Firma PPHU POLIGRAF Wiesław Kasprowiak – właściciel PRINT-ME, jednej z najbardziej rozpoznawalnych marek filamentów do druku 3D w Polsce, w 2020 roku rozpoczął prace nad projektem badawczo-rozwojowym „ProtoPlastMaker 4.0. Innowacyjne centrum addytywno-skrawającej obróbki tworzyw sztucznych, odpowiadające na potrzeby prototypowania w przemyśle 4.0”. ProtoPlastMaker 4.0 jest projektem realizującym założenia konkursu ogłoszonego w ramach Osi Priorytetowej 1 – Gospodarka i innowacje, Działania 1.1 Badania i Innowacje – I typu projektu – Projekty B+R przedsiębiorstw w województwie Lubuskim.
W ramach projektu dofinansowanego z Funduszy Europejskich powstała nowoczesna maszyna o podstawowej przestrzeni roboczej na poziomie 1 x 1 x 2 metry, pozwalająca na druk 3D elementów bezpośrednio z granulatów tworzyw sztucznych oraz obróbkę w 5 osiach bez konieczności demontowania wydrukowanego elementu. Projekt realizowany był przy współpracy z Wydziałem Inżynierii Mechanicznej i Mechatroniki Zachodniopomorskiego Uniwersytetu Technologicznego w Szczecinie.
W centrum addytywno-skrawającym ProtoPlastMaker 4.0 zastosowano wiele innowacyjnych i zaawansowanych rozwiązań technologicznych i konstrukcyjnych zgodnych z ideą przemysłu 4.0. Dzięki temu maszyna umożliwia produkcje gotowych elementów bezpośrednio z granulatów tworzyw sztucznych. Poprzez zastosowanie technologii druku 3D oraz obróbki skrawaniem w 5 osiach możliwe jest zastąpienie kilku operacji/kroków technologicznych zwykle realizowanych na odrębnych maszynach: produkcję filamentu z granulatu, druk 3D oraz obróbkę/wygładzanie powierzchni wydrukowanego detalu. ProtoPlastMaker 4.0. realizuje powyższe kroki technologiczne w jednej, w pełni zautomatyzowanej fazie produkcyjnej (w jednym procesie).
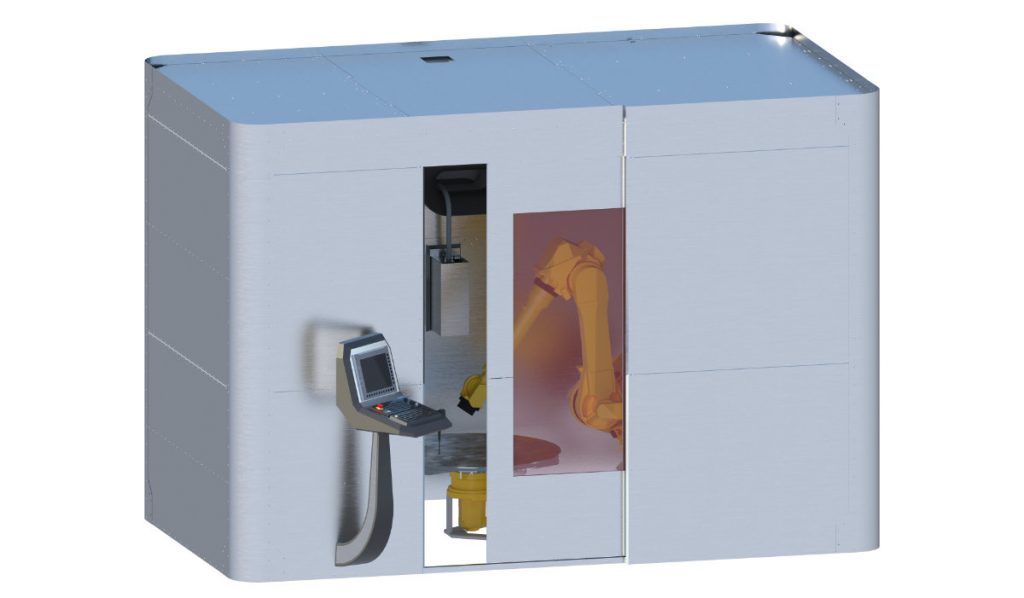
ProtoPlastMaker 4.0 jest szczególnie dedykowany do zastosowań w profesjonalnych firmach produkujących duże i wielkogabarytowe detale z tworzyw sztucznych oraz kompozytów zarówno dla produkcji seryjnej, jednostkowej jak i w działach R&D. Techniki przyrostowe jako jedne z niewielu pozwalają na wytwarzanie wydruków o skomplikowanych geometriach często bardzo trudnych lub niemożliwych do uzyskania tradycyjnymi metodami ubytkowymi. ProtoPlastMaker 4.0 dzięki zastosowaniu tych dwóch technologii, addytywnej (ekstruder drukujący) i ubytkowej (wrzeciono frezujące) łączy zalety obu technologii. Takie rozwiązanie umożliwia szybko i precyzyjne wyprodukowanie detali architektonicznych, elementów konstrukcyjnych czy części karoserii.
Szczególnie ciekawym zastosowaniem jest wytwarzanie małoseryjnych form wtryskowych lub do odlewów z żywic epoksydowych, drukowanych ze specjalnie dobranych granulatów. Wybrana forma jest najpierw drukowana z użyciem ekstrudera, a następnie wykańczana z użyciem wysokoobrotowego wrzeciona. Zastosowanie druku 3D pozwala na wydruk już wstępnie ukształtowanej formy, bez konieczności stosowania naddatków materiału. Następnie z zastosowaniem wrzeciona forma jest wykańczana zgrubnie i wykańczająco, wykonywane są także otwory konstrukcyjne i technologiczne. ProtoPlastMaker 4.0 jako jedno z niewielu rozwiązań pozwala na druk ze 100% wypełnieniem.
Programy do druku 3D jak i obróbki generowane są na podstawie autorskiego oprogramowania bazującego na SolidWorks oraz SolidCam. Bezprzewodowo wysyłając plik do maszyny użytkownik po zakończonym procesie otrzymuje wydrukowany detal z idealnie gładką powierzchnią sięgającą nawet Ra=0,72 𝜇𝑚. Ponadto oprogramowanie poza standardowymi opcjami, które znamy z podstawowych „slicerów” pozwala przygotować wydruk w postaci tzw. przygotówki – czyli bierze pod uwagę naddatki do obróbki skrawaniem, istnieje także możliwość zwiększenia zagęszczenia ścieżki drukowanego detalu w miejscach, gdzie przewidziana jest obróbka skrawaniem (np. pod otwory montażowe lub technologiczne).
W trakcie prac nad projektem dokonano także wielu badań, testów i analiz. Jedyni z ciekawszych badań, które przeprowadzono z praktycznego punktu widzenia, jest pomiar sił wynikających z obróbki skrawaniem na trzech kierunkach tj. X, Y oraz Z wydrukowanego w technologii 3D detalu, co w praktyce przełożyło się chociażby na sposób mocowania detalu do podłoża oraz rzutowało na wybór kinematyki realizowanej przez prototyp. Naukowcy z zespołu PRINT-ME wraz z Wydziałem Inżynierii Mechanicznej i Mechatroniki ZUT przeprowadzili również analizy chropowatości powierzchni, bezpośrednio po wydruku 3D oraz po obróbce skrawaniem, wraz z bardzo szczegółową analizą parametrów technologicznych skrawania w kontekście jakości wykończenia powierzchni obrabianej (chropowatości Ra).
W pierwszej kolejności zostaną omówione wyniki pomiarów chropowatości powierzchni dla różnych parametrów technologicznych skrawania, z wykorzystaniem różnego rodzaju materiałów. Badania przeprowadzono dla trzech podstawowych tworzyw, wykorzystywanych w druku 3D, tj. PLA, PET-G oraz ABS.
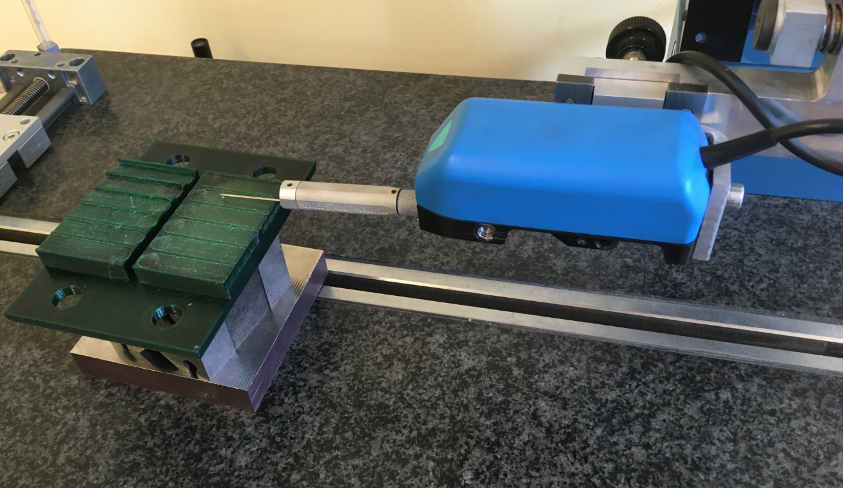
Z oczywistych względów wynik chropowatości detalu, tuż po druku 3D zależny jest od wielu czynników jak np. wysokość warstwy, klasy drukarki, prędkości itp. Niemniej jednak w trakcie badań dokonano wszelkich starań, aby jakość wydruku okazała się jak najlepsza. Wykorzystano praktycznie najwyższą rozdzielczość druku oraz dobrano tak parametry, aby zachować największą dokładność geometryczną. Wydruki wykonano na drukarce Zortrax M300. Jak wynikło z pomiarów próbki bezpośrednio po wydruku, uzyskano powierzchnię o chropowatości Ra=4,57. Wynik pomiarów pokrywa się praktycznie w przypadku każdego z materiałów tj. PLA, PET-G oraz ABS . W kolejnym etapie dokonano prób skrawania dla różnych parametrów technologicznych obróbki, co prezentują poniższe rysunki:
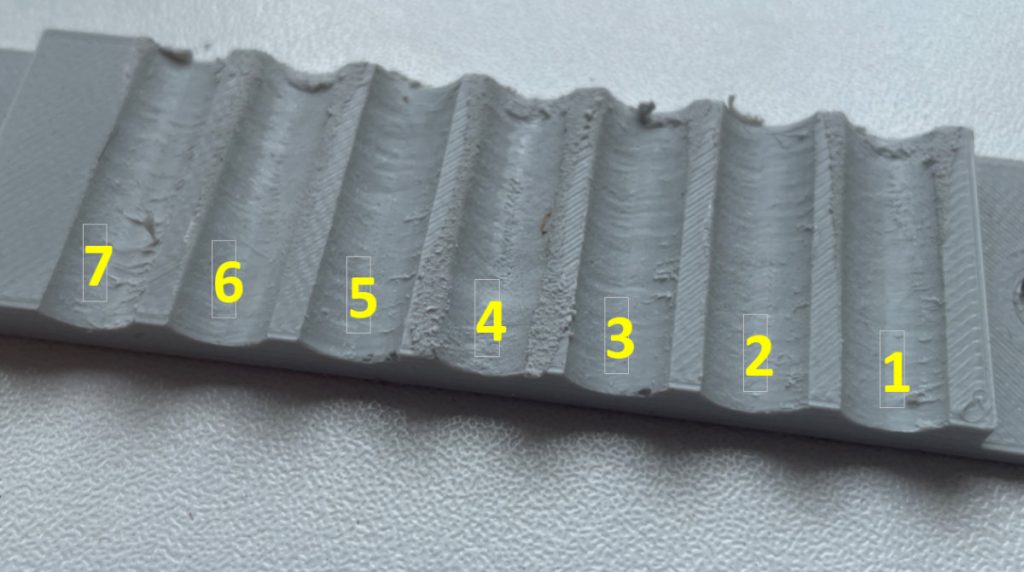
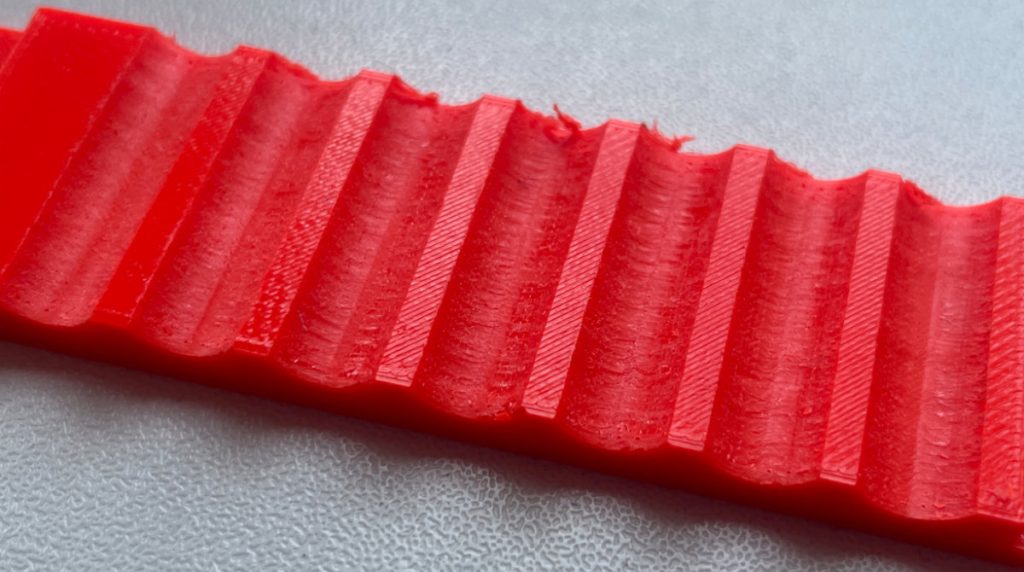
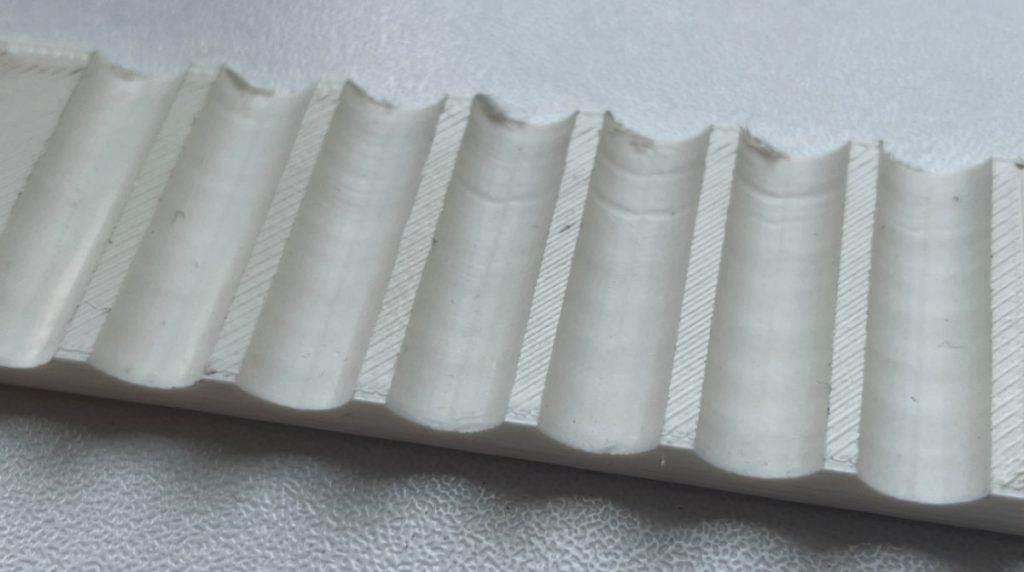
W poniższej tabeli zostało zawartych siedem zmiennych parametrów technologicznych, które były brane pod uwagę w trakcie testów, gdzie:
- ap – to szerokość/głębokość warstwy skrawanej [mm]
- Vc – prędkość skrawania [m/min]
- N – obroty [obr/min]
- Fz – prędkość posuwu [mm]
- Fmin – prędkość skrawania [mm/min]
Nr | ap [mm] | Vc [m/min] | N [rpm] | Fz [mm] | Fmin [mm/min] |
---|---|---|---|---|---|
1 | 2 | 271 | 10800 | 0,08 | 1728 |
2 | 2 | 301 | 12000 | 0,08 | 1920 |
3 | 2 | 331 | 13200 | 0,08 | 2112 |
4 | 2 | 362 | 14400 | 0,08 | 2304 |
5 | 2 | 392 | 15600 | 0,08 | 2496 |
6 | 2 | 423 | 16800 | 0,08 | 2688 |
7 | 2 | 458 | 18240 | 0,08 | 2918 |
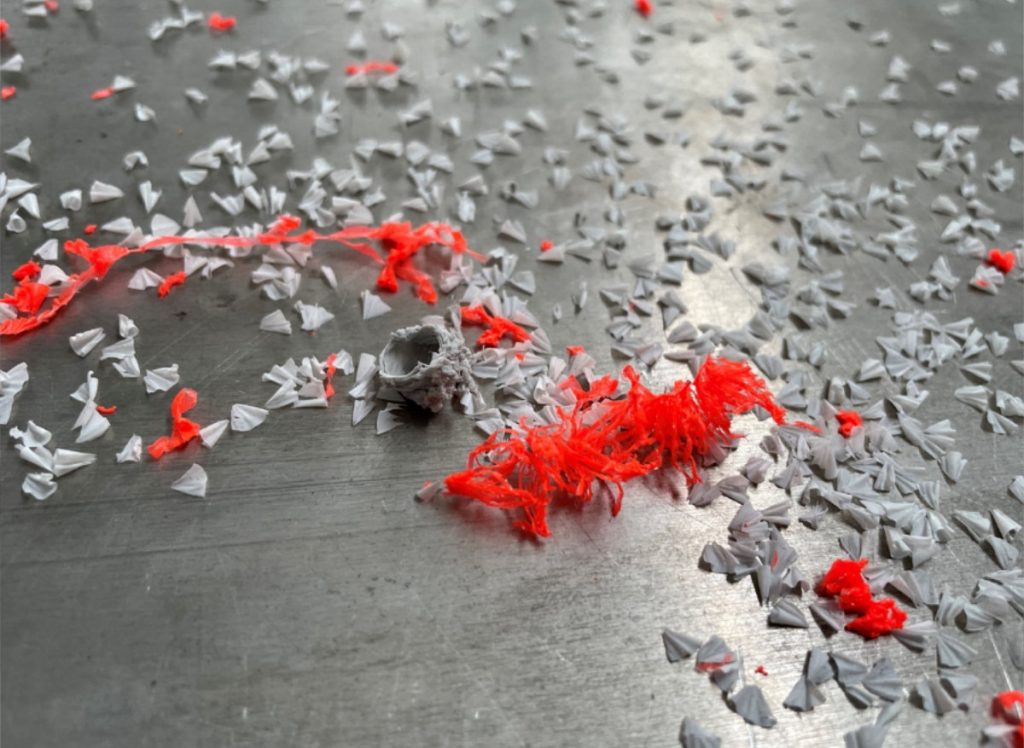

Na pierwszy rzut oka, widoczna jest aglomeracja wiórów pochodzących ze skrawania próbki PLA, co wynika w głównej mierze z niskiej temperatury zeszklenia tego materiału i małej odporności termicznej. Najlepszy rezultat, jaki udało się uzyskać dla danego materiału to Ra =3,7, co nie jest zadowalającym efektem i w ocenie autorów, materiał ten pomimo tego, że cieszy się dużą popularnością, nie nadaje się do obróbki skrawaniem. W przypadku PET-G skrawalność tego materiału jest na dużo lepszym poziomie niż w przypadku polilaktydu, lecz odporność termiczna polimeru, która sięga około 70°C, nie jest w stanie zagwarantować satysfakcjonującej jakości powierzchni.
Bardzo obiecujące są wyniki badań dotyczących próbek wykonanych z ABS. Odporność termiczna tego materiału jest rzędu 90°C, co jak się okazało jest wystarczające, aby uzyskać bardzo dobrej jakości powierzchnię, ponadto materiał wykazuje bardzo dobre cechy skrawalności dając rezultat Ra=0,72 𝜇𝑚 – co można porównać do powierzchni stali po procesie polerowania.
Jak już wspomniano jednym z badań był również pomiar sił skrawania. Niezależnie od materiału uzyskano bardzo porównywalne wyniki. Siła skrawania, nie była większa niż 15 N, w kierunku, gdzie składowa siły skrawania ma największą wartość tj. w kierunku posuwu. Co ciekawe na wielkość siły skrawania nie miało wypływu także narzędzie. Siła okazała się porównywalna dla narzędzia zawierającego jedno, czy cztery ostrza. Ciekawostką może być to, że im mniej ostrzy zastosowano, tym uzyskano lepszą jakość powierzchni, co można tłumaczyć zachodzącymi w trakcie skrawania zjawiskami termodynamiki i mniejszym nagrzewaniem się polimeru.

Podsumowując spośród badanych materiałów obróbka skrawaniem ABS daje najlepsze rezultaty, ponadto wyższe prędkości obrotowe i posuwy na ząb pozwalają na uzyskanie powierzchni o mniejszej chropowatości (najniższy Ra=0,72um). Obróbka skrawaniem PET-G nie wykazała takiej korelacji z parametrami skrawania oraz nie zaleca się obróbki skrawaniem PLA ze względu na niską temperaturę zeszklenia.

Artykuł jest finansowany w ramach projektu numer RPLB.01.01.00-08-0020/19 – Oś Priorytetowa 1 – Gospodarka i innowacje, Działania 1.1 Badania i Innowacje – I typu projektu – Projekty B + R przedsiębiorstw w województwie Lubuskim.