Arrinera Hussarya w kontekście technologii 3D powraca… W lutym bieżącego roku informowaliśmy o projekcie drukowanych elementów polskiego supersamochodu przez poznańskie Omni3D – teraz mamy dla Was kolejne case study związane z tym pojazdem, ale dla odmiany oparte o technologię skanowania 3D. Polski producent skanerów 3D – SMARTTECH, wspierał Arrinerę w obszarze inżynierii odwrotnej.
Arrinera Hussarya to auto-legenda, które od dekady rozpala emocje osób zajmujących się motoryzacją oraz… inwestycjami giełdowymi. W tym roku projekt po raz kolejny nabrał realnych kształtów, a podziwiał go osobiście sam wicepremier i minister rozwoju i finansów – Mateusz Morawiecki. Samochód w przeciwieństwie do większości współczesnych polskich projektów motoryzacyjnych został stworzony od podstaw. Wszystkie części karoserii, silnika i wnętrza zostały zaprojektowane od nowa, tak aby nie tylko spełniały wyśrubowane wymagania typowe dla pojazdów sportowych, ale również posiadały atrakcyjną estetykę. To postawiło projektantów przed nie lada wyzwaniem – zarówno od strony projektowej jak i budżetowej.
Twórcy Arrinery długo poszukiwali metody na przyśpieszenie i redukcję kosztów tworzenia auta. Ostatecznie postanowili zastosować inżynierię odwrotną, czyli pozyskać dokumentację techniczną istniejącego elementu w celu jego ponownego przeprojektowania. W pracy wykorzystano skaner MICRON3D green z 10 megapikselowym detektorem, produkcji SMARTTECH, z pomocą którego zaprojektowali obudowę sprzęgła.
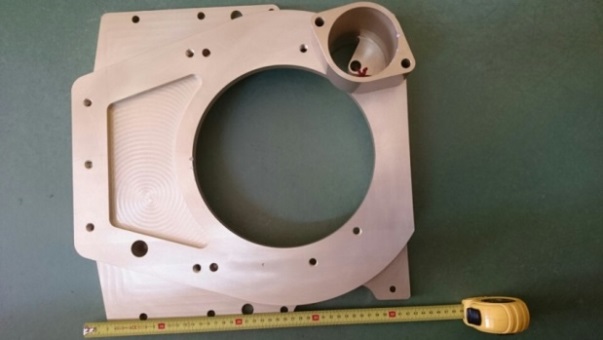
Sprzęgło stosowane w samochodach sportowych jest poddawane zupełnie innym siłom i przeciążeniom niż odpowiednik działający w tradycyjnych autach miejskich. 810Nm momentu obrotowego wymaga użycia nie tylko niezawodnej, ale również lekkiej konstrukcji sprzęgła. Skaner 3D SMARTTECH umożliwił pozyskanie dokumentacji technicznej istniejącej już na rynku obudowy oraz przeprojektowanie jej w oprogramowaniu CAD w celu instalacji mocowań dopasowanych do konstrukcji auta.
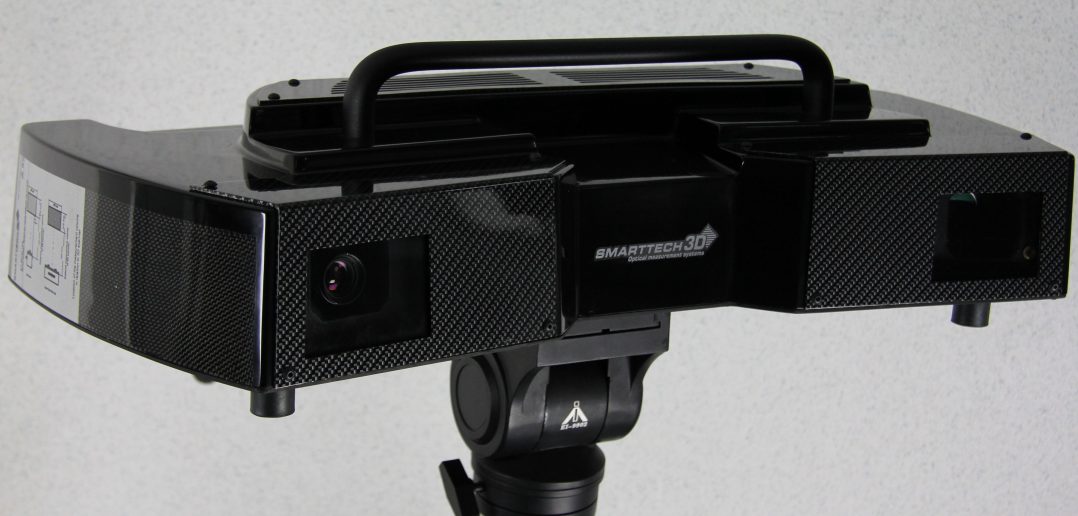
Skaner MICRON3D green wykorzystuje w skanowaniu zielone światło LED, co pozwala na osiągnięcie wyników o 30% dokładniejszych niż skanery 3D wykorzystujące światło białe. Przy objętości pomiarowej 800 x 600 mm, skaner 3D pozyskuje chmurę punktów reprezentującą zeskanowany kształt z dokładnością 0,084mm. W praktyce oznacza to, że za pomocą pojedynczego pomiaru można zeskanować powierzchnię równą 80 cm na 60 cm.
MICRON3D green jest certyfikowany metrologicznie według niemieckiej normy VDI/VDE 2634, dzięki czemu Arrinera miała pewność, że błąd pomiaru nie przekracza wartości podanych w certyfikacie dokładności urządzenia. Istotne jest również to, że urządzenie nie wymaga dodatkowej kalibracji, gdyż jest na stałe skalibrowane na jedną objętość pomiarową.
Pomiar za pomocą skanera 3D polega na wyświetleniu prążków na mierzonej powierzchni. Prążki odkształcają się na jej krzywiźnie, co rejestruje detektor wbudowany w głowicę skanującą. Urządzenie mierzy jedynie powierzchnie, które są widoczne dla detektora. Aby móc pozyskać z każdej strony kompleksową informację geometryczną, obiekt musi zostać zeskanowany za pomocą stolika obrotowego. Jego nośność wynosi ponad 300 kg, a średnica jest równa 50 cm, co w zupełności wystarcza do pełnego pomiaru większości części samochodowych.
Obraz z detektora jest następnie przekształcany w chmurę punktów dzięki specjalnemu algorytmowi oprogramowania sterującego. Każdy z punktów to informacja geometryczna opisana za pomocą współrzędnych X, Y, Z, które po odpowiedniej obróbce mogą być użyte do kontroli jakości lub – tak jak w przypadku Arrinery – do przeprojektowania i wyfrezowania modelu na maszynie CNC.
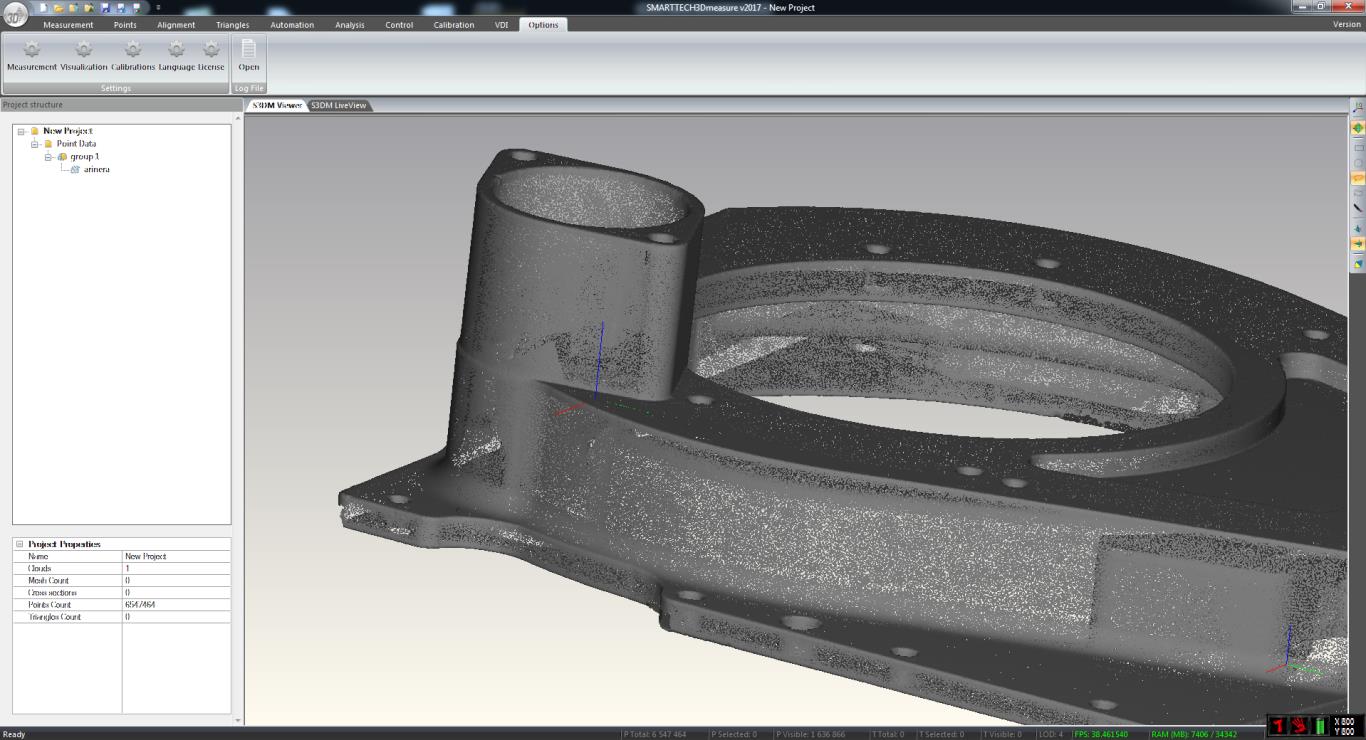
W zależności od rozdzielczości, chmura punktów z jednego pomiaru może składać się z 5 lub 10 milionów punktów, odpowiednio dla rozdzielczość 5 lub 10 megapikseli. Ilość megapikseli wpływa przede wszystkim na szczegółowość danego obiektu. W wypadku Arrinery zastosowano skaner 3D z 10 megapikselowym detektorem, gdyż pojawiła się potrzeba dokładnego odwzorowania krawędzi mierzonego obiektu.
Obudowa sprzęgła została zeskanowana z dwóch stron, co pozwoliło uzyskać dwie chmury punktów. Na każdą z nich przypadało po sześć pojedynczych pomiarów. Dzięki stolikowi obrotowemu zintegrowanemu ze skanerem 3D, pojedyncze pomiary są do siebie wstępnie dopasowane. Alternatywne opcje pozwalają użyć np. markerów pozycjonujących.
Po zakończeniu procesu skanowania 3D istnieje możliwość przekształcenia chmur punktów w siatkę trójkątów w oprogramowaniu SMARTTECH3Dmeasure, które jest dostarczane wraz z każdym skanerem 3D firmy. Najpierw jednak trzeba dopasować do siebie wyniki pomiarów. Wykorzystuje się do tego metodę „na trzy punkty” polegającą na wybraniu trzech wspólnych punktów dla obydwu chmur. Na ich podstawie oprogramowanie automatycznie określa pozycję wyników względem siebie. Celem jest uzyskanie chmury punktów w całości reprezentującej zeskanowany obiekt. Użycie stolika obrotowego znacząco uprościło operację łączenia pomiarów ze względu na podzielenie ich na dwie grupy punktów odpowiadające obydwu stronom.
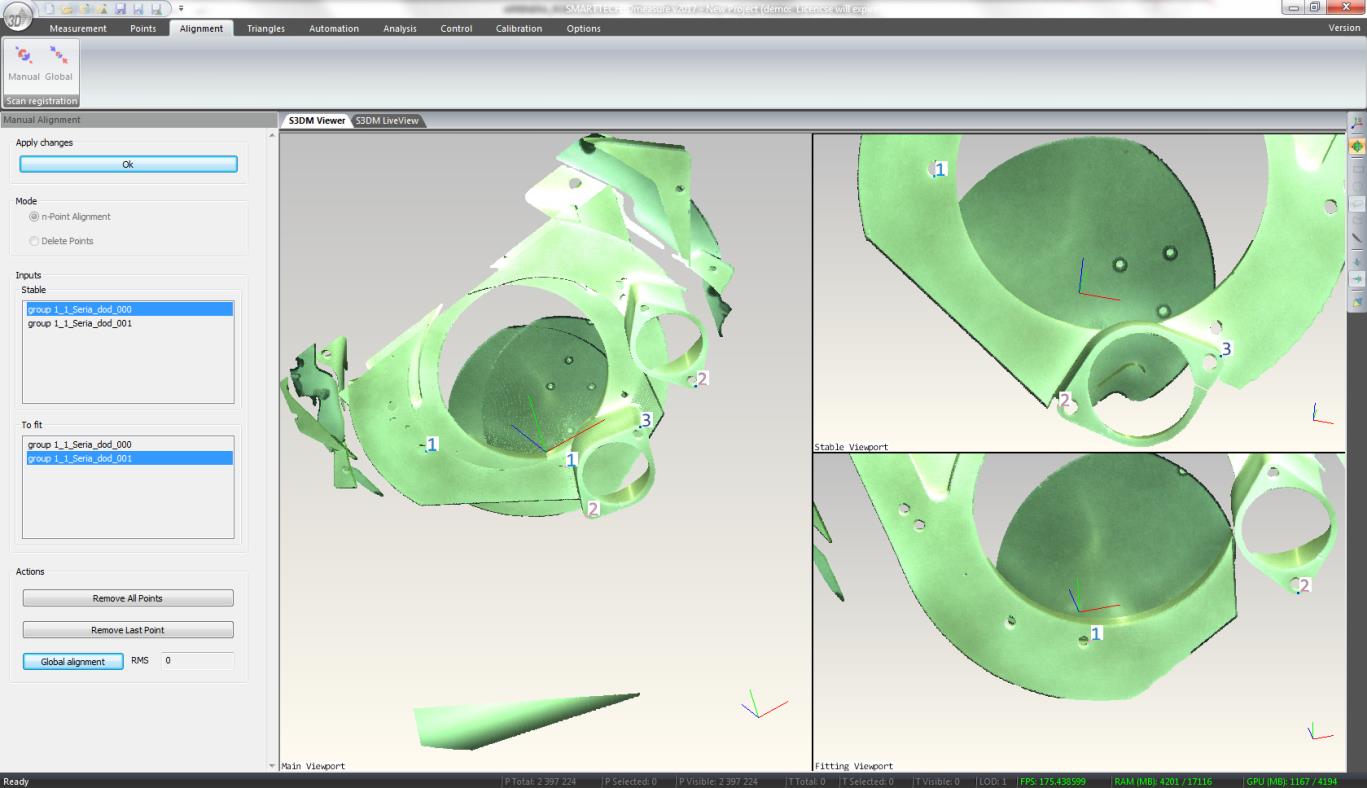
Przed przekonwertowaniem chmury punktów w siatkę trójkątów należy zastosować funkcję „Dokładnego dopasowania„, która na podstawie położeń punktów precyzyjnie dopasowuje do siebie wszystkie chmury. Na tym etapie pozostało jeszcze usunięcie pokryć, czyli wzajemnie pokrywających się elementów wspólnych poszczególnych pomiarów.
Tak przygotowana chmura punktów zostaje następnie przetworzona na siatkę trójkątów. Na potrzeby Arrinery jako format zapisu wybrano .STL, który jest najpopularniejszym formatem dla siatek trójkątów ze względu na kompatybilność z drukarkami 3D i frezarkami. Siatka może zostać również użyta jako doskonała baza do modelowania CAD. Arrinera wykonała i dostosowała model CAD, a następnie przesłała go do oprogramowania zarządzającego maszyną CNC. Skanowanie 3D nie tylko odciążyło budżet firmy, ale też umożliwiło produkcję dedykowanej części.
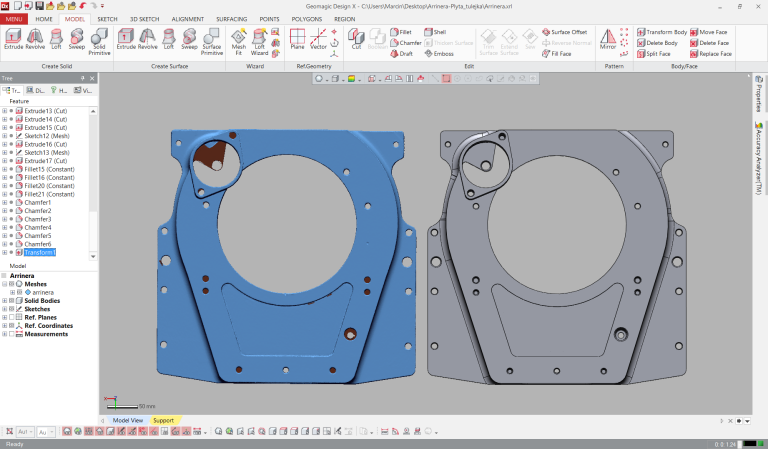
Skanowanie 3D na stoliku obrotowym w laboratorium pomiarowym nie zawsze jest możliwe ze względu na gabaryty obiektu. W takiej sytuacji można zrobić pomiary na linii produkcyjnej dzięki alternatywnej metodzie wykorzystującej markery.
Podczas produkcji pierwszego egzemplarza częstą sytuacją jest, że pomimo długofalowego projektowania, nie wszystkie części są dokładnie takie same, jak pierwotnie planowano. Przed takim problemem stanęli inżynierowie Arrinery. Lewy próg samochodu został dostosowany w celu optymalizacji konstrukcji. Chcąc zachować pełną symetrię pojazdu, próg z drugiej strony musiał zostać wytworzony w dokładnie takim samym kształcie. Tradycyjne metody pomiarowe stosowane przez Arrinerę nie pozwalają na pozyskanie pełnej geometrii, dlatego podjęto decyzję o wykorzystaniu technologii 3D firmy SMARTTECH.
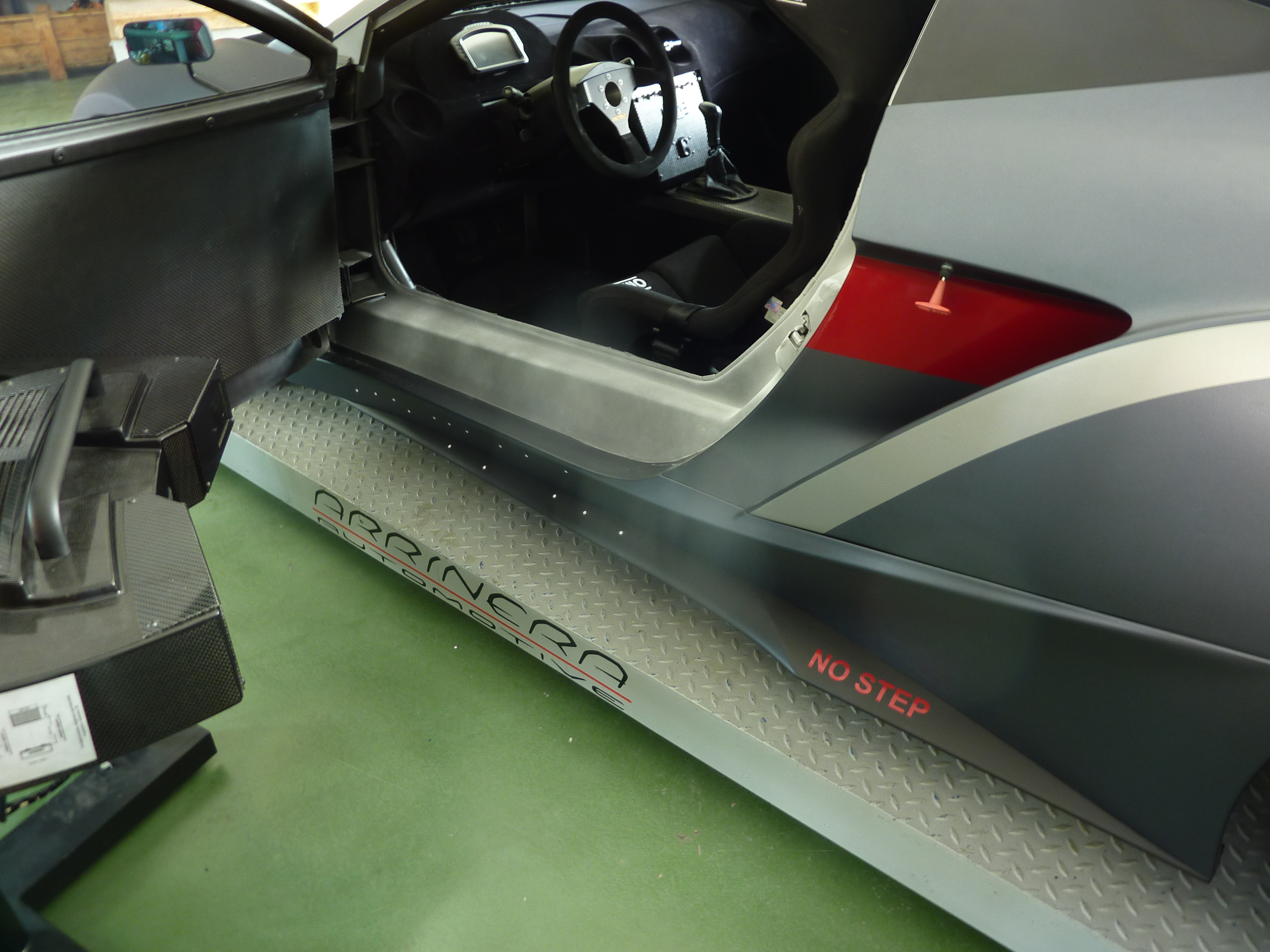
Dane geometryczne istniejącego progu zostały pobrane bezpośrednio z fizycznego prototypu. Arrinera Hussarya została umiejscowiona na platformie, a dostęp do progu utrudniały drzwi samochodu. Ponieważ swoimi wymiarami próg zdecydowanie przekraczał pole pomiarowe skanera 3D, zaistniała potrzeba wykorzystania niezwykle przydatnej funkcji skanowania z użyciem markerów pozycjonujących.
Metoda pomiaru na markery opiera się o umieszczenie na skanowanym obiekcie specjalnych znaczników pozycjonujących. Sterujące skanerem 3D oprogramowanie SMARTTECH3Dmeasure znajduje pięć wspólnych znaczników pozycjonujących, a następnie dopasowuje do siebie pojedyncze pomiary. Operator skanera ma pełen podgląd wykonywanej pracy i z łatwością może „doskanować” kolejne części progu. Ostry kąt pomiędzy układem projekcyjnym a detektorem umożliwił – pomimo kłopotliwych ograniczeń manualnych, pozyskanie dużej ilości danych na temat geometrii.
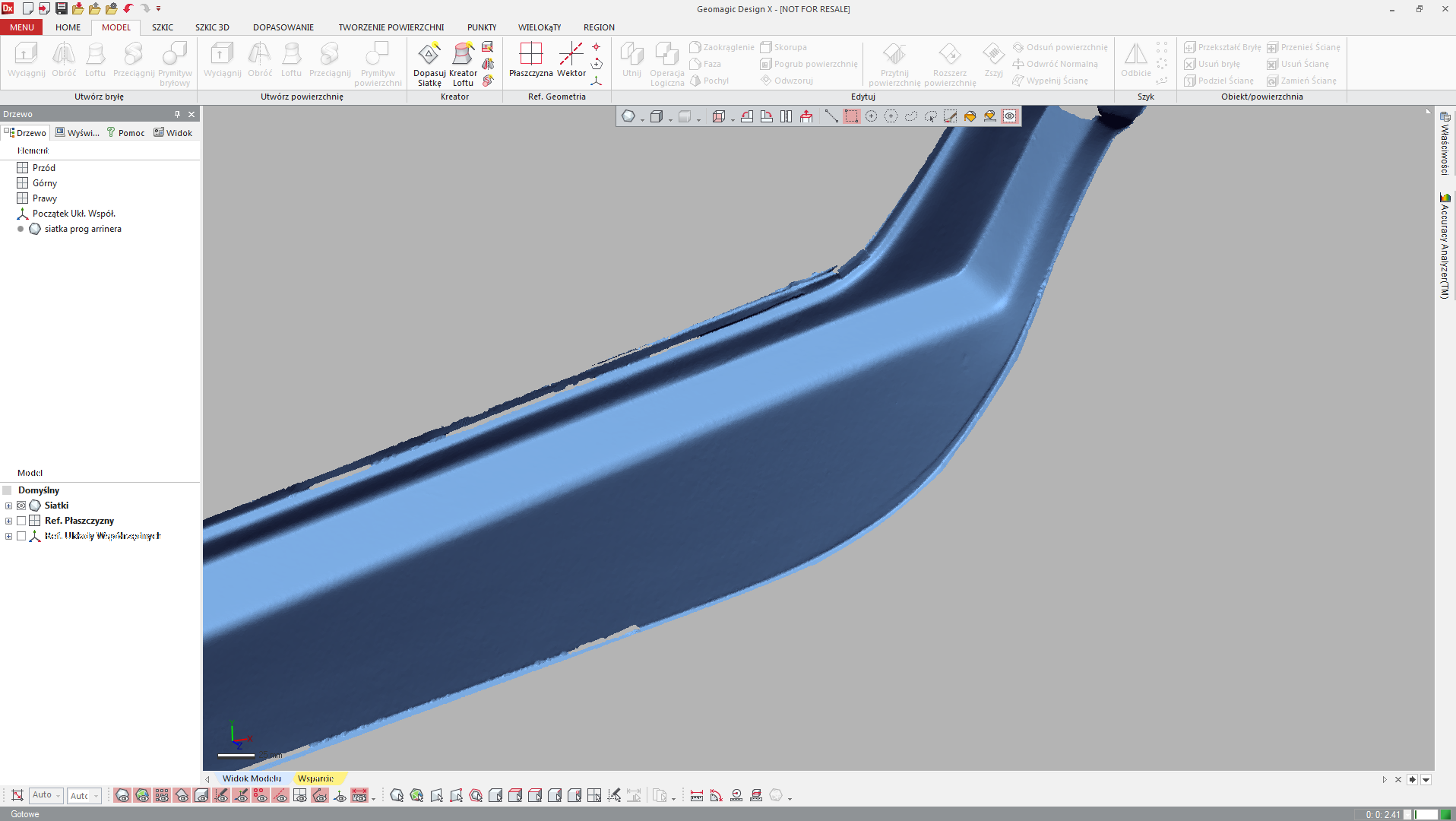
Efektem skanowania 3D z użyciem markerów pozycjonujących jest wstępnie złożona chmura punktów. Dalsza obróbka w SMARTTECH3Dmeasure przebiega za każdym razem podobnie ze względu na intuicyjność i możliwość zautomatyzowania poszczególnych operacji. W tym przypadku również jest niezbędne wykonanie modelu referencyjnego CAD w stosowanym przez Arrinerę oprogramowaniu Geomagic Design X. Taki model jest kompatybilny z wycinarką oraz giętarką, które wytwarzają potrzebne części.
Źródło: materiały prasowe & www.skaner3d.pl