Jak wielokrotnie o tym pisaliśmy, Holandia to bez dwóch zdań jeden z najważniejszych ośrodków związanych z drukiem 3D w Europie. Z liczącego zaledwie 17 mln mieszkańców państwa wywodzą się m.in. takie firmy jak Ultimaker, Leapfrog, FelixRobotics, colorFabb, czy Formfutura, które od wielu lat nadają ton rozwoju całej branży desktopowego druku 3D. Kolejnym graczem, który ma nadzieję podbić świat swoimi produktami jest 3DEVO. Co ciekawe, w przeciwieństwie do w/w, firma oferuje coś zupełnie innego i nietypowego…
3DEVO jest producentem wytłaczarek do filamentów – jednakże w przeciwieństwie do większości tego typu urządzeń, które próbowały swojego szczęścia w minionych latach na rynku wyróżnia się zupełnie innym podejście. Wytłaczarka NEXT oraz kompatybilna z nią stacja do rozdrabniania plastiku SHR3D IT są dedykowane użytkownikom profesjonalnym – i jak zapewnia producent, zapewniają taką samą jakość wyprodukowanych materiałów eksploatacyjnych.
3DEVO ma zamiar wkrótce wejść na polski rynek. Skontaktowałem się zatem z CEO firmy – Timem Wesselnkiem i poprosiłem go, aby przedstawił swoje produkty polskim czytelnikom, pomógł zrozumieć wizję firmy, którą kieruje, a przede wszystkim przedstawił plany jakie ma wobec naszego kraju w kontekście swoich maszyn…

Paweł Ślusarczyk: Wasza firma specjalizuje się w produkcji urządzeń, które nazywacie „pierwszymi na świecie, profesjonalnymi wytłaczarkami do filamentu„. Skąd pomysł na tego typu produkt?
Tim Wesselink: W 2012 roku założyliśmy biuro konstrukcyjne gdzie realizowaliśmy mnóstwo projektów, dedykowanych dla takich gałęzi przemysłu jak automatyzacja, roboty spawalnicze, systemy do pakowania, rozwój produktu, czy szybkie prototypowanie. Wykorzystując maszyny przemysłowe opracowywaliśmy na małą skalę różnego rodzaju prototypy. Dość szybko trafiliśmy na drukarki 3D i zauważyliśmy jak ta metoda może zaoszczędzić nam koszty i czas w prototypowaniu, chociaż równocześnie filament do drukarek 3D, który musieliśmy nabyć okazywał się być dość kosztowny w przypadku małych projektów. Ceny surowych tworzyw sztucznych są ułamkiem ceny gotowych filamentów, co naszym zdaniem stanowi ich główną wadę.
Odkryliśmy, że dużym liniom produkcyjnym brakuje swoistej elastyczności – aby przetestować i wyprodukować nową mieszankę, trzeba było wykorzystać minimum 2 kg materiału, operator linii potrzebował specjalnej wiedzy do jej obsługi, a i jej koszt był dość wysoki. Dlatego pomyśleliśmy: „dlaczego nie połączyć technologii desktopowej, naszego nie-polimerowego doświadczenia i połączyć to wszystko z technologiami przemysłowymi, których używaliśmy, gdzie efektem końcowym będzie redukcja skali i szybkości w pozyskiwaniu nowego tworzywa?” Wynik: pierwszy prototyp w maju 2014 r. naszego własnego 3D extrudera do filamentów.
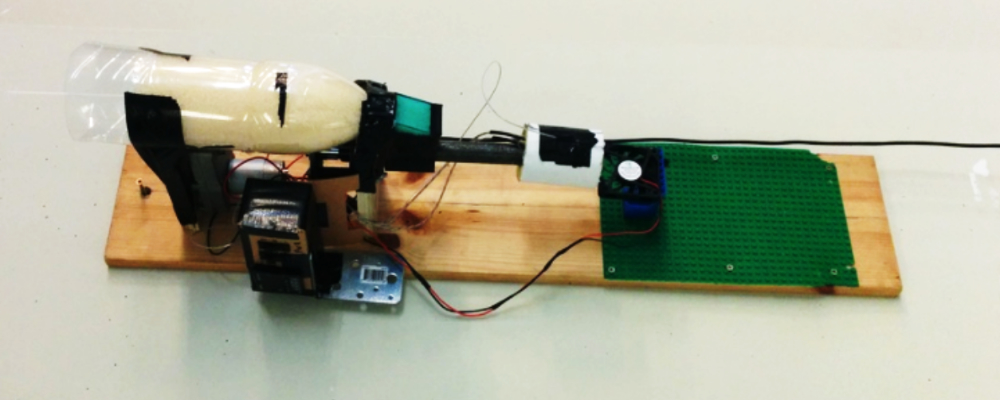
PŚ: Czy mieliście jakieś wcześniejsze doświadczenia w produkcji tworzyw sztucznych?
TW: Nie. Zaczynaliśmy jako inżynierowie mechanicy. Poszerzyliśmy nasz zespół o specjalistów z obszaru elektroniki i oprogramowania. Specjalnie poszukiwaliśmy osób, które nie posiadają wiedzy w zakresie przetwórstwa tworzyw sztucznych, którzy będą obsługiwać naszą maszynę i mimo to będą uzyskiwać dzięki niej świetne rezultaty.
Mieliśmy jednak dużą wiedzę na temat tego jak powinna działać maszyna do wytwarzania filamentu, jak jest zbudowana i czego potrzebuje.
PŚ: Jakie kamienie milowe możesz wymienić jako najważniejsze w rozwoju firmy?
TW: Pierwszy prototyp: maj 2014 r., założenie firmy: 6 czerwiec 2016 r., pierwszy komercyjny sukces: wrzesień 2016 r., premiera drugiej maszyny – SHR3D IT: marzec 2017 r.
PŚ: Czy mógłbyś własnymi słowami opisać czym jest Wasza maszyna? Do czego służy?
TW: Nasz produkt jest skierowany do osób, którzy chcą tworzyć własny filament do drukarek 3D, bądź zrecyklingować resztki filamentu, lub stare, bądź nieudane wydruki 3D wykonane z plastiku. Zatem po pierwsze jest to badanie i tworzenie nowych rodzajów materiałów. Daje to niejako dodatkowy, czwarty wymiar pracy z drukarką 3D – możesz zaszaleć i dodać różne mieszanki. Dokładnie jak opisują to nasi klienci: to maszyna do produkcji filamentu.
ZOBACZ: porównanie urządzeń 3DEVO
Po drugie jest to narzędzie do bieżącej produkcji materiału na własne potrzeby i zmniejszanie kosztów własnych. Po trzecie, to urządzenie do recyklingu resztek poprodukcyjnych – jest to coś na czym teraz przede wszystkim się skupiamy z naszym nowym produktem – SHR3D IT. Jest to swoisty „miniaturowy zakład recyklingu” tworzyw sztucznych. Źródłem pomysłu był fakt, że druk 3D generuje mnóstwo odpadów – czy to w postaci nieudanych, bądź niewykorzystanych prototypów, czy nieudanych wydruków w ogóle.
Używanie naszej maszyny to nie zaparzanie kawy w ekspresie… Jest to proces przemysłowy, który wymaga chwili czasu aby się z nim zapoznać, ale odpowiednie przeszkolenie i praktyka sprawią, że ostatecznie uda się odnieść pożądane efekty. Nie będziemy produkować 10 szpul filamentu na godzinę, ale jedną – za to o przemysłowej jakości.
PŚ: Czy urządzenie jest głośne podczas pracy? Czy proces wytwórczy jest „brudny„?
TW: Wczesne prototypy były bardzo głośne – szczególnie wentylatory. Teraz urządzenie jest nieco głośniejsze niż komputer PC i równie głośne co przeciętna drukarka 3D typu FDM. Jakkolwiek niszczarka do plastiku wydaje mnóstwo hałasu, co ma związek również z samym materiałem, który jest rozdrabniany. Tego z pewnością nie należy używać w ciasnym pomieszczeniu.
Czy proces jest „brudny„? I tak i nie, produkcja nowego materiału może być brudna. Jeśli zmiksuje się różne materiały, a nie będzie znało się właściwych ustawień, może to skończyć się spaleniem materiału lub wyprodukowaniem odpadów. Poza tym, jest raczej czysty, wszystko jest łatwo dostępne. W zależności od tego jak będzie się pracować, proces może być czysty lub brudny. Zawsze znajdzie się ktoś, kto sprawi, że będzie brudny…
SHR3D IT jest brudne, ale można z łatwością oczyścić każdy komponent maszyny dzięki temu w jaki sposób jest zbudowana. Z pewnością praca jest czysta w porównaniu do przemysłowych linii. To samo dotyczy NEXT.
PŚ: Co z jakością filamentu? Nie sądzisz, że gdyby jego produkcja była tak prosta i nie wymagałaby specjalistycznej wiedzy chemicznej, nie potrzebowalibyśmy producentów filamentów?
TW: Żeby osiągnąć dobrą jakość materiału, staraliśmy się uprościć proces produkcyjny tak bardzo jak tylko się dało. Każdego dnia możemy testować mnóstwo nowych związków i materiałów, ale nie ma na to czasu. Mimo to, jeśli poprawnie skonfiguruje się nasz sprzęt, otrzyma się tolerancję na poziomie przemysłowym. PLA, ABS, PETG, TPU, PC, PEEK – jeśli wiesz jak to zrobić, znajdziesz na to jakiś sposób.
Oczywiście znajdą się trudne materiały, lecz będą one równie trudne do wyprodukowania także przy pomocy przemysłowych linii produkcyjnych. Mamy system optyczny, który reguluje prędkość procesu tak samo jak w przypadku przemysłowego sprzętu. Każdy powinien poradzić sobie z obsługą oprogramowania naszych wytłaczarek. Istnieje protokół oprogramowania, który mierzy każdy aspekt procesu wytwórczego i system sprzęgieł, który kontroluje napięcie nawijania filamentu.
Producenci filamentu będą istnieć zawsze z uwagi na aspekt ekonomiczny i skali, jednakże w kwestii jakości będzie to bardzo zbliżone do tego, co uda się osiągnąć na NEXT.
PŚ: Ile filamentu mogę wyprodukować w ciągu 24 godzin?
TW: Zależy od materiału? Na naszej stronie internetowej podajemy, że od 0,75 do 1 kg na godzinę, lecz im bardziej schłodzi się materiał podczas wytłaczania, tym szybciej będzie on produkowany. Maksymalna prędkość to 1,5 – 2 kg na godzinę, ale będzie to oznaczało dostarczenie od 24 do 36 kg materiału, ale to wszystko zależy od kontroli temperatury i tzw. „Melt Flow Index” (współczynnik płynięcia przetopionego materiału).
PŚ: Kto jest Waszym idealnym klientem? Firma czy użytkownik indywidualny?
TW: Uczymy się tego każdego dnia, ponieważ jesteśmy na rynku dopiero pierwszy rok. Mamy wielu zadowolonych klientów z działów R&D i uczelni wyższych, którzy mogą poszerzyć swoje badania dzięki naszej maszynie. Współpracujemy także z mnóstwem firm specjalizujących się w polimerach, które mają zamiar rozpocząć produkcję filamentów do drukarek 3D i używają naszych produktów do tworzenia krótkich serii testowych.
Klient przemysłowy wykorzystuje je do badań nad materiałem wykorzystywanym w produkcji części mechanicznych dla branży motoryzacyjnej lub lotniczej. Sprawdzają, czy będą w stanie drukować je z własnego materiału? Jeśli możesz wydrukować rzecz z dokładnie tego samego materiału, który jest używany we wtrysku, jesteś dużo bliżej finalnej produkcji części w technologii druku 3D.
Ponadto użytkownicy dużych drukarek 3D, czy farm drukarek 3D, które potrzebują dużo materiału. Mamy wielu klientów korzystających z możliwości recyklingu – otrzymujemy sporo zainteresowania ze strony szkół.
Znakomita większość naszych klientów to firmy lub instytucje – nasze maszyny są zbyt skomplikowane dla użytkowników indywidualnych.
PŚ: Prowadzę firmę produkcyjną i wykorzystuję w pracy drukarkę 3D – dlaczego miałbym zainwestować pieniądze w Wasz produkt?
TW: Jeśli używasz mnóstwa materiałów eksploatacyjnych, możesz zoptymalizować ich użycie w procesie druku 3D. Jeśli chcesz użyć w swoim materiale jakichś specjalnych włókien lub chcesz zapewnić mu przewodność elektryczną, oznacz to wejście we wspomniany czwarty wymiar. To element wolności projektowej, jaka wcześniej była dla ciebie niedostępna. Osiągniesz to za pomocą urządzenia desktopowego, bez konieczności zlecenia tej usługi producentowi, który wyprodukuje go na linii produkcyjnej dedykowanej dla produkcji seryjnej.
PŚ: Kilka lat temu żyliśmy wizją (przynajmniej większość z nas…), że osobiste drukarki 3D będą używane przez wszystkich w domach. Jak postrzegasz to z punktu widzenia dnia dzisiejszego? W Polsce użytkownicy indywidualni kupują w większości tanie drukarki 3D z chińskich sklepów pokroju AliExpress lub GearBest. Klientami na profesjonalne, desktopowe drukarki 3D są firmy. Jak to wygląda w Holandii?
TW: W Holandii jest dokładnie tak samo. Większość rynku druku 3D jest skupiona wokół przemysłu. My również wyrośliśmy ze środowiska przemysłowego. Jeśli będę miał dzieci, kupię im tanią drukarkę 3D, żeby miały z nią kontakt. Wiedza na temat możliwości jakie daje wolność projektowania rzeczy nie była do tej pory dostępna. Póki jej jeszcze nie ma, myślimy w kategoriach konwencjonalnych technologii wytwórczych, ale za 10-20 lat ludzie, którzy wychowali się wśród drukarek 3D, będą o tym myśleć zmieniając status quo.
Sektor przemysłowy i rynek profesjonalny są obszarami, które rozwijają się najbardziej dzięki odkryciu nowych nisz technologicznych. Dzięki temu również my mogliśmy opracować i wyprodukować nasze produkty tak szybko. Na chwilę obecną sektor B2B ma największe perspektywy na wdrożenia technologii druku 3D.
PŚ: Nie boicie się konkurencji z Chin? Co jeśli pewnego dnia zobaczycie kopię 3DEVO w 1/3 Waszej ceny?
TW: Oczywiście Chińczycy są szybcy w reprodukcji rzeczy, ale wiemy, że prawidłowe działanie i właściwe użytkowanie jest niezbędne, i nie sprowadza się wyłącznie do sprzętu. Sprzęt jest tylko sprzętem, ale reszta to umiejętności i wiedza. Mamy dużo wiedzy i nadal dążymy do tego, aby jak najwięcej przekazać jej naszym klientom.
PŚ: Z tego co wiem, przygotowujecie się na wejście na polski rynek. Mógłbyś powiedzieć coś więcej na temat tych planów?
TW: Na początek zamierzamy znaleźć odpowiednich partnerów na uczelniach wyższych, jak również partnera biznesowego. Chcemy pomóc im zrozumieć jak działa nasza maszyna oraz jak używać jej by odnieść pożądany efekt. Jest to niezbędne aby zdobyć wiedzę, o której wcześniej wspominałem.
PŚ: Dziękuję za rozmowę.
TW: Dziękuję również.