Wytrzymałość materiału jest zwykle testowana przez przy użyciu dedykowanych maszyn wytrzymałościowych, na których przeprowadzane są próby rozciągania. Mały obiekt testowy jest poddawany dużej sile, aż do momentu pęknięcia lub złamania. Siła rzutowana na część podzieloną przez powierzchnię środka pęknięcia w momencie zerwania wyraża jego siłę. Jednakże inżynierowie z UltiMaker, Covestro i Royal Dutch Navy zdecydowali się na niekonwencjonalne podejście, aby sprawdzić ponad wszelką wątpliwość jak mocne mogą być części wydrukowane na drukarkach 3D? Królewska Holenderska Marynarka Wojenna zaproponowała… pojazd opancerzony!
Aby podnieść ciężki pojazd za pomocą części wydrukowanej w 3D, inżynierowie musieli najpierw przeanalizować sprzęt. Królewska holenderska marynarka wojenna miała do dyspozycji specjalistyczny podnośnik, który wykorzystywał dwa otwierane stalowe pierścienie do połączenia z dźwigiem i linami przymocowanymi do podnoszonego pojazdu. Aby je połączyć stworzono wydłużone ogniwo w kształcie litery O.
Po zaimportowaniu geometrii stalowych pierścieni do oprogramowania CAD inżynier aplikacji w UltiMaker – Lars De Jongh, stworzył wstępny projekt połączenia. Aby projekt działał, łącze wymagało płaskiej strony w celu uzyskania stabilnego wydruku 3D i musiało być wydrukowane z liniami warstw w tym samym kierunku, w którym siły rzutowane na część. Współdziałająca powierzchnia części i metalowe pierścienie musiały być jak największe, aby równomiernie rozłożyć siły.
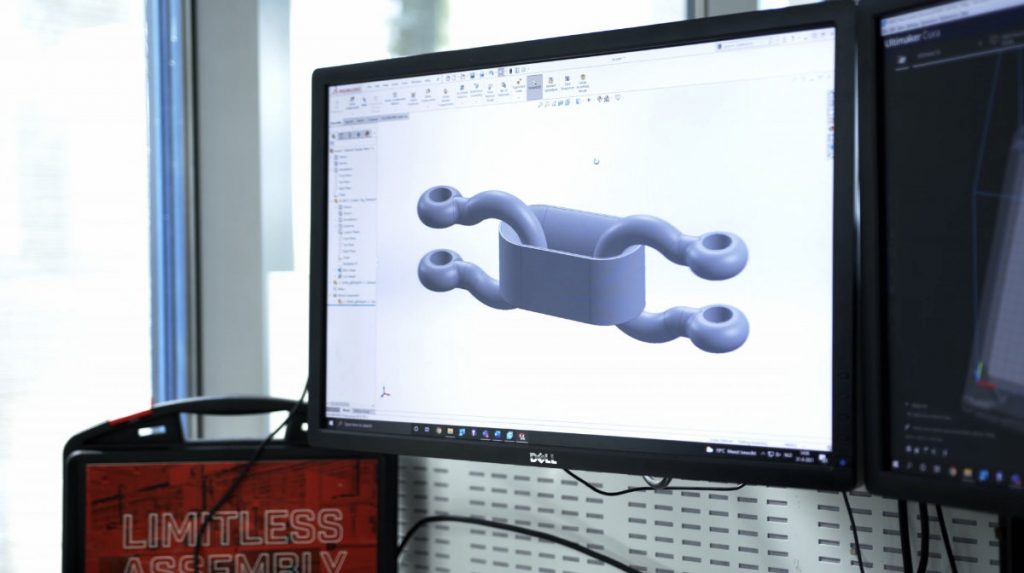
Inżynierowie potrzebowali wyjątkowo mocnego materiału, który mógłby pochłaniać krótkotrwałe siły szczytowe. Ostatecznie zdecydowano się na filament Addigy F1030 CF10 firmy Covestro, który spełniał założone wymagania. Jest to polimer na bazie poliamidu domieszkowany włóknem węglowym i może być drukowany za pomocą drukarek 3D klasy desktopowej – UltiMaker postanowił wykorzystać do tego swój model urządzenia – S5.
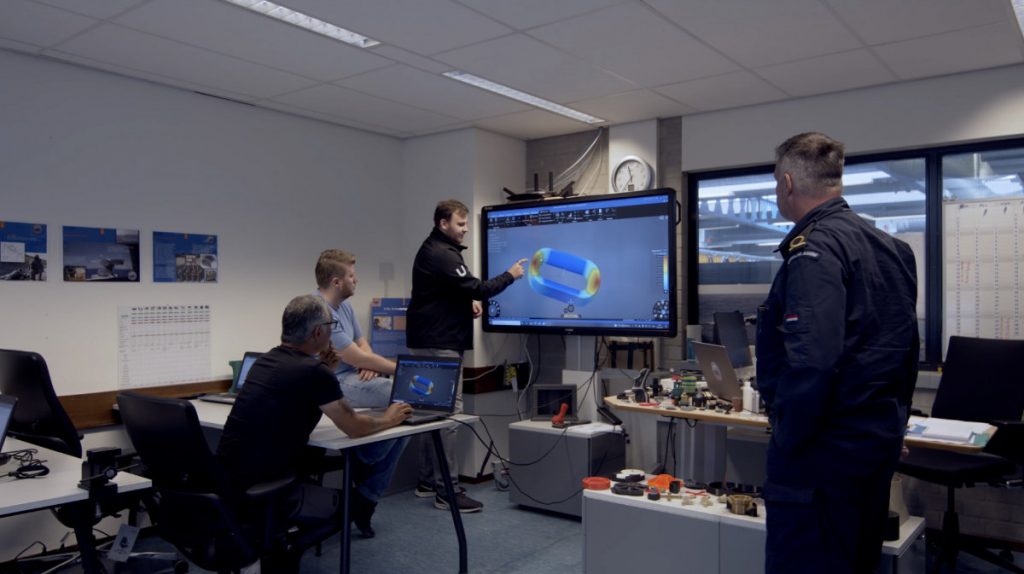
Zanim ciężki pojazd mógł zostać podniesiony, inżynierowie musieli fizycznie zweryfikować obliczoną wytrzymałość części. Wygenerowano dwa projekty dla dwóch rozmiarów. Pierwszym było ogniwo 1 kg, szacowane na 12 ton. Drugi, ważący blisko 3 kg, został oszacowany na 38 ton. Testy przeprowadzono za pomocą stacjonarnego przemysłowego testera rozciągania należącego do marynarki wojennej, który jest w stanie rzutować na obiekt siłę do 343 kiloniutonów.
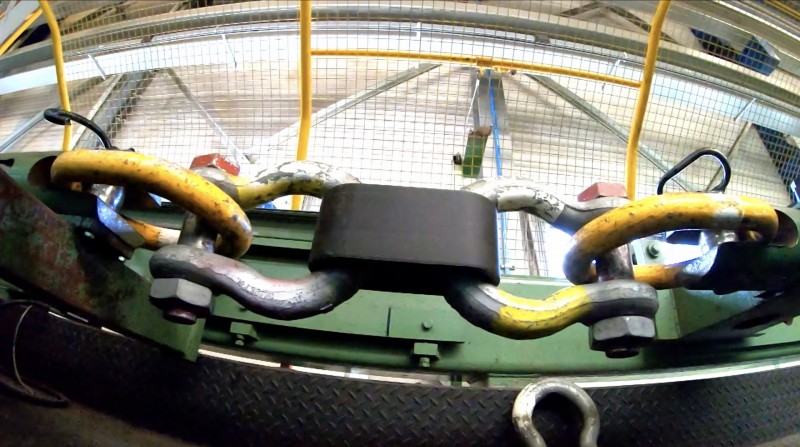
Różnica między testowanymi wynikami a symulowanymi wartościami była bliska, średnio tylko o 1%. Dzięki temu przepływ pracy był dokładny i opłacalny pod względem czasu wprowadzenia produktu na rynek i zwiększonej wydajności. Po kilku miesiącach projektowania, drukowania 3D, testowania i planowania przyszedł czas na działanie. Do podniesienia pojazdu użyto Leoparda 2 „Buffalo” wyposażonego w dźwig, który jest przeznaczony do odzyskiwania ciężkich pojazdów, takich jak ciężarówki i czołgi bojowe.
Na początku ogniwo zostało użyte do podniesienia wojskowej wersji jeepa Mercedesa ważącego ponad dwie tony. Ten pojazd został podniesiony z łatwością.
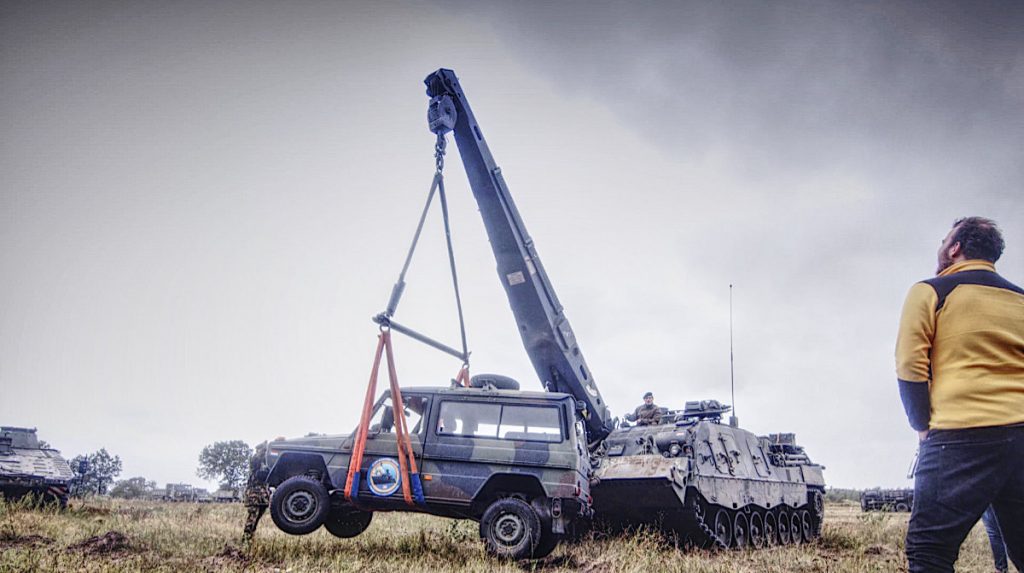
Dwukilogramowe, wzmocnione włóknem węglowym ogniwo zostało następnie umieszczone między opancerzonym czołgiem M113, a Buffalo. Metalowe pierścienie zostały zaciśnięte na miejscu, a od dolnego haka do pojazdu przymocowano cztery kable. 12-tonowy pojazd został powoli podniesiony, zawieszony na wydrukowanym w 3D ogniwie. Następnie Buffalo poruszał się w różnych kierunkach, a połączenie trzymało się idealnie.
Całość operacji można obejrzeć na poniższym video:
Źródło: www.ultimaker.com
Zdjęcia: www.ultimaker.com (materiały prasowe / wszystkie prawa zastrzeżone)