Jak opisywaliśmy to już niezliczoną ilość razy, jednym z największych wyzwań przed jakimi stoją użytkownicy drukarek 3D jest problem skurczu materiału. Skurcz występuje praktycznie w każdej technologii przyrostowej, bez względu na gatunek materiału jakiego się używa oraz typ maszyny. Druk 3D jest pod tym względem uczciwy – ze skurczem muszą zmagać się zarówno użytkownicy tanich, amatorskich drukarek 3D typu FDM / FFFm jak i operatorzy kosztujących kilka milionów złotych przemysłowych systemów do druku 3D z metalu.
Mimo że temat skurczu materiału był już podejmowany wielokrotnie na łamach portalu, nigdy tak naprawdę nie dokonaliśmy prostego wyjaśnienia skąd i dlaczego się on w gruncie rzeczy bierze? W niniejszym artykule skupimy się na najpopularniejszej i najbardziej rozpowszechnionej technologii druku 3D czyli FDM / FFF – w przypadku innych metod addytywnych źródłem problemów są inne czynniki, dlatego informacji tu zawartych nie należy przekładać na druk 3D z żywic światłoutwardzalnych, czy materiałów w formie proszków.
Jeżeli jesteście początkującymi użytkownikami drukarek 3D drukujących z filamentów, lub dopiero przymierzacie się do ich zakupu, warto abyście zapoznali się z trzema wcześniejszymi artykułami z tego cyklu:
Technologia FDM – ROZDZIAŁ 1 – Co to jest i na czym polega…?
Technologia FDM – ROZDZIAŁ 2 – Jak działa drukarka 3D i na co zwracać uwagę przy jej zakupie…?
Technologia FDM – ROZDZIAŁ 3 – Od wirtualnego modelu do wydruku 3D
Technologia FDM wykorzystuje w procesie wytwórczym termoplasty, czyli tworzywa sztuczne wykorzystywane do formowania geometrii w wysokich temperaturach. Modele drukowane w tej technologii powstają poprzez nakładanie kolejnych warstw półpłynnego materiału, który jest wytłaczany (tzw. “ekstrudowany“) z podgrzewanej dyszy. Materiał ma formę żyłki o stałej średnicy (1,75 mm lub 2,85 mm) nawiniętej na szpulę – jego zwyczajowa nazwa to „filament”.
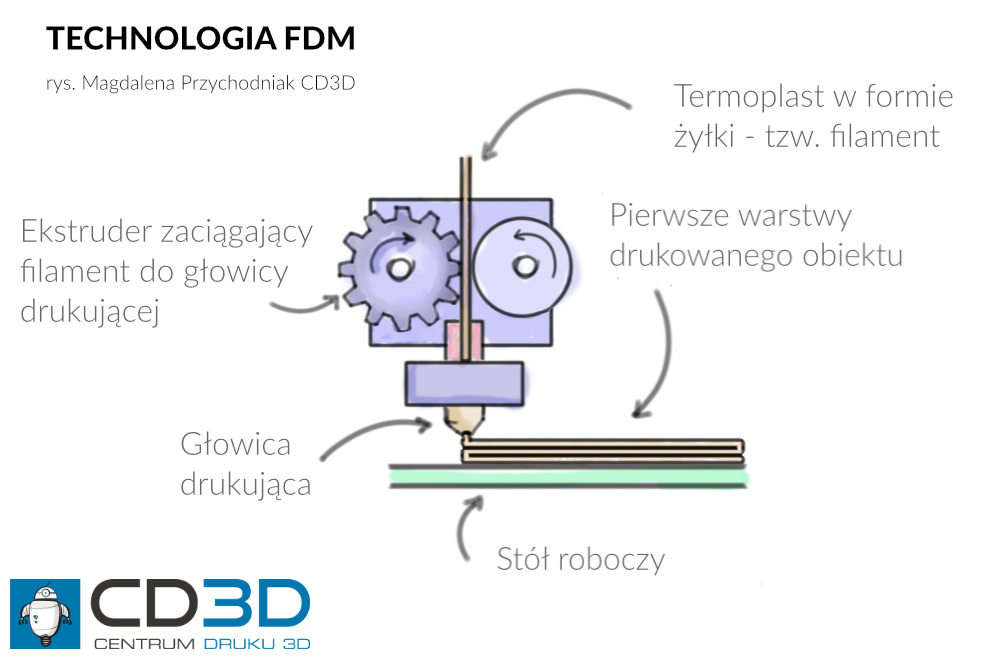
Głowica drukująca porusza się nad stołem roboczym w osiach XY (lub głowica w osi X, a stół roboczy w Y) i niczym ploter nakłada na powierzchnię stołu roboczego półpłynne tworzywo sztuczne, rysując za jego pomocą kształt. W ten sposób powstaje pierwsza warstwa modelu. Gdy pierwsza warstwa jest “narysowana“, w zależności od konstrukcji drukarki 3D stół roboczy opuszcza się w osi Z, lub głowica podnosi się w osi Z i nakładana jest kolejna warstwa modelu 3D. W ten sposób warstwa po warstwie powstaje model przestrzenny.
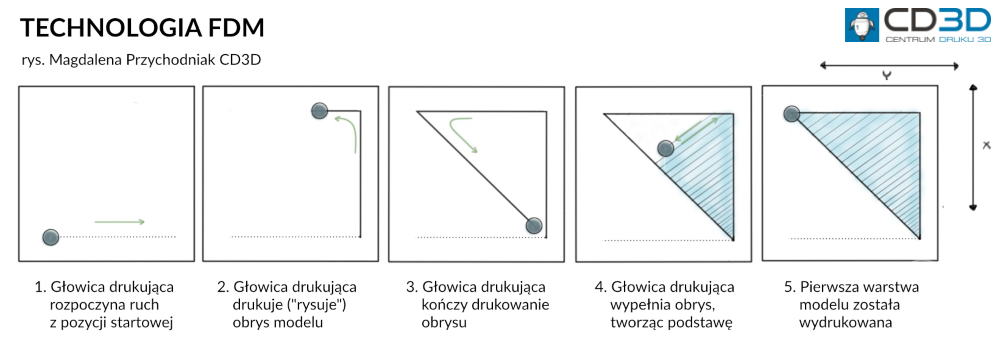
Gdy głowica nałoży kilka pierwszych warstw materiału – w zależności od jego gatunku, rozmiarów wydruku 3D oraz konstrukcji drukarki 3D – mogą zacząć objawiać się pierwsze problemy ze skurczem materiału. Zasada jest jedna – jeżeli już na samym początku wydruku 3D zaobserwujemy że materiał się odkształca na powierzchniach, krawędzie wydruku 3D odklejają się od powierzchni stolika roboczego i podwijają do góry, nie ma na co czekać – wydruk należy przerwać, ponieważ dalej będzie już tylko gorzej…
Co jest tego powodem? Niekontrolowane studzenie / chłodzenie się materiału. Proces wygląda w następujący sposób:
- materiał w formie żyłki trafia do głowicy drukującej, gdzie w zależności od gatunku jest rozgrzewany do temperatury 190-270°C (mowa oczywiście o drukarkach 3D klasy amatorskiej lub desktop); dzięki temu materiał przechodzi do stanu półpłynnego, co umożliwia głowicy „narysowanie” warstwy detalu
- gdy zostanie wytłoczony przez głowicę i zespoli się z materiałem na niższej warstwie – stygnie; stygnięcie jest bardzo szybkie – ze 190-270°C momentalnie przechodzi do temperatur na poziomie kilkudziesięciu stopni Celsjusza
- w zależności od wysokości detalu oraz tego czy drukarka 3D jest wyposażona w podgrzewany stół roboczy (a jeśli jest, to jaką temperaturę ma ustawioną), wytwarzają się różne strefy ciepła, które przekładają się na skurcz.
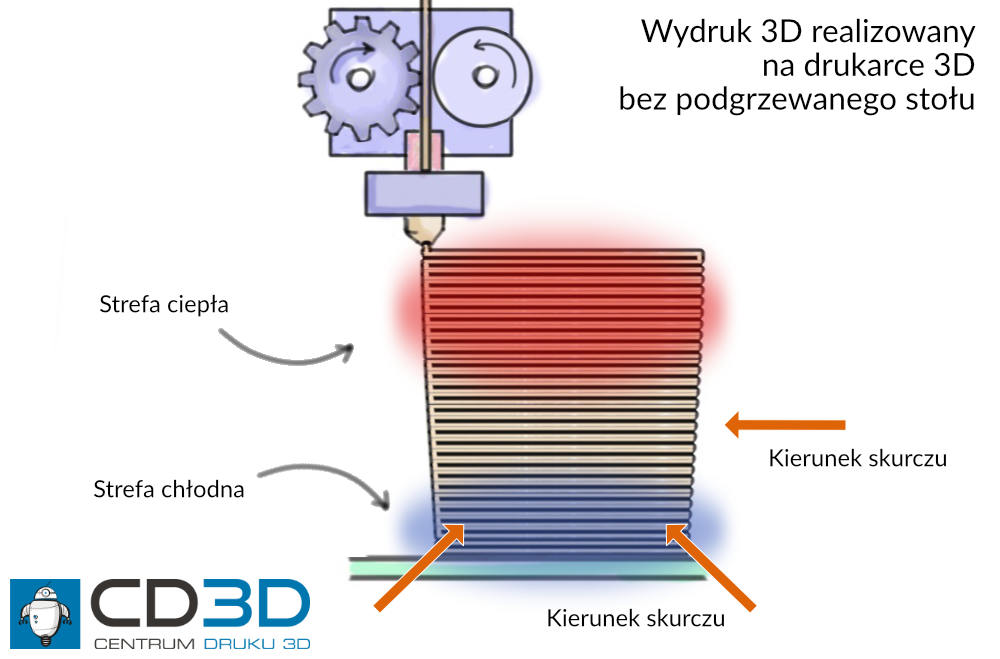
Znakomita większość materiałów termoplastycznych rozszerza się po podgrzaniu i kurczy po schłodzeniu. Drukowany detal jest poddawany naprężeniom – na rysunku powyżej widać, jak chłodny obszar kurczy się do wewnątrz we wszystkich kierunkach. Będzie to najbardziej widoczne przy miejscu styku detalu z powierzchnią stołu.

Skurcz rośnie wraz ze zwiększaniem się powierzchni detalu. Przykładowo, detal o długości 20 cm, drukowany z materiału, który kurczy się o 2% podczas schładzania, teoretycznie skurczy się do 19,2 cm. W praktyce jednak środek detalu pozostaje nieruchomy, gdyż jest przytwierdzony do podłoża stolika – skurczą się tylko jego krawędzie.
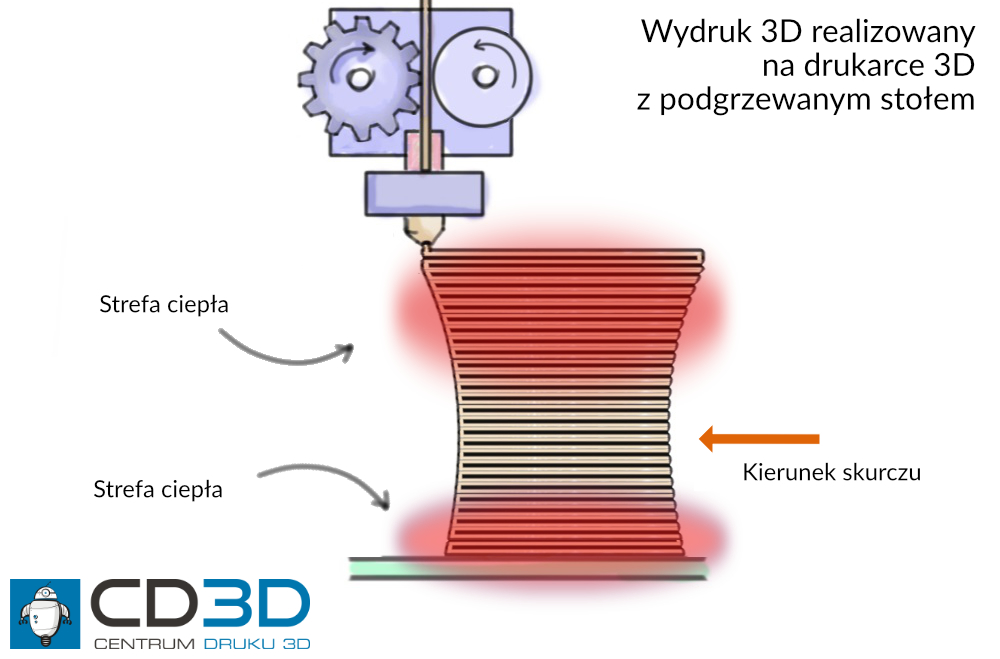
Jeżeli korzystamy z drukarki 3D wyposażonej w podgrzewany stół roboczy i spód wydruku bardzo mocno przylegnie do jego podłoża, nie oznacza to, że skurcz zniknie – pojawi się po prostu na wyższych warstwach detalu. Dojdzie albo do miejscowej deformacji, albo krawędzie detalu po prostu popękają, nie mogąc poradzić sobie z naprężeniami.
Najlepszym rozwiązaniem tego problemu jest stosowanie drukarek 3D wyposażonych w zamknięte, a najlepiej podgrzewane komory robocze. Wydruk powstaje wtedy w miarę kontrolowanym środowisku – temperatura jest stała i nie występują tak drastyczne strefy chłodu, jak ma w przypadku otwartych urządzeń.
Problem skurczu jest różny w przypadku różnych gatunków tworzyw sztucznych. Najmniej podatne na skurcz jest PLA oraz do pewnego stopnia PETG czy HIPS (oraz cała masa materiałów kompozytowych, opartych o nie). Skurcz jest istotnym problemem podczas pracy z ABS, nylonem (PA6) oraz wszystkimi tworzywami sztucznymi, które możemy zakwalifikować jako techniczne – przemysłowe. Pamiętajmy jednak o jednej rzeczy: to że dany materiał ma niski skurcz, nie oznacza że nie posiada go wcale. Warto o tym pamiętać decydując się na wielkogabarytowe wydruki realizowane na dużych, lecz otwartych konstrukcjach drukarek 3D.