PLA jest materiałem, którego się nie stosuje na większą skalę w przemyśle. Jest stosowany w dużej mierze właśnie w branży RepRapowskiej. PLA ma mały skurcz…
Nawet w dużych maszynach pokroju np. Stratasys, kosztujących po xxxxxx €, o dużym stole roboczym, drukując jakieś skomplikowane geometrie z ABS czy PC/ABS zdarzają się sytuacje, że coś się odklei od stołu. Mimo tego, że jest to Stratasys, który ma bardzo dobry system rastrowania. A tu sprzęt, który kosztuje 6-7 tysięcy złotych ma obszar 31 x 31 x 31 cm….
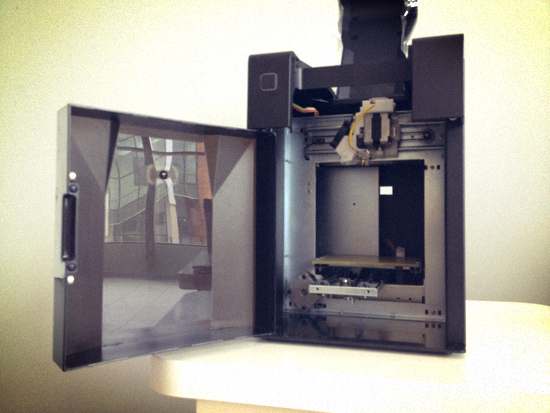
PŚ: Obszar zadruku na poziomie 14 x 14 x 14 cm twoim zdaniem optymalny, ale kontrargumentem może być to, że jest to przecież za mało na druk 3D większości obiektów? Że po to wszyscy starają się właśnie przejść na większy obszar roboczy i to maksymalnie maksymalizować? Czy z twojego doświadczenia i pracy przy profesjonalnym prototypowaniu faktycznie potrzebny jest duży obszar roboczy?
MP: Nie. Nie jest potrzebny. Z bardzo prostego powodu: prototypy modele z ABS się świetnie się klei. Jeżeli chcesz otrzymać dobrą jakość wyrobu niekoniecznie musisz pokazywać, że zrobisz to za jednym razem. To może być zgubne.
PŚ: A co powiesz zatem o Mamoth technology Mateiralise? Stół roboczy o długości 2 metrów, drukują z żywicy?
MP: Tak widziałem to. Ale to jest żywica i nie ma jej co porównywać. Tam nie występują tego typu problemy, to zupełnie inna technologia. Możesz zrobić stół 2 x 2 metry. Z resztą przy FDM też możesz wykorzystać tak duży stół, trzeba tylko pozwolić ABS`om stygnąć w sposób kontrolowany, a nie chaotyczny.
PŚ: Skoro przeskoczyliśmy na moment na żywicę – The Form 1, co byś powiedział na ten temat?
MP: Bardzo fajny sprzęt. Czekam aż pojawi się możliwość jego kupna bo chciałbym zobaczyć co jest w środku?
PŚ: A gdybyś miał możliwości, zająłbyś się dystrybucją tego sprzętu?
MP: Nie wiem? Nie wiem na ile byłoby to odpowiedzialne pod kątem serwisowym? A to jest o tyle istotne, że jak się okazuje w Polsce można sprzedawać wszystko, niekoniecznie nawet dobry sprzęt. Dlatego tak istotna jstt kwestia późniejszej opieki serwisowej i odpowiedzialności za te urządzenia.
PŚ: A jak wygląda to w przypadku Up!?
MP: Serwis mamy w Polsce.
PŚ: A kwestie bezpieczeństwa? Certyfikaty?
MP: Jest certyfikat CE i jest to wymagalne aby urządzenie było sprzedawane na polskim rynku. Więc ten certyfikat posiadamy. Są oznaczenia wszystkich stref gorących co jest opisane w instrukcji. Poza tym szkolimy za każdym razem kupujących w jaki sposób mają podejść do drukarki 3D.
PŚ: To jest urządzenie seryjne, nie ma żadnych upgrade`ów?
MP: Tylko software`owe. Nie robimy upgrade`ów maszynowych.
< Do rozmowy dołącza na moment Michał Kosiński >

podczas Festwalu Przemiany w CN Kopernik
PŚ: To powiedzcie coś na temat oprogramowania? To jest dedykowane oprogramowanie?
MP: Tak, jest to dedykowane oprogramowanie i jest bardzo proste. Jest w nim stół roboczy, możesz wstawić i dodać nowy model, możesz grupować tych modeli po kilkanaście. Możesz sobie wrzucić dowolny model i możesz go skompilować z innym. Nie jest tak jak na pierwszych oprogramowaniach do drukarek 3D, gdzie można było pracować tylko na jednym modelu. Kolejną rzeczą jest możliwość edycji sposobu drukowania modelu.
Michał Kosiński: model możesz skalować, jest opcja automatycznego ustawianie modelu na stoliku, użytkownik ma dowolność przesuwania, również obracania modelu o zadany kąt. Jest w stanie naprawić proste rzeczy narzędziem FIX. Kalibracja głowicy następuje również z poziomu programu, bez drukowania kostek czy innych tego typu zabiegów – wszystko dzieje się automatycznie. Nie ma możliwości uszkodzenia – tak jak w pierwszych RepRapach, gdzie mogłeś uderzyć stołem o głowicę. Tu nie ma tej opcji. To oprogramowanie jest o wiele prostsze i przyjazne użytkownikowi, niż inne tego typu rozwiązania na rynku. Jest dedykowane dla tego modelu urządzenia. Nie zmieniasz niczego wszystko się dzieje samo. Twierdzę, że to jest pierwsza drukarka Plug & Print.
PŚ: A dlaczego Up Mini jest zabudowany, a Up!2 Plus nie?
MP: Jest to bardziej zabieg marketingowy, nie ma to większego przełożenia na efektywność.
MK: Producent uznał, że zabudowana drukarka jest bardziej europejska i będzie się lepiej sprzedawać.
MP: Up Mini stoi u mnie w domu między sprzętem grającym a gitarą i się fajnie komponuje <śmiech>
PŚ: Hmm… A jak wygląda sytuacja z oparami ABS?
MP: Podobno jest to niezdrowe. Nie jestem w tej kwestii tak hurraoptymistyczny jak parę lat temu. Kupowanie sobie kilku urządzeń do open-space`u może nie być dobre. Wydaje mi się, że najlepiej gdy urządzenia tego typu pracują w wydzielonych ku temu miejscach. Niezbyt wierzę w drukarki 3D w domu, a w szczególności w to, że Formlabs wypuści domowe drukarki 3D z żywicy i będziemy trzymać te żywice w domu. Żywice akrylowe, epoxydowe są trujące!
PŚ: Poza tym dochodzi jeszcze kwestia opakowania? Co z nim zrobić? Nie można go po prostu wyrzucić do śmieci.
MP: To jedna rzecz, druga to pozostałości po materiale. Żywica żywicą, ale spójrzmy chociażby na FDM. Kiedyś się zastanawiałem: czy można zrobić coś pożytecznego robić z odpadami? Pracując na profesjonalnych maszynach potrafiliśmy przerobić 50 kg materiału rocznie. Potem zostają rolki, odpady itd. Z 50 kg odpada ci na podpory 20-30 kg?
PŚ: A co myślicie o urządzeniach pokroju Filabota i koncepcji żeby resztki ABS potem przerabiać?
MP: Dobry pomysł, tylko, że to jest już przegrzane. Tworzywa mają to do siebie, że za każdym razem gdy je przetapiasz, zmieniają się ich właściwości mechaniczne. Poza tym jest jeszcze jedna rzecz, jeżeli będziesz przerabiać te odpady, to musisz wyekstrudować potem wiązkę o bardzo idealnej średnicy. To jest duży problem, bo tego nie da się tak łatwo ostudzić, sprawić żeby skurcz występował równomiernie. Mamy swoją wyciskarkę aby od czasu do czasu za jej pomocą poeksperymentować i trochę na ten temat już wiemy.
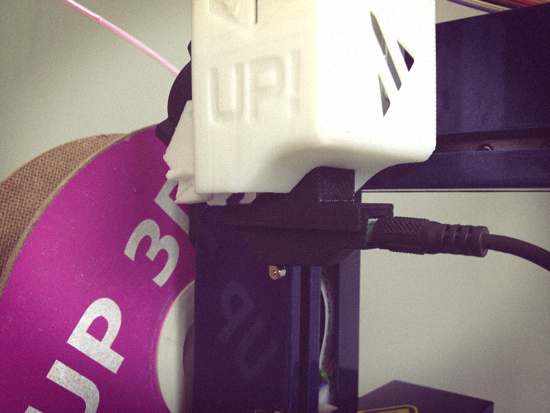
PŚ: Czy zamierzacie sprzedawać drukarki 3D takimi kanałami jak Komputronik czy RTV Euro AGD, a więc iść w ślady CB Printer lub Omni3D?
MP: Jesteśmy na tyle wyspecjalizowani w tym co robimy, że wolelibyśmy to sprzedawać swoim kanałem, mamy bezpośredni kontakt z tym klientem i jesteśmy w stanie te maszyny serwisować. Ponadto drukarki 3D są na tym etapie rozwoju, że nie są póki co urządzeniami, które nie będą generowały problemów. Cieszę się, że akurat sprzedaję Up!`y ponieważ nie generują one problemów. Jesli chodzi o wymienione przez ciebie sklepy, to zakładam, że w takim RTV EURO AGD może to kupić przysłowiowy Kowalski, który choć ma 6-7 tysięcy złotych na zakup drukarki 3D jest niekoniecznie przygotowany na jej zakup. Z tego mogą się rodzić póxniej problemy. My sprzedając drukarkę bezpośrednio klientowi, uświadamiamy go zarówno pod kątem obsługi jak i ze względu na potencjalne problemy czy zagrożenia. Do momentu jak nie ma personalnego kontaktu z człowiekiem to może to być problematyczne.
PŚ: Ile trwa realizacja zamówienia?
MP: Dwa dni. Generalnie mamy zatowarowanie na poziomie 30 sztuk. Zawsze. Natomiast jak wystrzelamy się – a już tak bywało, to klienci i tak nie czekali dłużej niż tydzień.
PŚ: Serwis i gwarancja?
MP: 12 miesięcy na wszystkie podzespoły – chyba, że ktoś urwie głowicę, a taki przypadek już mieliśmy. Serwis jest w Polsce, robimy wszystko u siebie.

PŚ: Opowiedz coś o prototypowaniu? Jakie technologie stosujecie?
MP: Mamy do dyspozycji maszyny DLP enVisiontec – pracujące w żywicy. Tier Time czyli FDM, maszyny Starasys. Mamy maszyny M-Cor czyli drukujące w pełnym kolorze, dokładnie mamy 4 mln kolorów do dyspozycji. Oprócz tego tzw. „brudne prototypowanie” w postaci Reactive Injective Molding i Vacuum Casting. Używamy też Objeta i ZCorpa.
PŚ: Czy jest możliwe wykonywanie profesjonalnych prototypów przy użyciu drukarek 3D klasy RepRap?
MP: Nie wiem? Nigdy nie drukowałem na RepRapie prototypów? Oczekiwania są różne. Robisz prototyp i klient życzy sobie raport wykonalności z tego prototypu i pomiary…
PŚ: Co myślisz o patentach SLS?
MP: Jak patenty zostaną uwolnione to będzie eldorado. Mam nadzieję, że pojawią się firmy, które będą w stanie wyprodukować niskobudżetową maszynę tego typu.
PŚ: A czy nie sądzisz, że powtórzy się sytuacja z Formlabsem? Uwolniła się nowa technologia – stereolitografia i na całym świecie pojawiła się… jedna drukarka tego typu, bo reszta się boi i czeka jak rozstrzygnie się kwestia patentów?
MP: Pytanie kto stoi za Formlabs?
PŚ: Nikt nie stoi…? Za Formlabs stoi Kickstarter?
MP: A skąd wiesz?
PŚ: …no nie wiem? Wiem, że są sygnały, że próbują się dogadać z 3D Systems?
MP: A nie myślałeś o tym, że to jest 3D Systems? To tylko moja dywagacja i nie przywiązywałbym się do tego, ale czysto hipotetycznie: Formlabs to jedyna firma, która na poważnie podeszła do tematu. 3D Systems miało patenty, a oni użyli część patentów w swojej drukarce 3D. Mimo wszystko ta drukarka ruszyła i udało się jej wyciągnąć pieniądze z Kickstartera? Tu jest sporo niewiadomych…?

PŚ: Microsoft wprowadza w Windows 8.1 oprogramowanie natywne do druku 3D, ma się pojawić nowy format pliku 3MF. Jakiś komentarz? Czy 3MF będzie nowym PDF?
MP: STL nie został wymyślony tylko dla drukarek 3D. STL jest plikiem tak zwanym plikiem skończonym – jest to siatka zapisana w formacie trójkątów. Siatka, która nie tylko definiuje powierzchnie zewnętrze i wewnętrzne ale też to co jest w środku. STL jest używany do symulacji wtrysku oraz naprężeń. Ciężko mi mówić, że się coś zmieni. Zmieni się może końcówka pliku – rozszerzenie, ale struktura pliku wydaje mi się, pozostanie ta sama.
PŚ: Plik Microsoftu ma być plikiem, który będzie posiadał masę informacji, które nie są zapisane w STL. Kolor tekstura, podpory itd.
MP: Plik parametryczny, STL`owski to plik wejściowy do drukarki 3D. A to co być może wypuści Microsoft, może będzie plikiem komunikacyjnym, czyli będzie zapisanym G Code`em, informacją o kolorze detalu – tak jak w przypadku plików wsadowych dla np. Mcora czy 3D system.
PŚ: I tym optymistycznym akcentem, kończymy naszą rozmowę. Dziękuję.
MP: Dzięki
Rozmawiał: Paweł Ślusarczyk
Foto: Paweł Ślusarczyk
Copyright: CENTRUM DRUKU3D